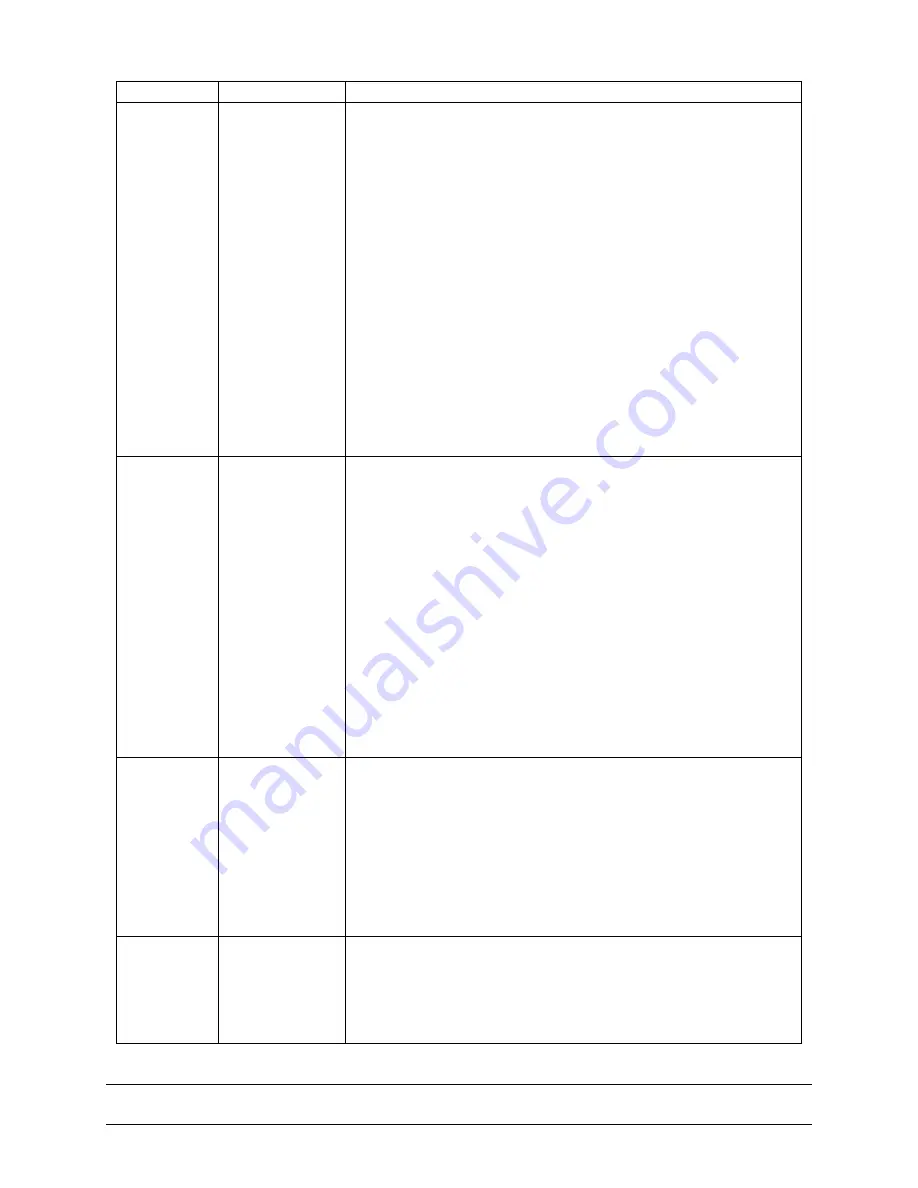
CRANE
CO.
280
N.
MIDLAND
AVE.,
STE
258,
SADDLE
BROOK,
NJ
07663
WWW.AVIDCONTROLS.COM
12/17/12
TECH-440/D.W.O. 23135
Page 38 of 55
Message Meaning Solution
PWM
overflow
During
calibration an
error occurred
with the PWM
signal that
control the
spool-valve
driver and the
position is not
following the
control signal
Check:
Hall sensor connector and cable, especially if remote (see
Figure 3-4, connector J8)
Magnet assembly is in correct position.
o
For rotary magnets check if it is not rotated 90
degrees (see figures 3.2, 3.3 and 3.4).
o
For linear magnets, check if the magnet assembly
center is matching the actuator mid position (see
figures 3.5, 3.6 and 3.7). Check if the proper fail-down
or fail-up magnet is being used (figure 5.1)
Check if the cable between the inner canister and the
pneumatic transducer assembly is tightly connected
Check the cable and connector between the transducer board
and the spool-valve coil.
Try to replace the Hall sensor and/or the magnet
Remove power for at least 1 minute and retry
Remove power for at least 1 minute, perform a factory default
(see Appendix I) and retry a full auto CAL
Call factory for additional support
HALL
sensor out
of range
(SEN, LO, HI, T)
Hall sensor
used to read
position is
unstable
Check:
Hall sensor connector and cable, especially if remote (see
Figure 3-4, connector J8)
Magnet assembly. For rotary magnets check if it is not rotated
90 degrees (see figures 3.2, 3.3 and 3.4). For linear magnets,
check if the magnet assembly center is matching the actuator
mid position (see figures 3.5, 3.6 and 3.7)
Remove power for at least 1 minute, perform a factory default
(see Appendix I) and retry the calibration
Grounding issues, cable shield is grounded properly,
positioner ground is properly connected to a clean ground
reference.
Sources of electromagnetic noise too close to the sensor or to
the positioner cables, like AC cables for motors, inverters etc
Try to replace the Hall sensor and/or the magnet
Call factory for additional support
mA input
A/D is not in
linear range
An invalid loop
current is
applied during
set-point
calibration
Check:
Check if the current generator is set at the proper value
(between 3.8mA and 20.5mA)
Check the set-point value on the LCD and adjust the current
generator accordingly
Make sure the minimum loop current span is at least 1.6mA
Remove power for at least 1 minute, perform a factory default
(see Appendix I) and retry a full auto CAL
Call factory for additional support
Illegal
calibration
code
An unknown
error has
occurred during
calibration
Check:
Remove power for at least 1 minute and retry
Remove power for at least 1 minute, perform a factory default
(see Appendix I) and retry a full auto CAL
Call factory for additional support