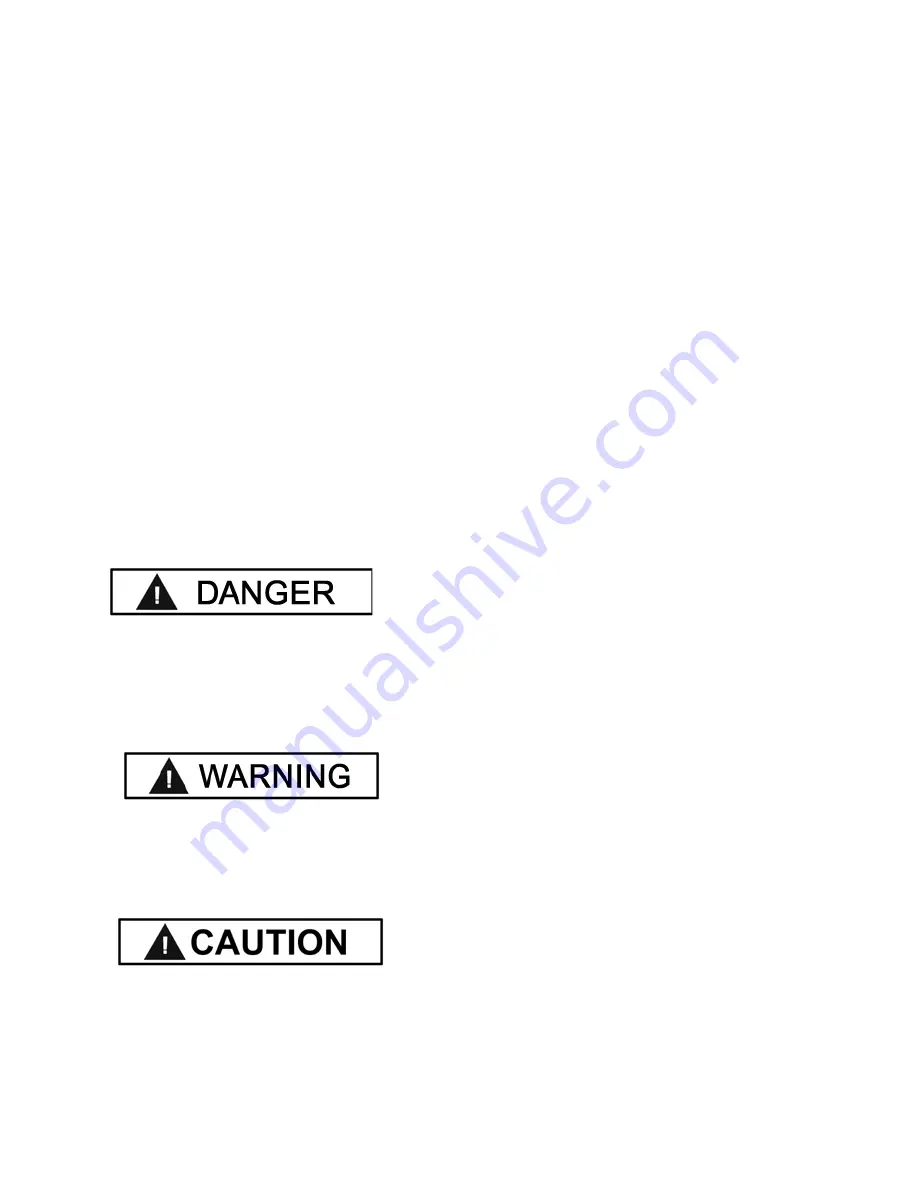
3
IMPORTANT NOTICE
Do not attempt to install this lift if you have never been
trained on basic automotive lift installation procedures.
Never attempt to lift components without proper lifting
tools such as forklift or cranes. Stay clear of any moving
parts that can fall and cause injury. These instructions
must be followed to insure proper installation and opera-
tion of your lift. Failure to comply with these instructions
can result in serious bodily harm and void product war-
ranty. Manufacturer will assume no liability for loss or
damage of any kind, expressed or implied resulting from
improper installation or use of this product.
PLEASE READ ENTIRE MANUAL
PRIOR TO INSTALLATION.
DEFINITIONS OF
HAZARD LEVELS
Identify the hazard levels used in this manual with the
following definitions and signal words:
DANGER !
Watch for this symbol: It Means: Immediate hazards
which will result in severe personal injury or death.
WARNING !
Watch for this symbol: It Means: Hazards or unsafe
practices which could result in severe personal
injury or death.
CAUTION !
Watch for this symbol: It Means: Hazards or unsafe
practices which may result in minor personal injury,
product or property damage.
OWNER’S RESPONSIBILITY
To maintain the lift and user safety, the responsibility of the
owner is to read and follow these instructions:
Follow all installation and operation instructions.
Make sure installation conforms to all applicable Local,
State, and Federal Codes, Rules, and Regulations;
such as State and Federal OSHA Regulations and
Electrical Codes.
Carefully check the lift for correct initial function.
Read and follow the safety instructions. Keep them
readily available for machine operators.
Make certain all operators are properly trained, know
how to safely and correctly operate the unit, and are
properly supervised.
Allow unit operation only with all parts in place and
operating safely.
Carefully inspect the unit on a regular basis and
perform all maintenance as required.
Service and maintain the unit only with authorized or
approved replacement parts.
Keep all instructions permanently with the unit and all
decals on the unit clean and visible.
BEFORE YOU BEGIN
Receiving:
The shipment should be thoroughly inspected as soon as it
is received. The signed bill of lading is acknowledgement by
the carrier of receipt in good condition of shipment covered
by your invoice. If any of the goods called for on this bill of
lading are shorted or damaged, do not accept them until the
carrier makes a notation on the freight bill of the shorted or
damaged goods. Do this for your own protection.
NOTIFY THE CARRIER AT ONCE
if any hidden loss or
damage is discovered after receipt and request the carrier
to make an inspection. If the carrier will not do so, prepare
a signed statement to the effect that you have notified the
carrier (on a specific date) and that the carrier has failed to
comply with your request.
IT IS DIFFICULT TO COLLECT FOR LOSS OR DAMAGE
AFTER YOU HAVE GIVEN THE CARRIER A CLEAR
RECEIPT.
File your claim with the carrier promptly. Support
your claim with copies of the bill of lading, freight bill,
invoice, and photographs, if available. Our willingness to
assist in helping you process your claim does not make
BendPak responsible for collection of claims or replace-
ment of lost or damaged materials.