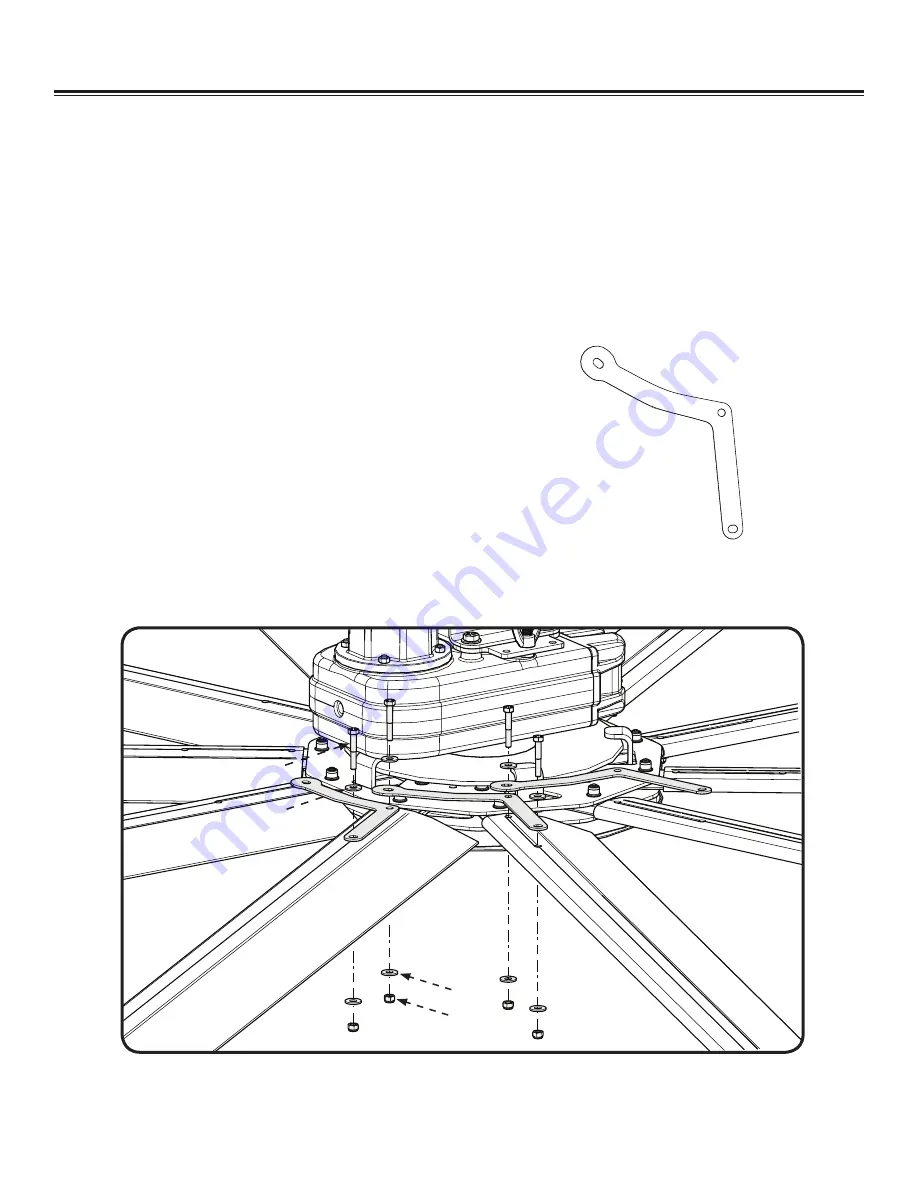
8’–24’ POWERFOIL
®
X2.0 WASHDOWN & POWERFOIL
®
X2.0PLUS WASHDOWN
25
WWW.BIGASSFANS.COM ©2012 DELTA T CORP. ALL RIGHTS RESERVED
8’–24’ POWERFOIL
®
X2.0 WASHDOWN & POWERFOIL
®
X2.0PLUS WASHDOWN
3. Attach airfoils to hub
Attach the 10 airfoil retainers with the Airfoil Hardware. Moving clockwise around the fan hub, position the airfoil retainers end over end
as shown. Hole A of the retainer should be positioned over top of Hole B.
Do not tighten the bolts until all the airfoil retainers have been
attached!
Tighten the bolts along the outer perimeter to
29 ft·lb (39 N·m)
using a torque wrench and 1/2” socket. After the outer perimeter bolts
are torqued, tighten the bolts along the inner perimeter to
29 ft·lb (39 N·m)
.
Airfoil Hardware (BAF-Supplied):
a. (20) 5/16-18 x 2’’ GR 8 Bolt
b. (40) 5/16” Flat Washer
c. (20) 5/16-18 Nylock Nut
a
b
c
b
Installing Airfoils (cont.)
Hole A
Hole B
Airfoil Retainer
Summary of Contents for powerfoil x2.0
Page 6: ......
Page 48: ......
Page 56: ...Notes...
Page 58: ......
Page 66: ......
Page 73: ......
Page 74: ......
Page 75: ......
Page 76: ...002972 002972 2425 Merchant St Lexington KY 40511 1 877 BIG FANS WWW BIGASSFANS COM REV J...