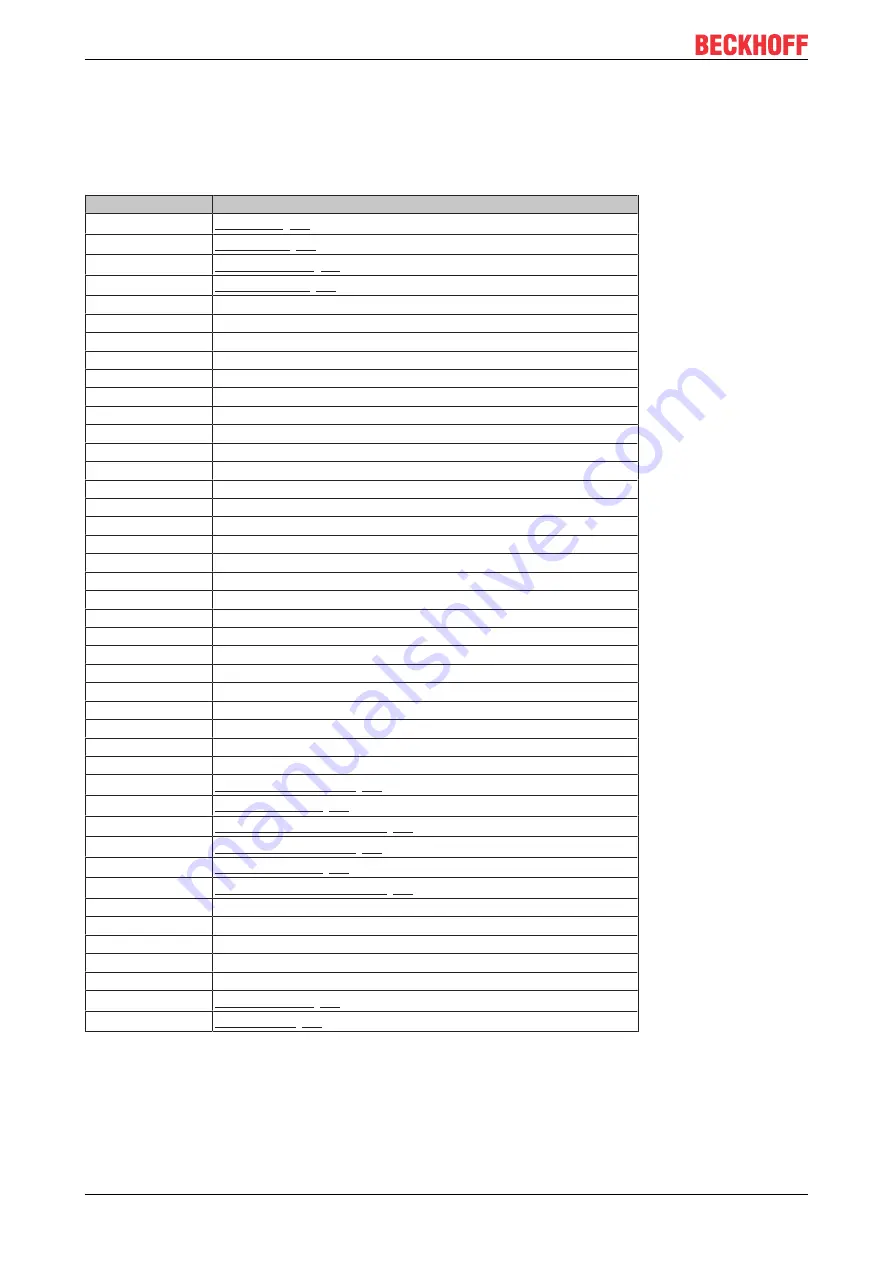
CoE objects
EP7402-0057
46
Version: 1.3
7
CoE objects
7.1
Register
Index (hex)
Name
1000
1008
1009
100A
100B
Bootloader version
1011
Restore default parameters
1018
Identity
10F0
Backup parameter handling
1600
DO RxPDO-Map Outputs
1601
STM RxPDO-Map Control Ch. 1
1602
STM RxPDO-Map Target Velocity Ch. 1
1603
STM RxPDO-Map Control Ch. 2
1604
STM RxPDO-Map Target Velocity Ch. 2
1A00
DI TxPDO-Map Inputs
1A01
STM TxPDO-Map Status Ch. 1
1A02
STM TxPDO-Map Synchron info data Ch. 1
1A03
STM TxPDO-Map Status Ch. 1
1A04
STM TxPDO-Map Synchron info data Ch. 1
1A05
STM TxPDO-Map Inputs Device
1C00
Sync manager type
1C12
RxPDO assign
1C13
TxPDO assign
1C32
SM output parameter
1C33
SM input parameter
6000
DI Inputs
6020
STM Inputs Ch. 1
6030
STM Inputs Ch. 2
7010
DO Outputs
7020
STM Outputs Ch. 1
7030
STM Outputs Ch. 2
8020
8022
8023
STM Controller Settings 4 Ch. 1 [
8030
8032
8033
STM Controller Settings 4 Ch. 2 [
F000
Modular Device Profile
F008
Code word
F010
Module Profile List
F081
Download revision
F600
STM Device Diag data
F80F
F900