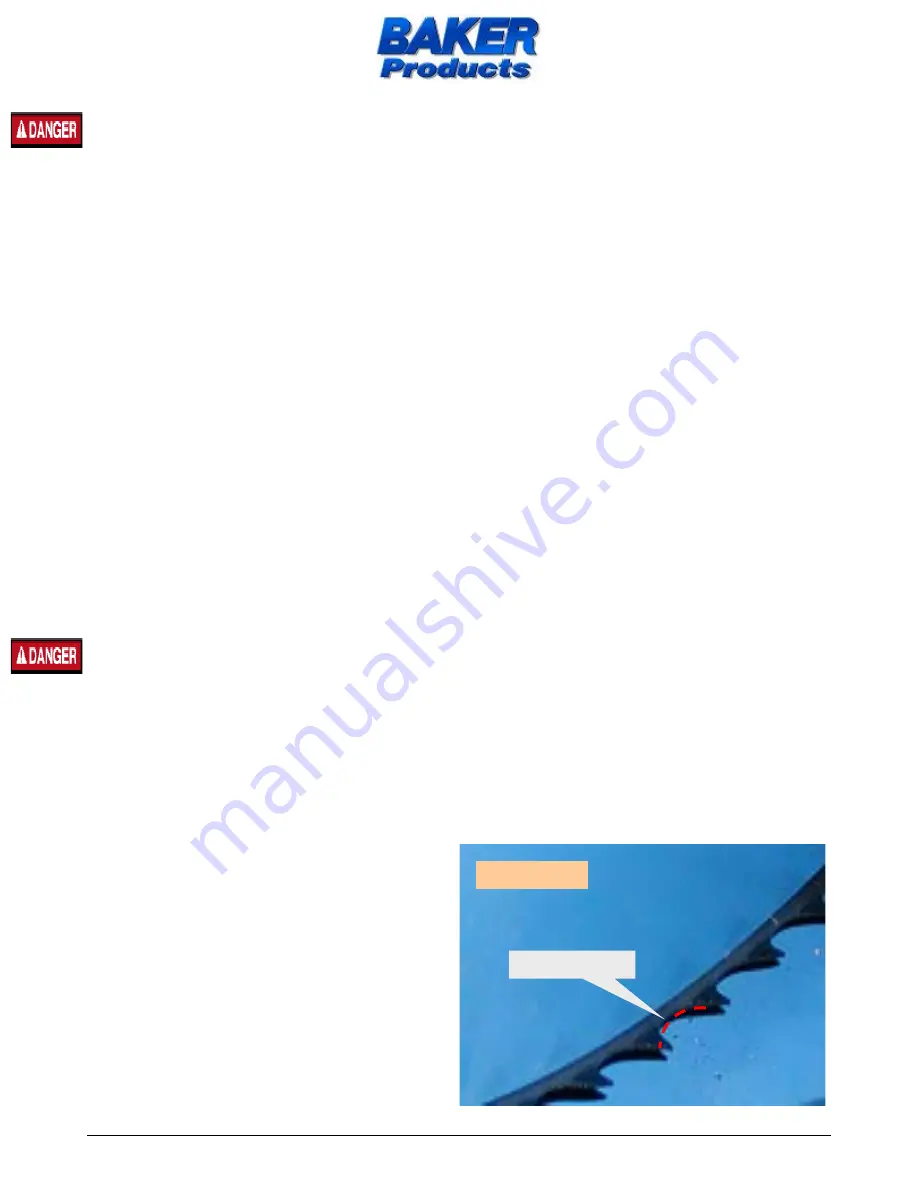
46
Blade Tracking
Note:
The blade tracking is set at the factory prior to shipment, but it may periodically have to be
reset. Most band blades will vary on how they track due to the blade material.
1 ½” Blades
running on 1” thick steel wheels will be centered on the wheels between
the gullet and the rear edge of the wheel. Depending on the blade brand used, the
distance from the face of the wheel to the gullet will not always be 1/32”.
Example: Lenox blades may be 1/8” from the gullet to the face of the wheel.
2” Blades
--
should be centered on the wheels with the gullet flush or no more than 1/32” past
the front face of the wheels.
If the blade is tracking out just a little after running for a few minutes, don’t be alarmed;
most blades do this as they self-adjust to the contour of the wheels.
If the blade is running out or in more than 1/32” you should try three or more blades or
another box of blades before making any tracking adjustments. This will help you
determine whether it’s the blade(s) or something else that is affecting tracking.
Verify proper blade tension, which can also cause tracking to vary. More tension tends to
bring the blade “out” on the wheels.
2” Blade Tension
: 1,900 – 2,100
1 ½” Blade Tension
: 1,700 PSI
If the problem exists after trying different blades, then proceed to the next section
“
Tracking the Blade”.
Tracking the Blade
Move saw head to front of the mill (end nearest the operator control station).
Power down the mill and lock-out/tag-out main electrical panel.
Ensure the blade is properly installed; reference “
Changing Blades”
section if necessary.
Open the left and right cowling doors.
Rotate the idler wheel several rotations counter-clockwise and look at the blade gullet in
relation to the front face of the wheel
.
Figure 42
Blade Gullet