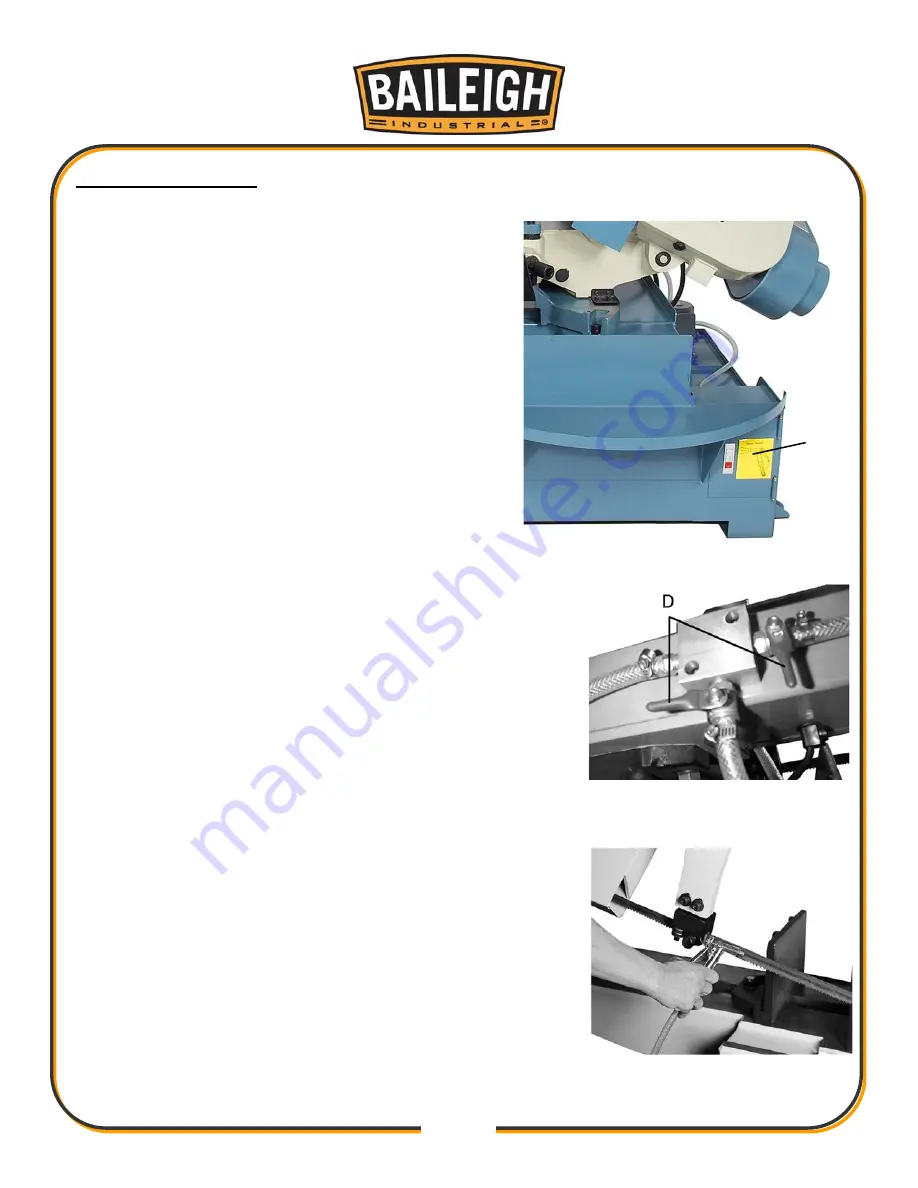
17
17
Water Gun Operation
Water gun is designed for washing off the chips and
debris in or on the work table, as well as, being used
during machine operation.
1. Open the access door and remove the spray hose.
2. Press the operation start button to start machine.
3. Turn off the hydraulic flow control switch by turning
the cutting pressure control valve clockwise to the
end.
4. Start the coolant pump by turning the switch to "I"
(on) position.
5. Close the two coolant ball valves (D) on the saw arm. This
will direct the coolant flow and pressure to the spray hose.
6. Use the hose as needed to spray chips off of the blade,
guides, vise and table back to the coolant strainer for
removal.
7. Immediately clean up any splatter, or overspray from the
floor.
A
Summary of Contents for BS-330M
Page 17: ...14 14 DESCRIPTION OF MACHINE PARTS A G E D C F B H I J K L N P Q O M S T U V W X R Y...
Page 32: ...29 29...
Page 48: ...45 45 ELECTRICAL PANEL LAYOUT...
Page 49: ...46 46 ELECTRICAL SCHEMATIC...
Page 50: ...47 47 PARTS DIAGRAM...
Page 51: ...48 48...
Page 65: ...62 62 NOTES...
Page 66: ...63 63 NOTES...
Page 67: ...64 64 NOTES...