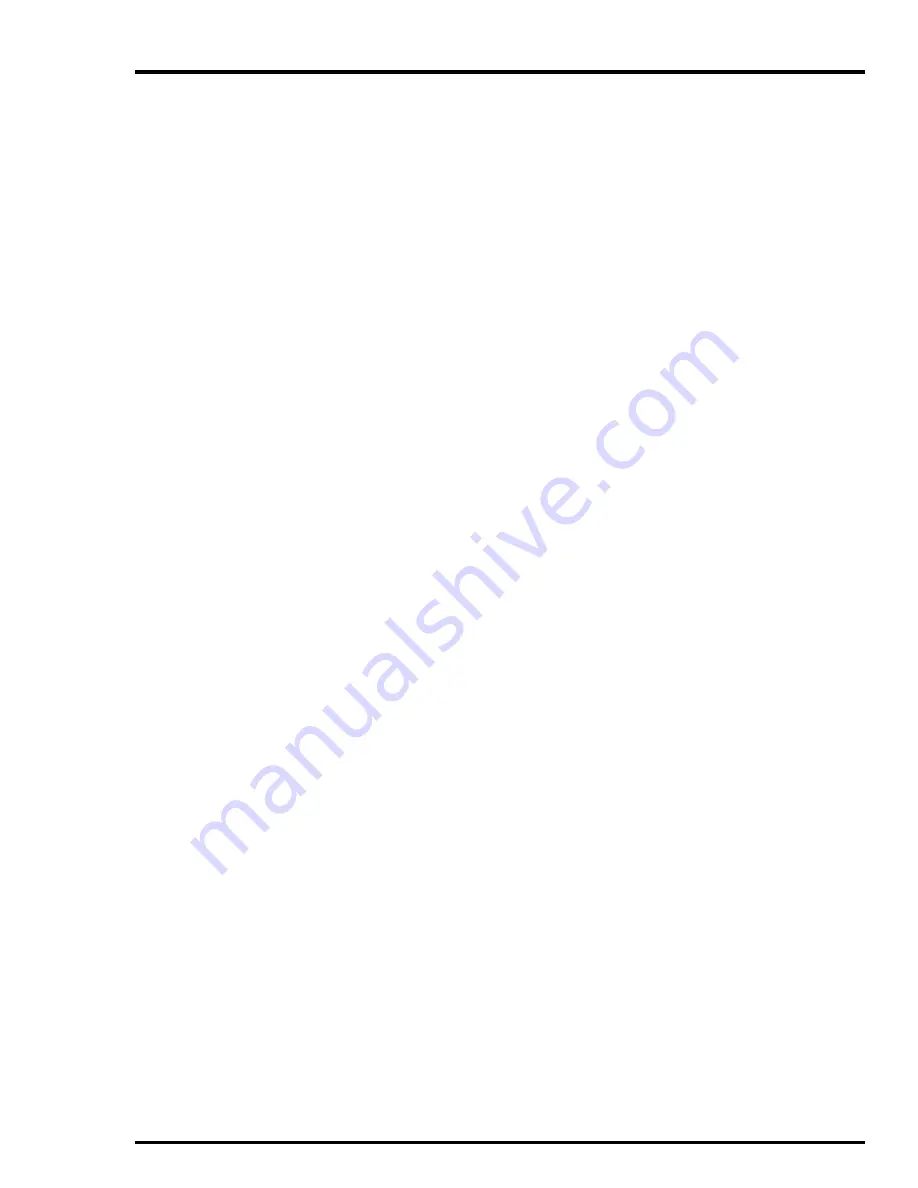
CONFIGURATION AND CALIBRATION
FIELD CALIBRATION
I-E96-301B1
15 December 1994
4 - 5
3. Calibrate the point with the new value (2 to 11 calibration
points per channel and input type).
4. Enable the point to the system.
Before beginning calibration, each channel must be configured
with one function code 216, and the calibration type defined in
S4 of function code 217 must be consistent with the input sig-
nal defined in S4 of function code 216.
The input channel being field calibrated must be disabled
before any calibration commands are accepted. Disabling the
input channel removes the channel from the normal input
scan processing. The point shows bad quality while it is dis-
abled. The value of the input is undefined while the channel is
disabled. All other channels are not affected and continue pro-
cessing input data according to the configuration data.
Before performing a point field calibration, ultra stable, known,
precise values are connected to the input channel. During
point calibration, the slave reads the input and stores its digi-
tized value. A user must perform at least two point calibrations
and can perform up to 11 point calibrations within an input
range. All these adjustment factors are calculated and stored
in the slave’s NVRAM when the point is enabled.
Up to 11 calibration points may be identified to adjust for non-
linear components in the input circuitry. Precision voltage val-
ues are required for low level, thermocouple and high level
input field calibration. For RTD input calibration, precision
resistance values are used. Function code 217 and the same
procedure is used for all three field calibrations.
Each input channel must be enabled before normal input scan
processing is resumed. The enable command indicates to the
slave that the calibration process is completed. At that time the
slave stores the field calibration values in NVRAM. The slave
uses these values during input scan processing to calculate
the correction factors for the calibrated channel.
If no field calibration is performed, or if the escape command
was issued to cancel the calibration, the new calibration cor-
rection values are not computed and the previous correction
factors will continue to be used. There is no change to the cali-
bration of the point. The quality of the input point remains bad
after an enable command until a successful input scan is per-
formed for that point. If either the master or the slave is
stopped, or placed into CONFIGURE mode while a field calibra-
tion sequence is in progress (before an enable is issued), the
field calibration sequence is aborted and must be restarted.
Once the slave module is calibrated, no further manual cali-
bration is necessary. On-board, low-drift references maintain
the accuracy of the calibration.