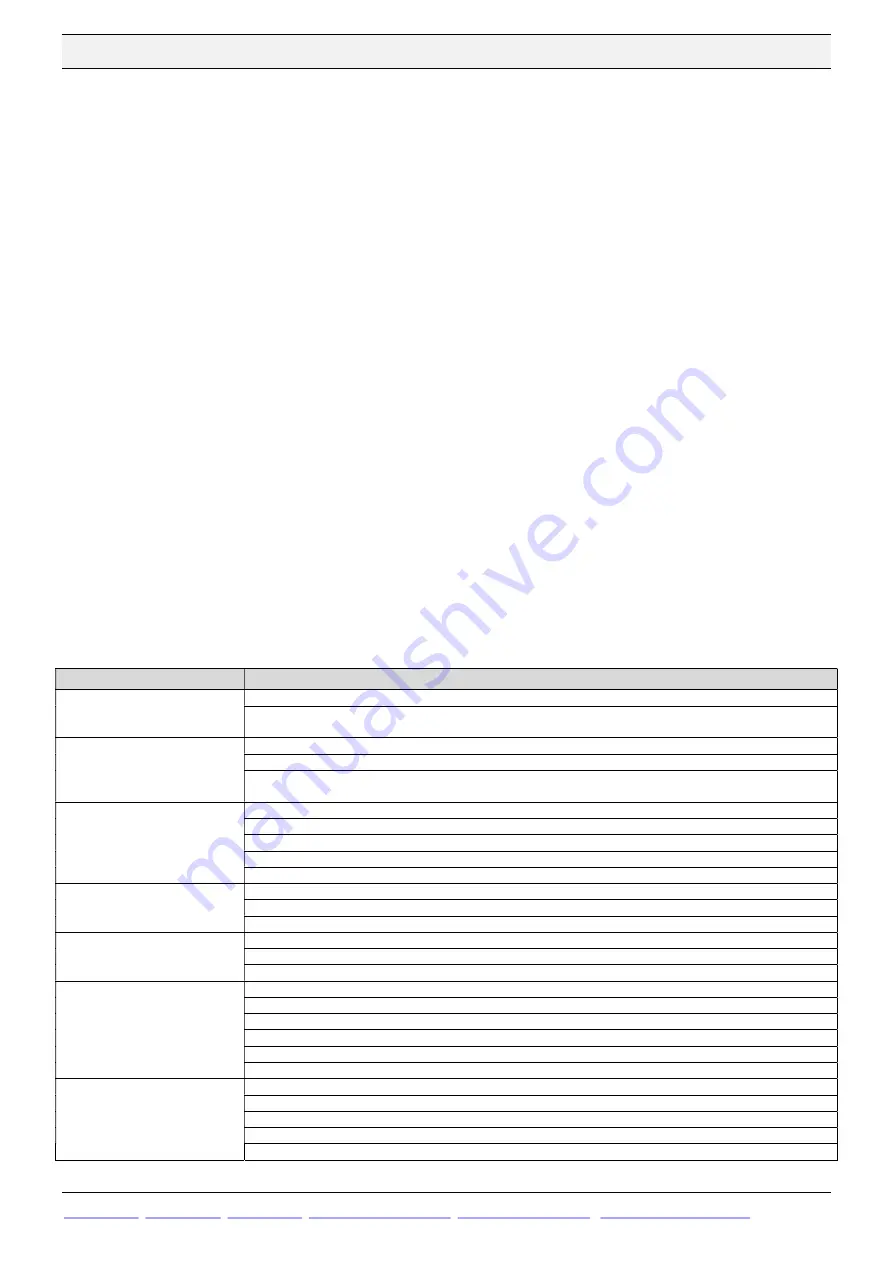
Beijer Electronics Frequency Inverter BFI-P2
KI00306B 2020-03
www.beijer.se www.beijer.no www.beijer.dk
www.beijerelectronics.com www.beijerelectronics.de www.beijerelektronik.com.tr
20 (31)
6 Autotuning for Vector control
To take advantage of other modes than V/F control the inverter must make a measurement (offline
autotuning) of the motor. Autotuning means that the motor's electrical characteristics are measured
and stored in the drive. These are then used for controlling the motor in an optimal way, gives
additional torque at low speed and also makes motor speed constant even though load of the motor
fluctuates. Autotuning is done in the following way:
1.
Make sure Safety Relay is correct connected or Safe Torque Off inputs are connected correctly,
terminal 1 to 12 and 9 to 13.
2.
Make sure motor is connected to the Drive on terminals U, V and W
3.
Set the following parameters in the sequence they are listed:
P1-07: Motor Rated Voltage (V), default 230 or 400.
P1-08: Motor Rated Current (A), default drive rating.
P1-09: Motor Rated Frequency (Hz), default 50.
P1-14: Parameter access code, default 0 set to 201
P4-05: Motor Power Factor, default -, (often referred to as Cos φ)
P4-01: 0 for Vector Speed Control or 1 for Vector Torque Control
4.
Start Autotuning by set P4-02=1. Drive will perform autotune, a non-rotational function
although some small rotation of the motor shaft may occur
5.
Wait for completion of autotune. During autotune the drive will display Auto-t or Auto-Tune on and
returning to its normal state once autotune is complete
6.
Autotuning will write values to parameters P7-01, P7-02, P7-03, P7-04, P7-06
7.
Autotuning can also fail. Check error code on display and look for explanation in chapter 8.
Symptom
Solution / Advice
Poor Torque Performance at
low speed
Check Auto-Tune performed Successfully – See Set-Up procedure
Check System criteria effecting auto-tune have not change. See step 3 in standard set-up procedure.
If any of these setting have changed then the Auto-tune procedure must be repeated.
Too much current causing
motor to heat up
Check parameter P1-07, motor nominal voltage is set correctly
Check parameter P1-08, motor nominal current is set correctly
If running for sustained periods at low speed check adequate cooling is provided to the motor. Forced
ventilation of motor might be needed.
Motor Stalled
Check motor connection
Check values entered into motor parameters P1-07 to P1-10 & P4-05
Check Auto-Tune performed Successfully – See Set-Up procedure
Reduce the load or/and Increase acceleration / deceleration time
Increase drive and motor rating
Unstable motor speed / poor
speed regulation
Check values entered into motor parameters P1-07 to P1-10 & P4-05
Check Auto-Tune performed Successfully – See Set-Up procedure
Check appropriate tuning of speed loop controller, reduce Gain, P4-03
Poor motor dynamics, slow
response times
Check values entered into motor parameters, P1-07 to P1-10 & P4-05
Check Auto-Tune performed Successfully – See Set-Up procedure
Check appropriate tuning of speed loop controller, increase gains as required
Trip Occurring
Check the motor and motor connection cable for phase-phase and phase-earth short circuits
Check the load mechanically for a jam or stalled condition, or shock loads
Check values entered into motor parameters P1-07 to P1-10 & P4-05
Check Auto-Tune performed Successfully – See Set-Up procedure
Increase the ramp up time in P1-03
Check appropriate tuning of speed loop controller, reduce gains as required
I_t-trp
Trip Occurring
Increase acceleration rate or reduce the load
Check motor cable length is within specified limits
Check values entered into motor parameters (P1-07 to P1-10 & P4-05)
Check Auto-Tune performed Successfully – See Set-Up procedure
Check the load mechanically to ensure it is free, and no jams, blockages or other mechanical faults exist