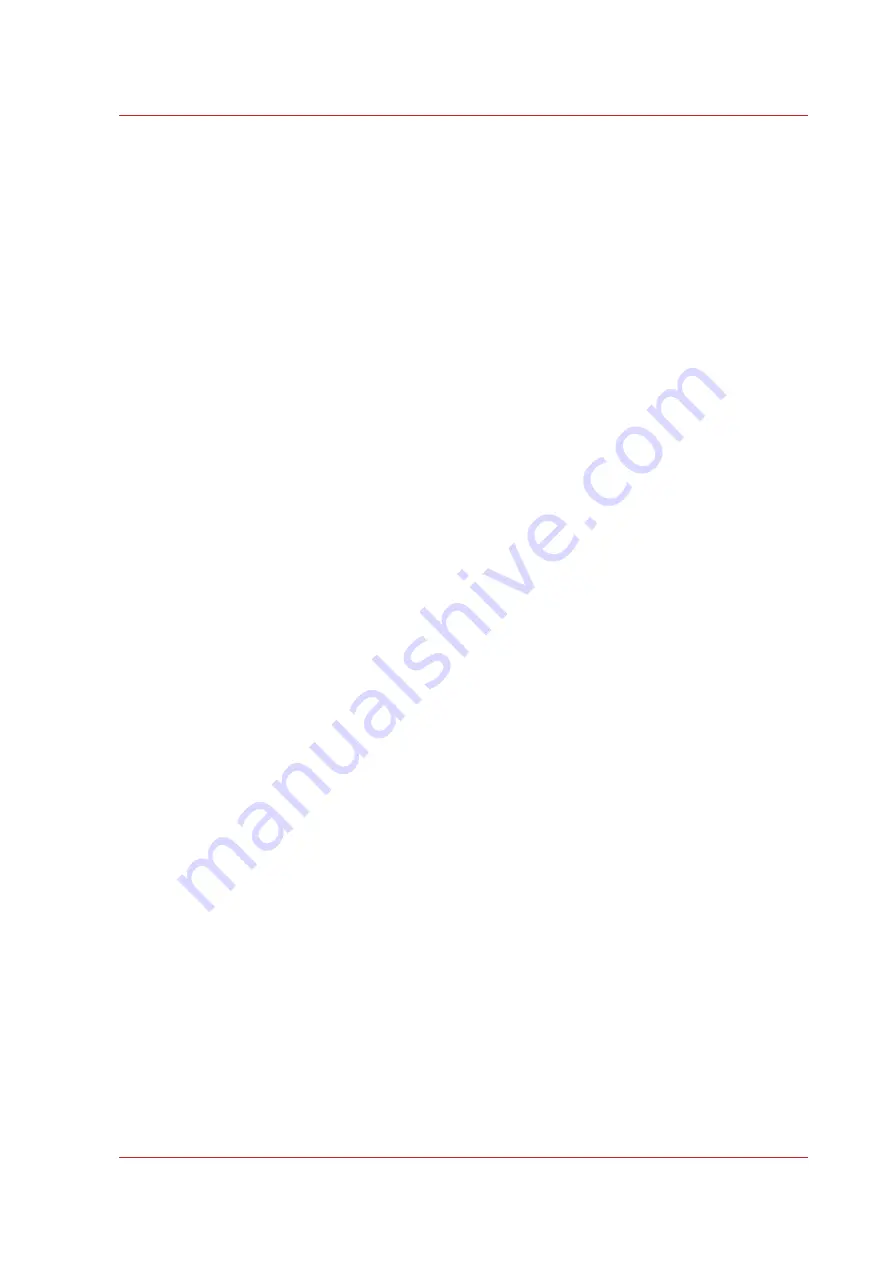
97
AXOR Industries
Service Manual
NanoMack
®
ver.1 rev.11/'19
5.4 Motor / Feedback
BRUSHLESS MOTOR:
Bru Encoder Commutation
With this coupling set only the following parameter:
•
Resolution:
insert the value of encoder pulses/rev.
•
Phase Angle:
It visualizes the phasing angle of the motor, previously calculated with the “
Au-
toPhasing
” procedures.
All other parameters are not to be set.
Bru Encoder Incremental serial (in Feedback Type select Encoder Incremental)
With this coupling set only the following parameter:
•
Resolution:
insert the value of encoder pulses/rev.
•
Phase Angle:
It visualizes the phasing angle of the motor, previously calculated with the “
Au-
toPhasing
” procedures.
All other parameters are not to be set.
Bru Encoder Incremental
With this coupling set only the following parameter:
•
Resolution:
insert the value of encoder pulses/rev.
All other parameters are not to be set.
Note:
At the first powerup happen the electrical phasing between motor and encoder, this can
result in a slight movement of the motor
.
Bru Sensorless
With this coupling set only the following parameter:
•
Resolution:
insert the value of encoder pulses/rev.
•
Min. RPM:
minimum speed allowed in RPM.
•
Back EMF[V]/Back EMF[RPM]:
insert the BACK EMF of the motor[V/RPM].
All other parameters are not to be set.
Bru hall sensor
With this coupling set only the following parameter:
•
Resolution:
the value is calculated with the following formula:
Resolution = hall cell number * 2
•
Phase Angle:
It visualizes the phasing angle of the motor, previously calculated with the “
Au-
toPhasing
” procedures.
All other parameters are not to be set.