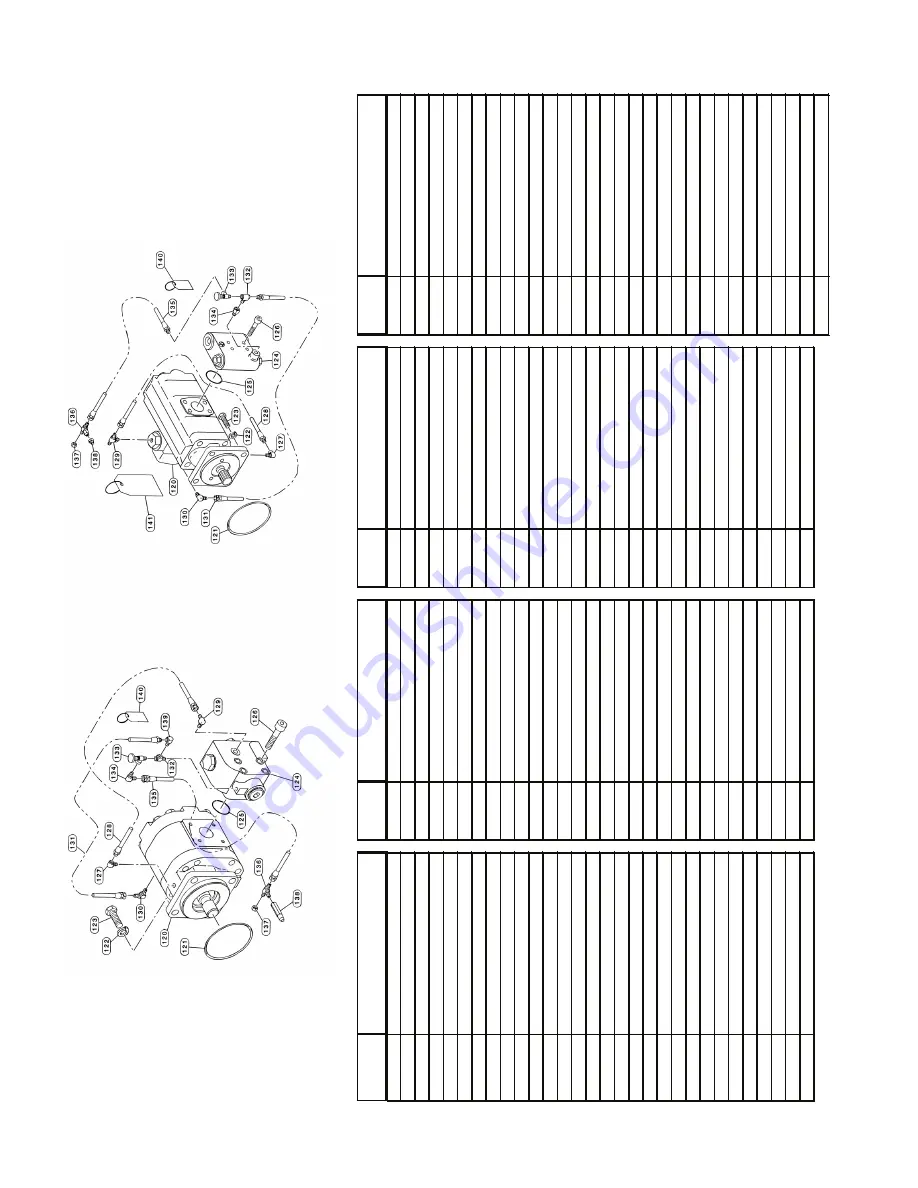
20
Two-speed
Motor
Single-speed
Motor
ITEM
ITEM
ITEM
ITE
M
NUMBE
R
DESCRIPTION
NUMBE
R
DESCRIPTION
NUMBE
R
DESCRIPTIO
NN
UMBE
R
DESCRIPTIO
N
1T
ie Plat
e3
1D
ow
el Pi
n6
7S
econd Stage Planet Carrier
97
Roller Bearin
g
2S
upport End Plat
e3
2P
ipe Plug
68
Planet Pi
n9
8S
pace
r
3O
-Ring Flush Plug
33
Capscrew
69
Th
rust
Wa
sher
99
Sprag Clutch Assembly
4L
ockw
ashe
r4
0T
hrust
Wa
sher
70
Second Stage Planet Gear
10
0S
pace
r
5C
apscrew
41
Th
rust
Wa
sher
71
Loose Roller
s1
01
Internal Retaining Ring
6O
uter Bearing Hu
b4
2
Primary Ring Gear/End Cove
r7
2O
utput Planet Carrie
r1
02
Sprag Clutch Inner Race
7I
nternal Retaining Ring
43
Capscrew
73
Planet Pi
n1
03
Spacer
8R
oller Bearin
g4
4
Lockw
ashe
r7
4B
earing Cone
10
4I
nternal Retaining Ring
9G
rease Fittin
g4
5R
ing Gear
75
Bearing Cu
p1
05
Cable
We
dge (01 & 02 Drum
)
10
Inner Bearing Hu
b4
6D
rain Tube
76
Output Planet Gear
10
6C
able
We
dge (03 & 04 Drum
)
11
Ex
ternal Retaining Ring
47
Plug
77
Bearing Spacer
12
0H
ydraulic
Mo
to
r
12
Seal
48
Split Ring
78
Internal Retaining Ring
12
1O
-Rin
g
13
Seal Carrier
49
Bearing Cone
79
Rollpin
12
2L
ockw
ashe
r
14
O-Ring
50
Bearing Cu
p8
0P
lu
g1
23
Capscrew
15
Lockw
ashe
r5
1B
earing Cu
p8
1I
nternal Retaining Ring
12
4B
rake Valv
e
16
Capscrew
52
Bearing Cone
82
Brake Spacer/Support Plat
e1
25
O-Ring
17
Capscrew
53
Me
tal Face Seal
83
Steel Brake Disk
12
6C
apscre
w
18
Lockw
ashe
r5
4V
ent Plug
84
Friction Brake Disk
12
7R
educer Elbo
w
19
Sight Gauge
55
Primary Sun Gear
85
Mo
tor Support/Brake Cylinder
12
8H
ydraulic
Hose
20
Capscrew
56
Ex
ternal Retaining Ring
86
Back-Up Ring
12
9E
lbow
Fittin
g
21
Cover Plat
e5
7T
hrust
Wa
sher
87
O-Ring
13
0E
lbow
Fittin
g
22
O-Ring
58
Second Stage Sun Gear
88
O-Ring
13
1H
ydraulic
Hose
23
Cable Drum
59
Primary Planet Carrie
r8
9B
ack-Up Ring
13
2T
ee Fitting
24
O-Ring
60
Planet Pi
n9
0
Brake Piston
13
3N
eedle Valv
e
25
Mo
tor End Plat
e6
1T
hrust
Wa
sher
91
Brake Spring
13
4E
lbow
Fittin
g
26
O-Ring
62
Primary Planet Gear
92
Brake Piston Stop
13
5H
ydraulic
Hose
27
Mo
tor Adapte
r6
3
Loose Roller
s9
3S
pring Stop
13
6M
ale Branch
Te
e Fitting
28
Mo
tor Couplin
g6
4R
ollpin
94
Internal Retaining Ring
13
7C
ap Nu
t
29
Capscrew
65
Th
rust
Wa
sher
95
Bushin
g1
38
Nipple
30
Lockw
ashe
r6
6O
utput Sun Gear
96
Sprag Clutch Outer Race
13
9E
lbow
Fittin
g
14
0W
arning
Ta
g
Summary of Contents for CH330
Page 2: ...2...