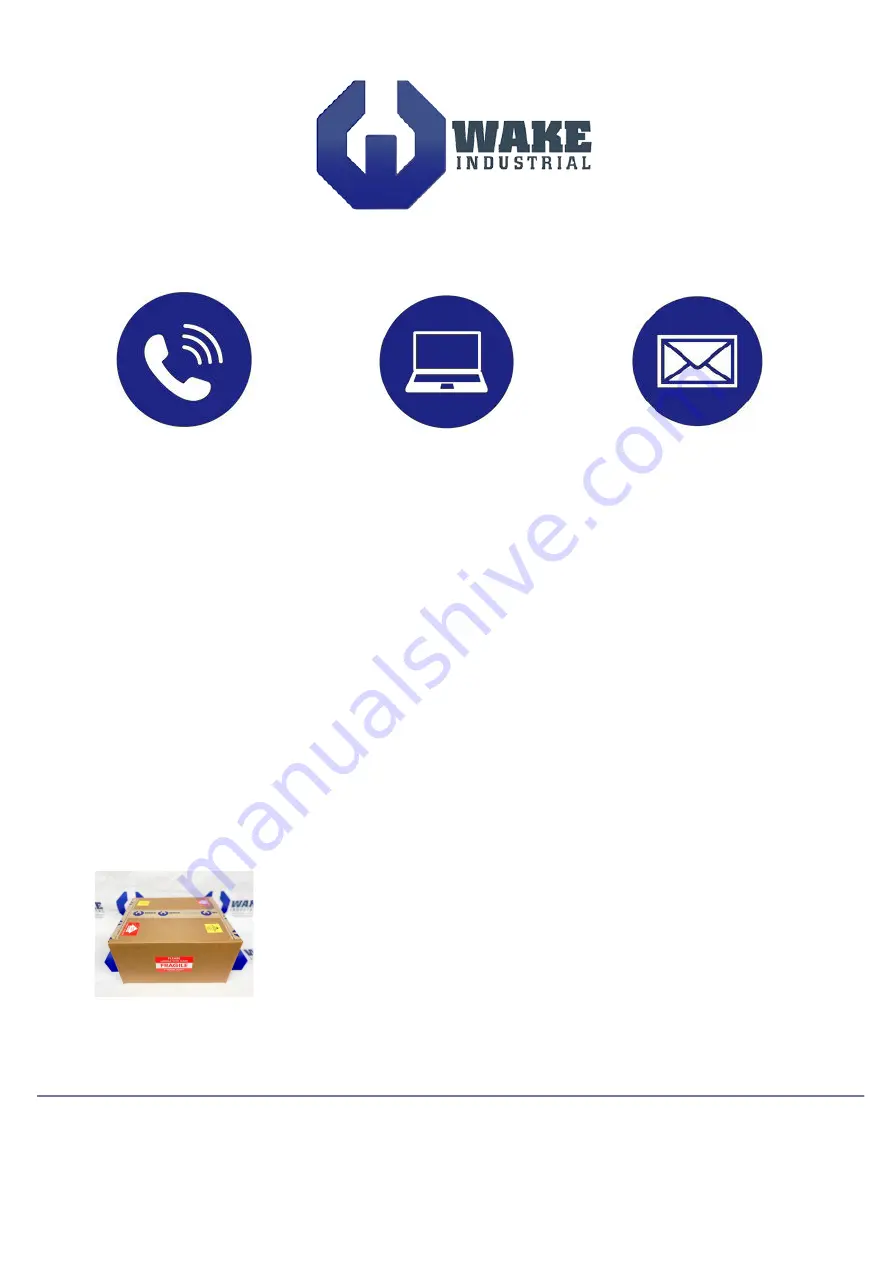
Email Us
We ship worldwide, offering
any type of shipping method
with all the major logistic
companies such as FedEx,
UPS, DHL, USPS, and a
variety of freight carriers.
Stay In Touch
Wake Industrial, LLC
1620 Old Apex Road
Cary, NC 27513
Call:
1-888-551-3082
International:1-919-443-0207
Fax:1-919-267-1705
Email:
Website:
Damage Free Delivery
All of our products are cleaned, go through quality control and are
shipped using a custom military
grade foam to ensure your product
arrives undamaged.
We have the capability to ship both
small
1lb products and large 200lb+
automation parts
regardless of your location.
Visit Our Website
Wake Industrial is not affiliated
with nor an authorized distributor
or representative of any
manufacturers, brands or
products listed.
All Products from Wake Industrial, LLC, come with:
Sales and Repairs Fast Shipping
Quality Guarantee
With standards like our 1 year
warranty on ALL products, we
can
guarantee
a
better
customer service experience
than any other company
within
our industry.
8 a.m. - 5 p.m. Sales Available
International: 1-919-443-0207
Toll Free: 1-888-551-3082
We specialize in providing
immediate product delivery
when your system goes
down. We have thousands
of
In-Stock
automation
products and offer a full
range of repair options.