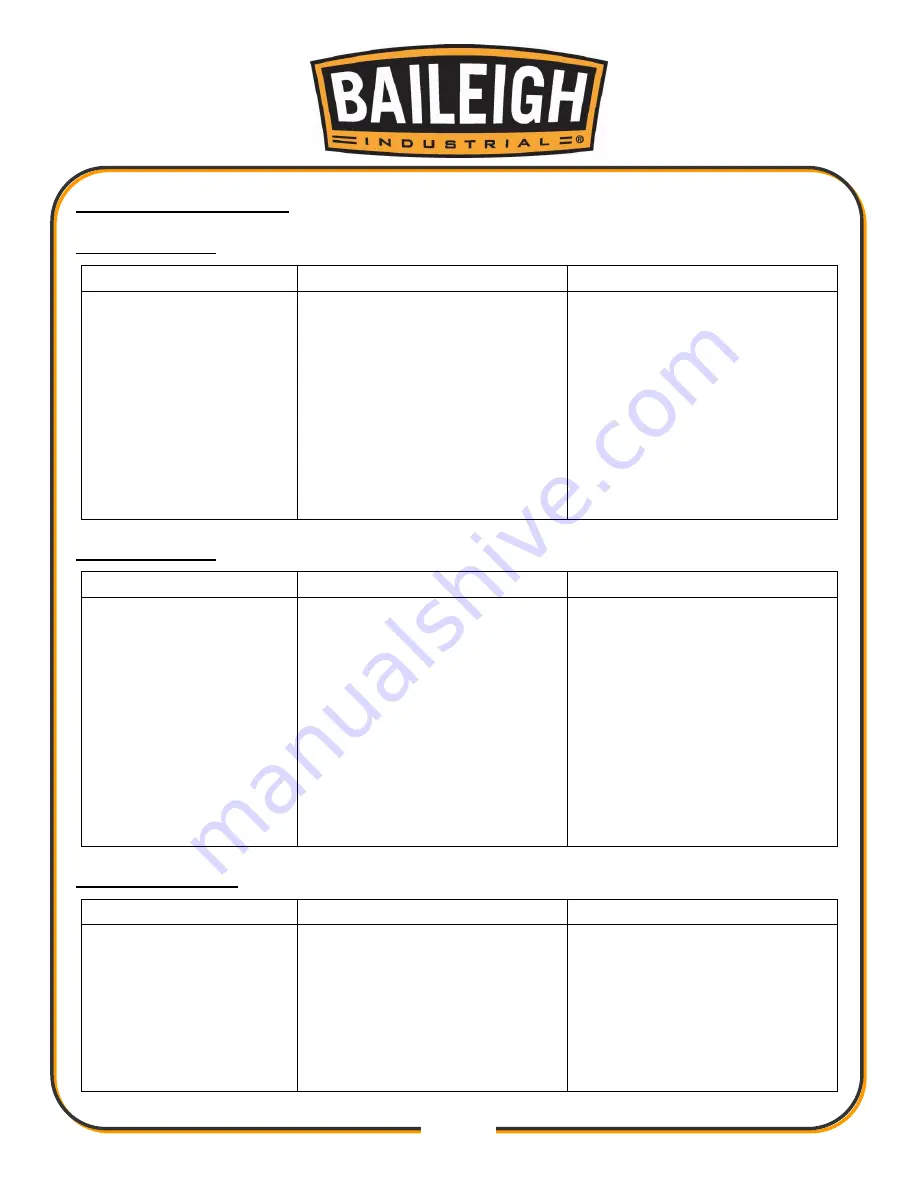
45
45
TROUBLESHOOTING
Shear Operation
FAULT
PROBABLE CAUSE
REMEDY
Can’t shear material
Cuts are not square.
Poor
quality
of
cuts,
ripping./ or tearing
Improper blade gap distance,
exceeding
machine capacities
Blade gap unequal across length,
Too
much
bow
in
blade,
Inadequate hold down pressure.
Dull blades, Poor blade gap set-
up, Loose blade
Widen gap for thicker material
Adjust blade gap to be equal
across length, Adjust blade bow,
Adjust hold down gap.
Replace or sharpen blades,
Adjust blade gap, Remove blade,
clean mounting.
Brake Operation
FAULT
PROBABLE CAUSE
REMEDY
Heavy resistance during
bends
Bend
radius
is
not
consistent
Brake blade points are
chipping.
Piece part shows scoring
marks after bend.
Exceeding machine capacities.
Brake blades and die are not
aligned.
Brake blades and die are not
aligned.
Brake
blades
or
die
has
scratches.
Use materials within machine
capabilities
Adjust brake alignment.
Adjust brake alignment.
Polish out scratches,
Slip Roll Operation
FAULT
PROBABLE CAUSE
REMEDY
Slip Roll creates cones
instead of cylinders.
A noticeable crease forms
in the piece part.
Piece part is pitted.
Rolls are not parallel to each
other.
Excessive pressure applied to
one spot.
Material sheet is dirty or roll is
damaged.
Adjust the rear roll to be parallel
to the top roll.
Reduce the radius and make the
bend in several passes.
Clean material, polish nicks in
roller.
Summary of Contents for SBR-5220
Page 17: ...14 14 Combination Shear Brake Roll Rear Stop Rods Handlebars Rear Stop Covers...
Page 21: ...18 18 OVERALL DIMENSIONS 71 50 74 00 54 50 18 75 19 75 56 25 44 Mounting Holes...
Page 45: ...42 42 PARTS IDENTIFICATION DRAWING C 17 18 55 55 23 23 23 23 49 49 56 21 20 19 56 57 22 57...
Page 49: ...46 46 NOTES...
Page 50: ...47 47 NOTES...
Page 51: ...48 48 NOTES...