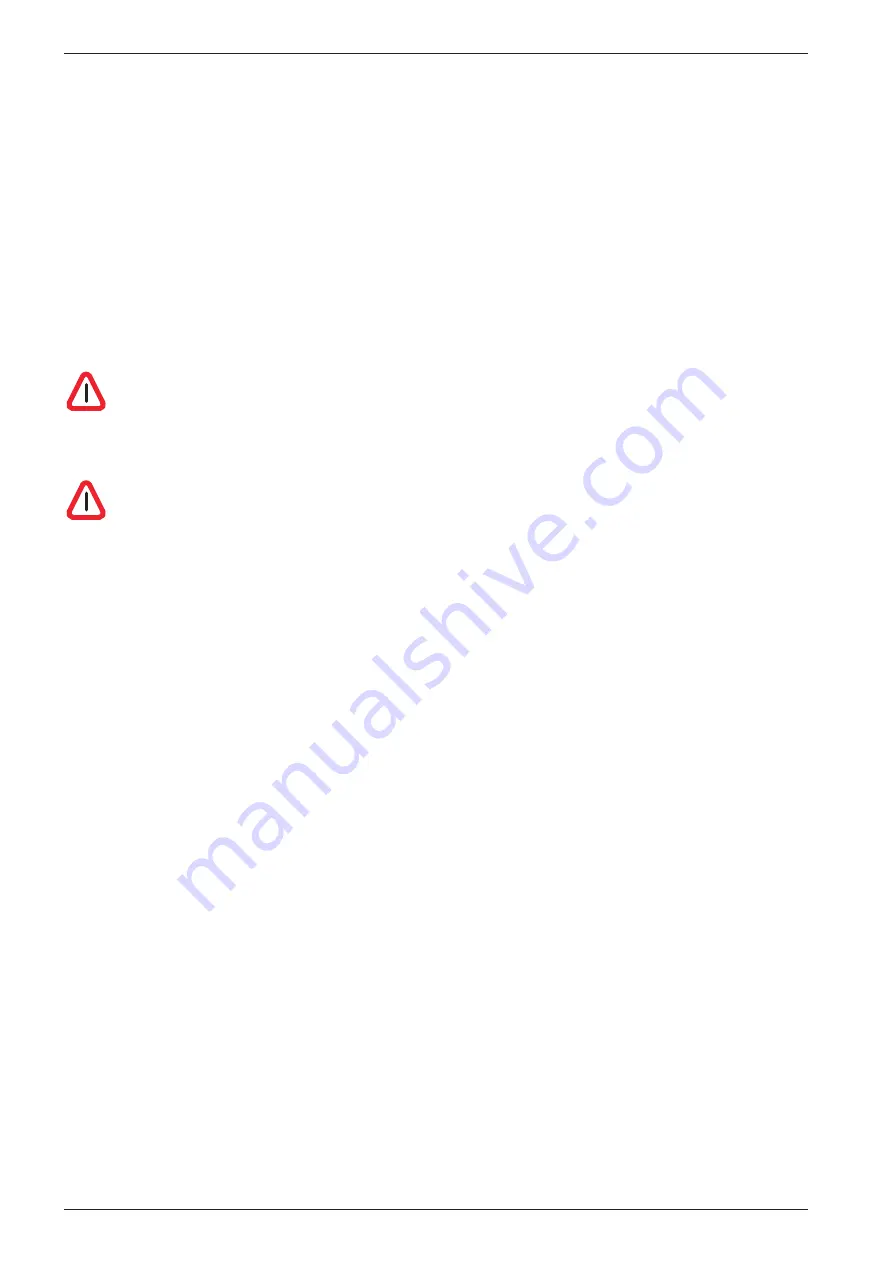
6.5 Escape-sequences
What is an escape-sequence?
An escape-sequence is just a name for a code which is sent to the printer from the computer to change
the parameters which control the way the printer works. All parameters that can be set via the opera-
tor panel, can also be changed with escape-sequences, (except those for the data communication, i.e.
active port, baud rate, data bit, stop bit, and parity).
This makes it possible to have different codes (read; escape-sequences) stored in a document.
So, when the document is sent to the printer, these codes are sent first and the printer sets itself in the
correct mode and format automatically.
Note! When the printer receives an escape-sequence, it will have first priority. This means,
regardless of the setting made before and regardless what the operator panel dictates, the most
recent escape-sequence will take precedence.
Note! Escape-sequences should be placed at the very beginning of the first page on the sheet,
(e.g. page 1, 3, 5, 7 ...). However, a software form feed can be placed wherever needed. (If
there is a command on the other pages, it will be skipped).
All page formatting which is done on the front page will also format the back of the same
sheet. It is for example not possible to have 8 dot Braille on the front page and 6 dot on the
back page. It is possible to mix 6 and 8 dot Braille however, as long as it is done on two differ-
ent sheets.
An overview of the different escape-sequences:
ESC A nn
- Sheet length.
nn can be from 08 to 28 (4 to 14 inches).
ESC B nn
- Line length.
nn can be from 10 to 42 characters.
ESC C n
- Print format. n can be 0 or 1, single-sided (0) or interpoint (1).
ESC H n
- Page layout. n can be 0 or 1, normal (0) or Z-fold printing (1).
ESC I n
- Page 1 up/down. n can be 0 or 1, up (0) or down (1).
ESC J n
- 6 / 8 dot Braille.
n can be 0 or 1, 6 (0) or 8 (1) dot Braille.
ESC M nn
- Line spacing.
nn can be from 0 to 16 step.
ESC N n
- Line single/double. n can be 0 or 1, single (0) or double line spacing (1).
ESC R n
- Page adjust.
n can be from 0 to 9 lines.
ESC S n
- Form feed mode. n can be 0 or 1, no form feed (0) or normal form feed (1).
ESC T nn
- Page margin.
nn can be from 0 to 20 step.
ESC 0
- Soft reset
ESC 1
- Soft form feed
ESC 4
- Printer ID
BRAILLO
l
B 600 SR
98
Summary of Contents for 600 SR
Page 1: ...User s Guide BRAILLO NORWAY BRAILLO 600 SR Rev January 2018...
Page 2: ...2018 Braillo Norway AS...
Page 4: ...BRAILLO l B 600 SR 4...
Page 89: ...Frame exploded view BRAILLO l B 600 SR 89...
Page 114: ...BRAILLO l B 600 SR 114 8 5 Measurements All measurements in centimetres 115 cm 77 cm 112 cm...
Page 115: ...9 GENERAL INFORMATION 9 1 Declaration of conformity BRAILLO l B 600 SR 115...
Page 119: ...BRAILLO l B 600 SR 119...