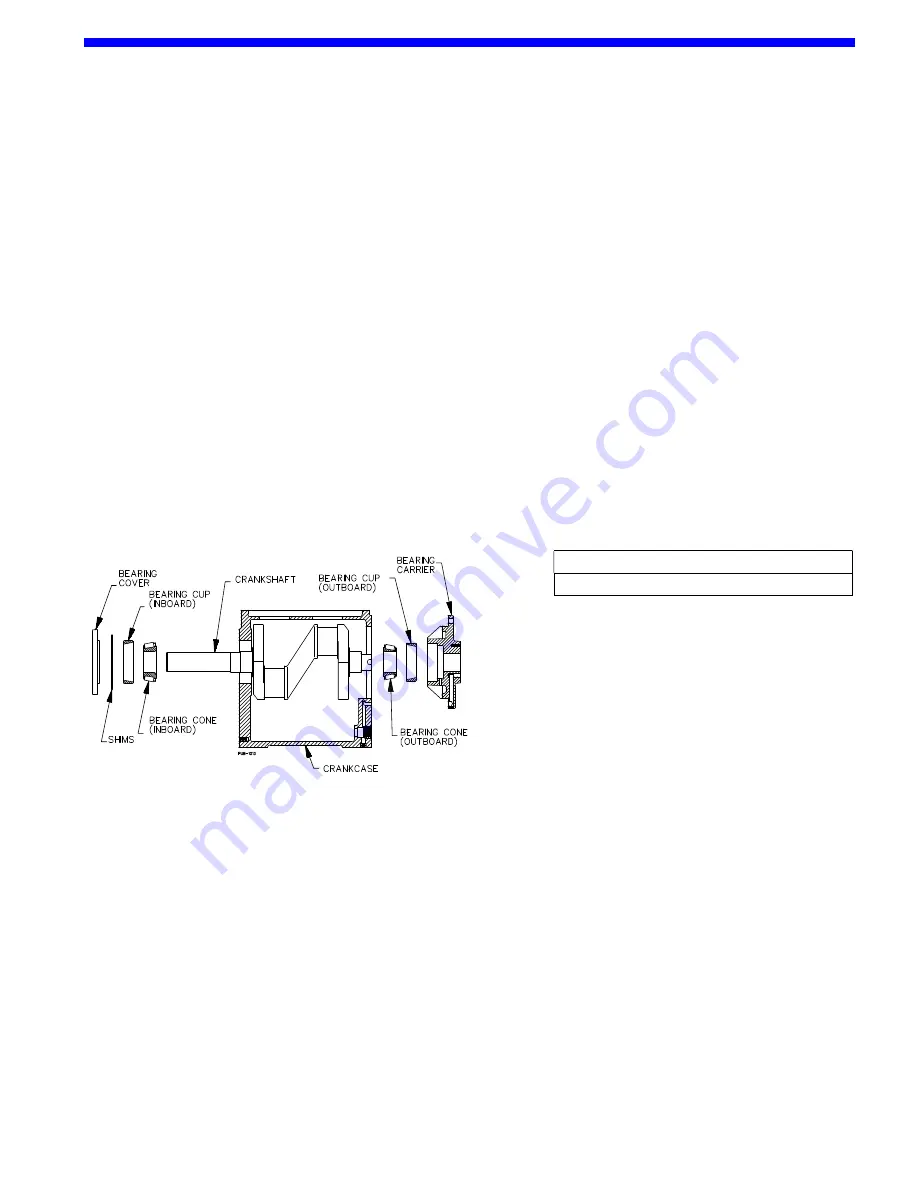
BEARING REPLACEMENT
CB5A-021 page 21/24
NOTICE: When replacing the bearings, the entire
bearing assembly, including the bearing cup and the
bearing cone, must be replaced and the crankshaft
endplay must be readjusted.
1. Follow steps 1 through 12 of the "Compressor
Disassembly" section.
2. Remove the Oil Pump per the section titled "Oil
Pump Replacement."
3. Remove the flywheel.
4. Remove the bearing carrier and gasket from the
outboard end of the crankcase. The outboard
bearing cup will come off with the bearing carrier and
will need to be removed with a bearing removal tool.
5. Remove the key from the crankshaft and slide the
crankshaft through the outboard end of the
crankcase. The bearing cones can then be removed
with a bearing puller.
6. Remove the bearing cover plate from the inboard
end of the crankcase. The inboard bearing cup is
pressed into the crankcase and can be removed with
the use of a bearing removal tool.
7. To install the bearings:
a. Grease the outer edges of the bearing cups.
b. Referring to Figure 14 for the proper orientation,
carefully press the inboard bearing cup into the
crankcase until it is flush with the outer surface
of the crankcase.
c. Note the proper orientation and carefully press
the outboard bearing cup into the bearing carrier
assembly.
d. Press a bearing cone onto each end of the
crankshaft with the tapered end outward. The
bearing race should rest against the shoulder on
the crankshaft.
e. Lubricate the bearings with grease.
8. Install the crankshaft through the outboard end of the
crankcase.
9. With the oil pump assembly
removed
, install the
bearing carrier and new gasket. The bolt hole
positions ensure proper orientation. Tighten the
bolts evenly per Table 7 - Bolt Torque."
10. If the bearings have not been replaced, reinstall the
inboard bearing cover plate using the existing shim
set. If the bearings have been replaced, use a
thicker
set of shims.
11. Rotate the crankshaft by hand to verify free
movement of the shaft.
a. If the crankshaft has an excessive amount of
end play, too many shims have been used.
Lateral crankshaft movement (end play)
between the bearings should be:
End Play at Room Temperature
0.0015 to 0.0030" (0.038 to 0.076 mm)
If necessary, remove shims until the end play is
within tolerance.
b. If the crankshaft binds, or will not turn, not
enough shims have been used pushing the
bearing cup too tight against the bearing cone.
Remove the crankshaft from the crankcase and
drive the inboard bearing cup out toward the
inboard side of the crankcase. Reinstall the
crankshaft and the bearing cover plate using
additional shims as required.
12. Install the oil pump per the "Oil Pump Replacement"
section of this manual.
13. Reassemble the compressor according to the
"Compressor Assembly" section.
Figure 14 - Bearing Locations