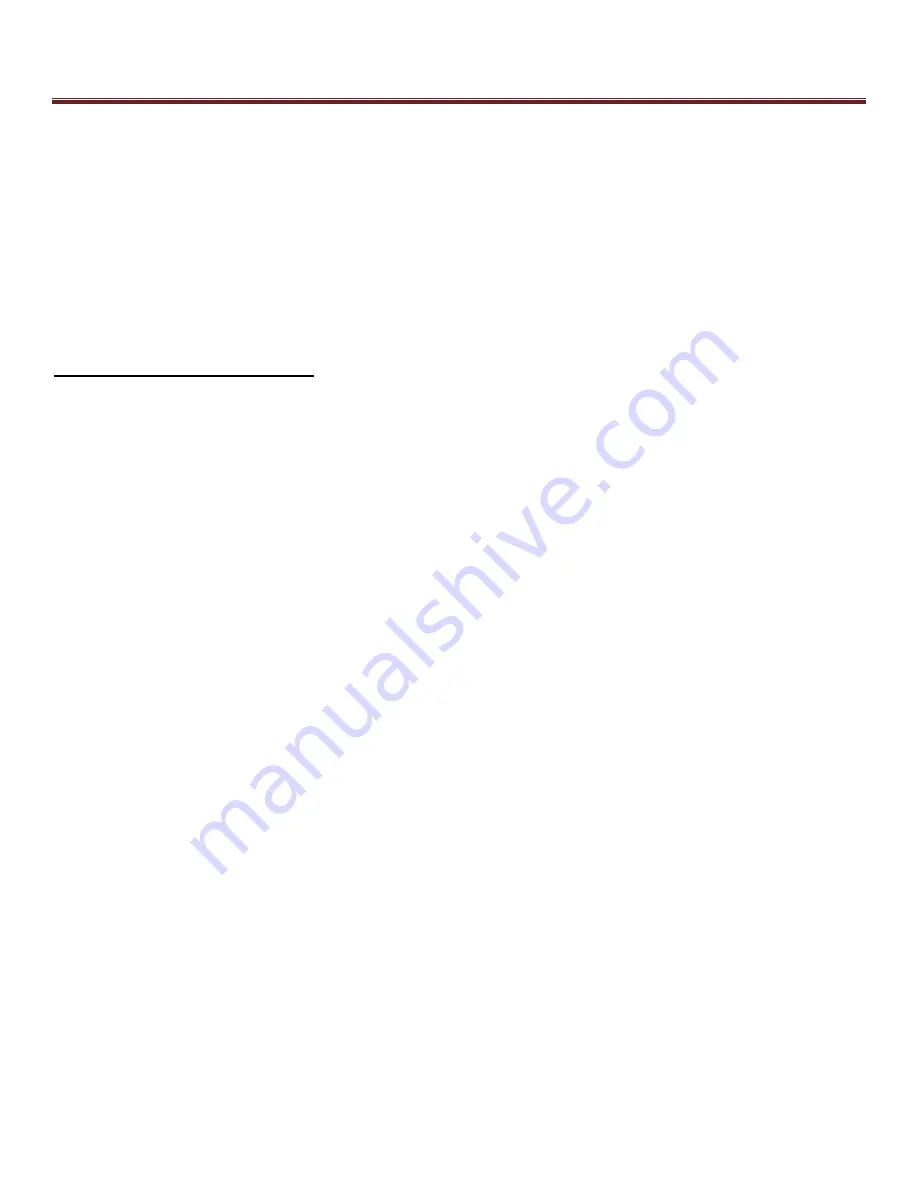
Owner’s Manual Play Set
Rev5/20/10 BRS
15. Instruct children to never jump from a fort deck. They should always use the ladder, ramp or
slide.
16. Instruct children to never crawl or walk across the top of monkey bars.
17. Instruct children to never crawl on top of a fort roof.
18. Verify that any suspended climbing ropes, chain, or cable are secured at both ends and that
they cannot be looped back on it.
19. Instruct children not to attach items to the playground equipment that are not specifically
designed for use with the equipment, such as, but not limited to, jump ropes, clothesline, pet
leashes, cables and chain as they may cause a strangulation hazard.
20. Instruct children to never wrap their legs around swing chain.
21. Instruct children to never slide down the swing chain.
Maintenance Instructions:
1. Check all nuts and bolts twice monthly during the usage season and tighten as required. (But
not so tight that you crack the wood) We recommend you check the swing beam and
hardware every two weeks due to wood expansion and contraction. It is particularly important
that this procedure be followed at the beginning of each season.
2. Remove plastic swing seats and take indoors or do not use when the temperature drops below
32
F.
3. Oil all metallic moving parts monthly during the usage period.
4. Check all coverings for bolts and sharp edges twice monthly during usage season to be certain
they are in place. Replace when necessary. It is especially important to do this at the
beginning of each new season.
5. Check swing seats, ropes, cables and chains monthly during usage season for evidence of
deterioration. Replacement should be made of any swing seat that has developed cracks in
the plastic seats or has exposed metal in the edges of the swing seat. If there are already
exposed metal inserts on the edge of the seat, immediately remove the seats and chains to
prevent serious injury. Ropes, cables and chains should be removed and replaced if excessive
wear is found.
6. For rusted areas on metallic members such as monkey bars, hand supports, brackets, etc.
Sand and repaint, using a non lead-based paint meeting the requirements of Title 16 CRF Part
1303.
7. Inspect wood parts monthly. The grain of the wood sometimes will lift in the dry season
causing splinters to appear. Light sanding may be necessary to maintain a safe playing
environment. If you are treating your Playcenter with stain regularly, it will help prevent severe
checking/splitting and other weather damage.
8. We have applied a waterborne transparent stain to your unit. This is done for color only. Once
or twice a year, depending on your climate conditions, you must apply some type of protection
(sealant) to the wood of your unit. Prior to the application of sealant, lightly sand any “rough”
spots on your set. Please note this is a requirement of your warranty.
9. Creating and maintaining the Playcenter on a level location is very important. As your children
play, your Playcenter will slowly dig its way into the soil, and it is very important that it settles
evenly. Make sure the play set is level and true once each year or at the beginning of each
play season.
10. Rake the surface periodically to prevent compaction and maintain appropriate depths.