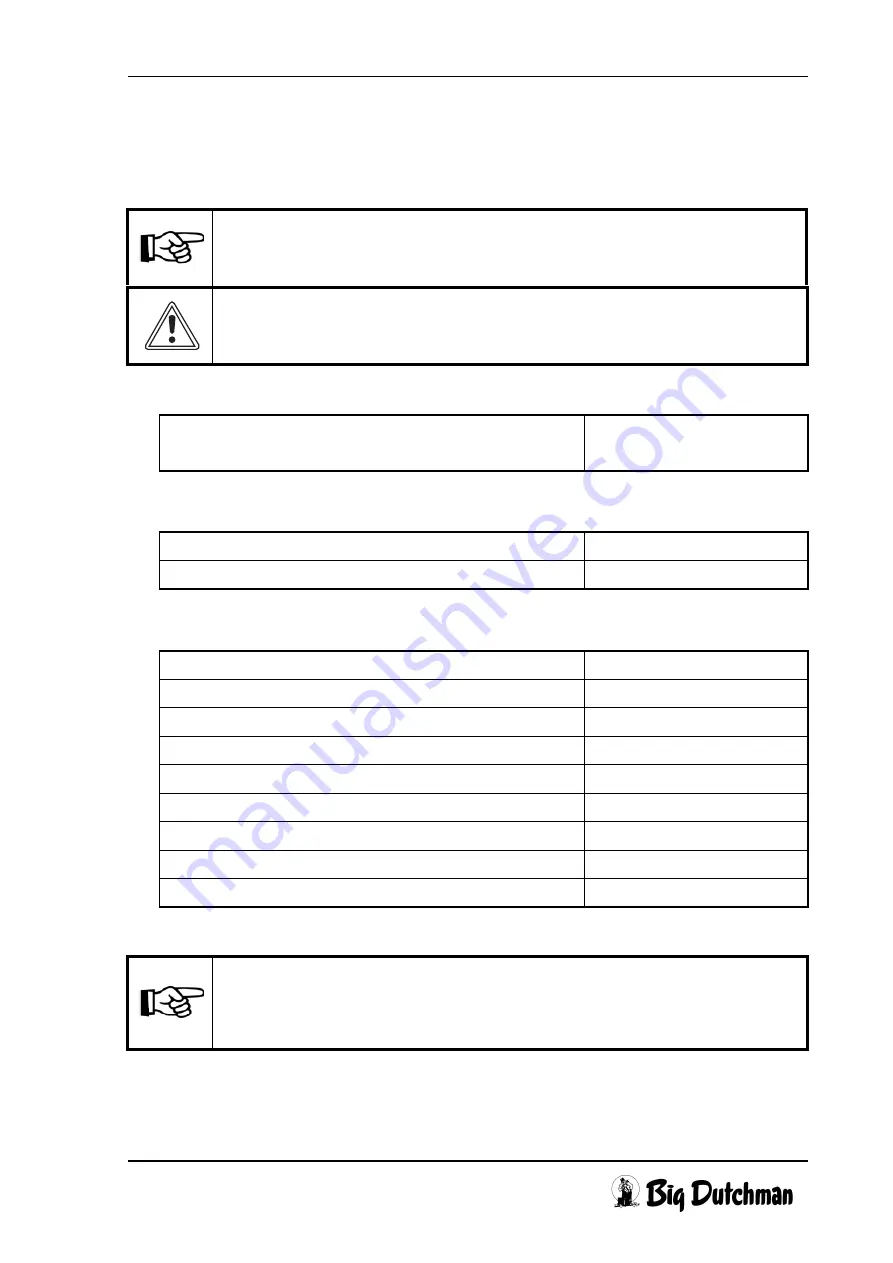
System description
Page 17
DR 1500
Edition: 08/10 M 4021 GB
3.3 Technical information
3.3.1 Technical data
Table 3-1:
System
Table 3-2:
Drive
Table 3-3:
Feed channel
The quoted performance data variies depending on the type of
transported feed, the number of turns and length of the installation.
The pipe must not be filled by more than two thirds.
max. capacity (filled to 66% and with a feed density
of 650 kg per
3
m)
1580 kg/h
Drive power
1,50 kW
Chain speed
27m/min
max. system length including 4 idler corners
300 m/with XXL: 500m
*
reduction in length per idler corner
6 m
Gradient
max. 45°
Reduction in length with 45° gradient
0,5 m per m
Chain size
35,75 x 4,5 mm
Washers
42 mm
Distance between washers
71,5 mm
Pipe outside
60 mm
Pipe inside
57 mm
Including 4 idler corners, the maximum system length must not exceed
300 m and XXL 500 m, when the driver is used
*
do not exceed ! Each
additional idler corner shortens the system by 6 m (see illustration 3-2).
* A condition for the maximum drive length of 500m is that the XXL drive is used with a smooth start.
In addition, strong, fibreglass-reinforced corner wheels must be used up to 10m before the drive.
Pellets must not be used as feed.
Summary of Contents for Dry Rapid DR 1500
Page 1: ...Mounting and operating instructions Dry Rapid DR 1500 Code No 99 97 4021 GB Edition 08 2010...
Page 2: ......
Page 4: ......
Page 83: ...Drive unit Page 73 DR 1500 Edition 08 10 M 4021 GB Figure 9 13 Drive with clamping device...
Page 162: ...Page 152 Control and operation DR 1500 Edition 08 10 M 4021 GB Description of sensor MS45R...