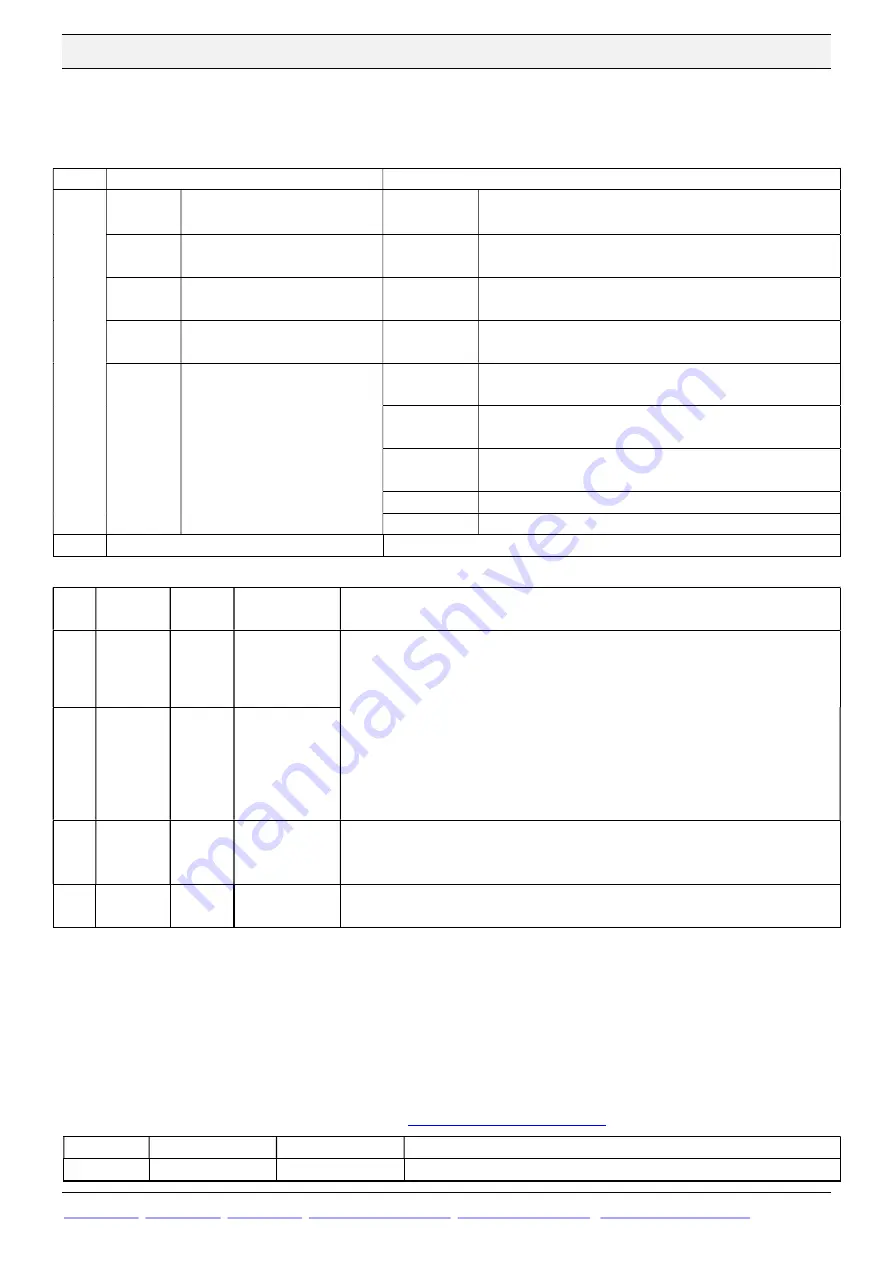
Beijer Electronics Frequency Inverter BFI-P2
KI00306B 2020-03
www.beijer.se www.beijer.no www.beijer.dk
www.beijerelectronics.com www.beijerelectronics.de www.beijerelektronik.com.tr
16 (31)
5.8 Fieldbus communication protocol
Cyclic data for all bus types consist of four 16-bit word input and output. Word 1 and 2 has the
following meaning:
Word
Data to drive
Data from drive
1
Bit 0
0: Stop
1: Start
Bit 0
0: Stop
1: Startsignal on
Bit 1
0: Deceleration time in P1-04
1: Deceleration time in P2-25
Bit 1
0: Drive Healthy
1: Drive tripped
Bit 2
0: No function
1: Alarm reset
Bit 2
No Function in BFI-P2
Bit 3
0: No function
1: Coasting stop
Bit 3
0: Safe Torque inputs activated
1: Safe Torque inputs deactivated, Inhibit in display
Bit 4-15
Not used
Bit 4
0: Maintenance Time Not Elapsed
1: Maintenance Time Elapsed
Bit 5
0: Not in Standby
1: In Standby
Bit 6
0: BFI not Ready to run
1: BFI Ready to run, ( Enabled, STO ok, Power on)
Bit 7
Not used
Bit 8-15
Alarmcode
2
Set frequency [0,1 Hz]
Actual output frequency [0,1 Hz]
Word 3 and 4 of output/input data can be individually configurated described in table below.
Para-
meter
Name
Default
settng
Function
Explanation
P5-12
Fieldbus
Module
PDO3
0
What to be read
in word 3
0 : Motor Current in A with one decimal place, 105 = 10,5 A (P5-12)
0 : Output Torque, Value 0 to 2000 = 0 to 200 % of rated torque (P5-08)
1 : Output Power in kW with two decimal places, 405 = 4.05kW
2 : Digital Input Status. Bit 0 =Digital input 1 status, Bit 1= Digital input 2 status etc
3 : Analog Input 2. Signal Level 0 to 1000 = 0 to 100.0%
4 : Drive Heat-sink Temperature in °C
5 : User Register 1. Accessable by PLC program or group 9 parameters
6 : User Register 2. Accessable by PLC program or group 9 parameters
7 : P0-80 Value P6-28
P5-08
Fieldbus
Module
PDO4
0
What to be read
in word 4
P5-14
Fieldbus
Module PDI3
0
What to be written
in word 3
0 : Torque limit / ref (%) Set in % of rated torque with 1 decimals.
1 : User PID Reference - 0 to 1000 = 0% to 100.0%
2 : User Register 3 – Can be accessed by PLC program or group 9 parameters
P5-13
Fieldbus
Module PDI4
0
What to be written
in word 4
0: User ramp time – In second with two decimal places.
1: User Register 4 – Can be accessed by PLC program or group 9 parameters
Acyclic data is also available except for CC-link.
5.9 Energy Optimization function
The Energy Optimization function is designed to maximize the energy savings achievable when the
motor and drive is not operating at rated load. Care should be taken in using the energy optimiser
function in applications where the frequency setpoint to the drive changes continuously, such as PI
control applications. As the motor voltage is reduced, the slip of the motor may increase, resulting
in a small drop in motor speed, which can make the PI control unstable. Detailed explanation of the
function is to be found in Application Notes on
www.beijerelectronics.com
Parameter
Name
Default setting
Function
P1-06
Energy Optimization
0
0= Disbaled 1 = Enabled