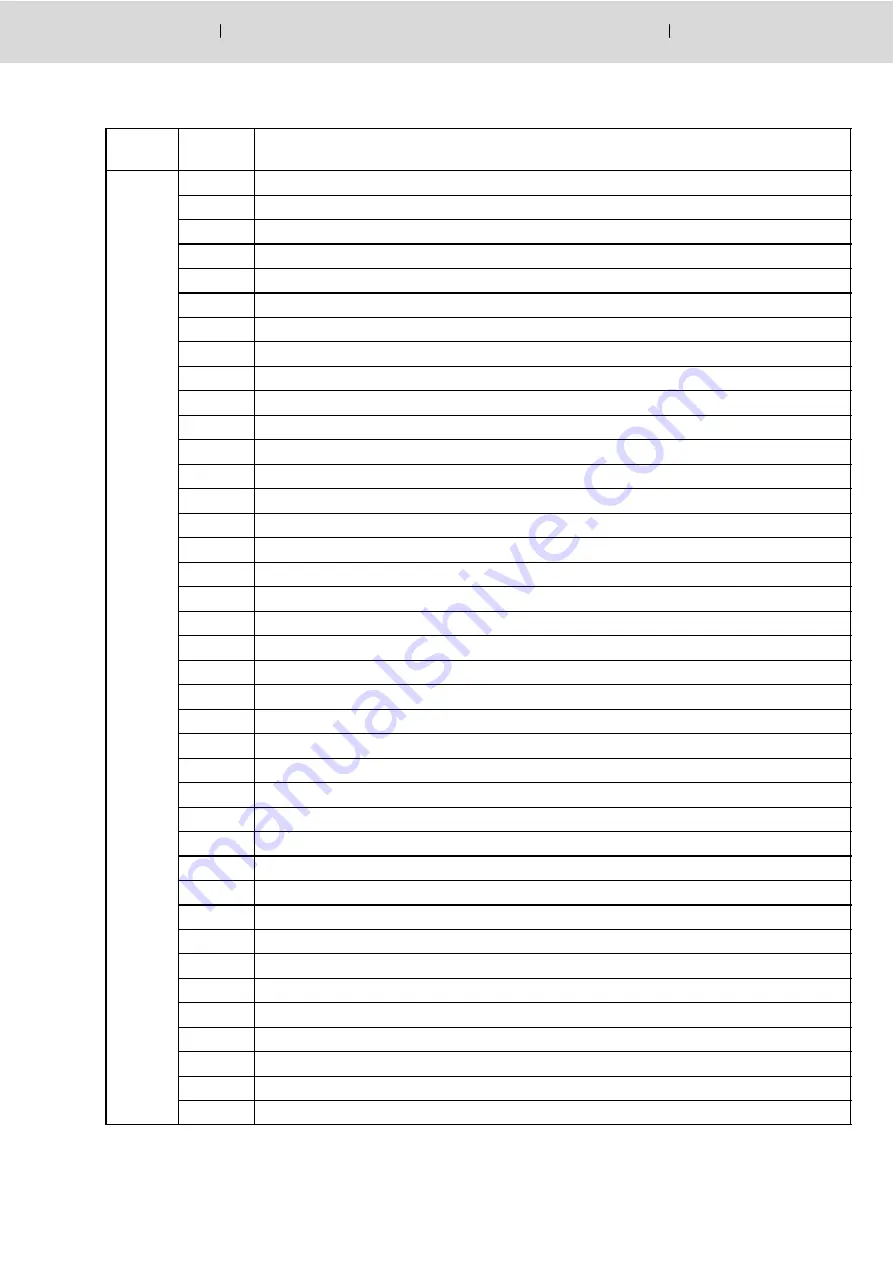
Electric Drives
and Controls
4–23
Bosch Rexroth AG
Servodyn-D
1070 066 032 / 03
VMA..KR, VMA..B,C,D,F and DM/DS error displays
F code
display
Meaning
Error
number
F70
1351
Motor rating plate: Parameter set 2: Pole pitch = 0
1352
Motor rating plate: Parameter set 2: Speed: Nominal value = 0
1353
Motor rating plate: Parameter set 2: Speed: Maximum = 0
1354
Motor rating plate: Parameter set 2: Force: Nominal thrust = 0
1355
Motor rating plate: Parameter set 2: Force: Standstill thrust = 0
1356
Motor rating plate: Parameter set 2: Force: Max. thrust = 0
1357
Motor rating plate: Parameter set 2: Primary Resistance = 0
1358
Motor rating plate: Parameter set 2: Transportable load = 0
1359
Motor rating plate: Parameter set 2: Signal periods length = 0
1360
Motor rating plate: Parameter set 2: Distance between reference marks = 0
1361
Motor rating plate: Parameter set 2: Step distance = 0
1362
Motor rating plate: Parameter set 2: Distance between reference marks = 0
1363
Motor rating plate: Parameter set 2: Thrust constant value 1 = 0
1364
Motor rating plate: Parameter set 2: EMF constant = 0
1365
Motor rating plate: Parameter set 2: Series inductance = 0
1366
Motor rating plate: Parameter set 2: Shunt inductance = 0
1367
Motor rating plate: Parameter set 2: Leakage inductance primary winding = 0
1368
Motor rating plate: Parameter set 2: Leakage inductance secondary winding = 0
1369
Motor rating plate: Parameter set 2: Second. resistance = 0
1370
Multiturn value: Different rating plate info & Mfg. specifications; Motor set 2
1371
Singleturn value: Different rating plate info & Mfg. specifications; Motor set 2
1372
Encoder pulses: Different rating plate info & Mfg. specifications; Motor set 2
1373
Singleturn value: Different rating plate info & Mfg. specifications; Motor set 2
1374
Encoder pulses: Different rating plate info & Mfg. specifications; Motor set 2
1375
No. of ref. marker periods:Different rating plate info <–> Mfg. specs;Motor set2
1376
Encoder pulses: Different rating plate info & Mfg. specifications; Motor set 2
1377
Encoder pulses: Different rating plate info & Mfg. specifications; Motor set 2
1378
Signal period length:Different rating plate info &Mfg. specifications;Motor set2
1379
Steps distance : Different rating plate info & Mfg. specifications; Motor set 2
1380
Signal period length:Different rating plate info&Mfg. specifications; Motor set2
1381
Signal period length:Different rating plate info&Mfg. specifications;Motor set2
1382
Ref. marker spacing:Different rating plate info & Mfg. specifications;Motor set2
1383
Signal period length:Different rating plate info &Mfg. specifications;Motor set2
1384
Ref. marker spacing:Different rating plate info & Mfg. specifications;Motor set2
1385
1st Ref. marker position: Different rating plate info & Mfg. specs;Motor set 2
1386
Encoder pulses: Different rating plate info & Mfg. specifications; Motor set 2
1387
Encoder pulses: Different rating plate info & Mfg. specifications; Motor set 2
2201
Flash rating plate: Parameter set 1: Motor type = 0
2202
Flash rating plate: Parameter set 1: Version number = 0