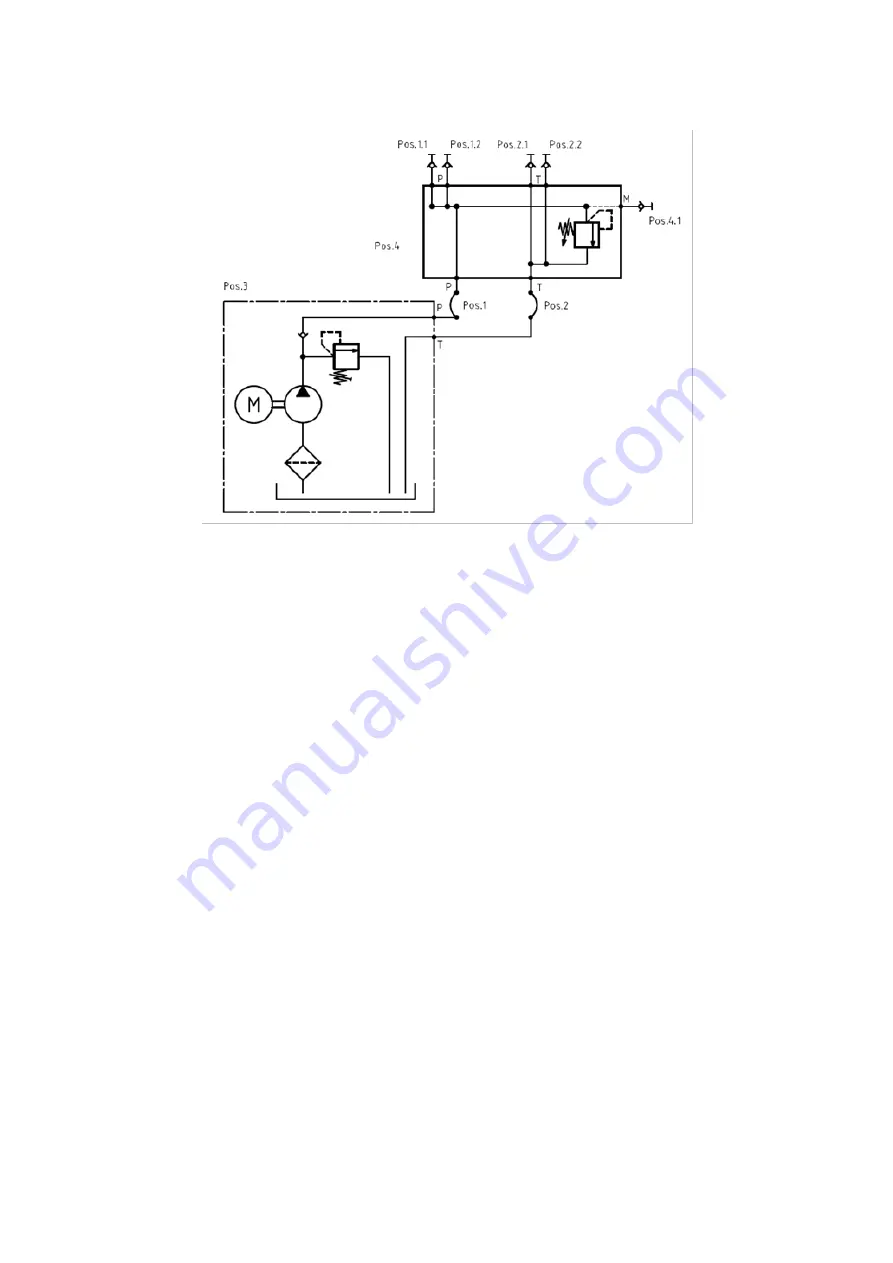
Assembly of the WS200 work station 57/92
DCA_DE_000151/10-2013, WS200,
Bosch Rexroth AG
1 Pressure line
1.1 / 1.2 Coupling connector - port P
2 Line to the tank
2.1 / 2.2 Coupling connector - port T
3 ANTRIEBSAGGREGAT TS-WS200 220V/50HZ 1X
4 P/T distributor
4.1 Minimess coupling - connection of the hydraulic measuring line
Fig. 41:
Hydraulic circuit schematic WS200
Summary of Contents for Rexroth WS200
Page 1: ...WS200 work station Operating instructions DCA DE 000151 10 2013 Replaces English ...
Page 85: ...Appendix 85 92 DCA_DE_000151 10 2013 WS200 Bosch Rexroth AG ...
Page 86: ...86 92 Appendix Bosch Rexroth AG WS200 DCA_DE_000151 10 2013 ...
Page 87: ...Appendix 87 92 DCA_DE_000151 10 2013 WS200 Bosch Rexroth AG ...
Page 88: ...88 92 Appendix Bosch Rexroth AG WS200 DCA_DE_000151 10 2013 ...
Page 89: ...Appendix 89 92 DCA_DE_000151 10 2013 WS200 Bosch Rexroth AG ...
Page 90: ...90 92 Appendix Bosch Rexroth AG WS200 DCA_DE_000151 10 2013 ...
Page 91: ...Appendix 91 92 DCA_DE_000151 10 2013 WS200 Bosch Rexroth AG 15 2 Declaration of conformity ...