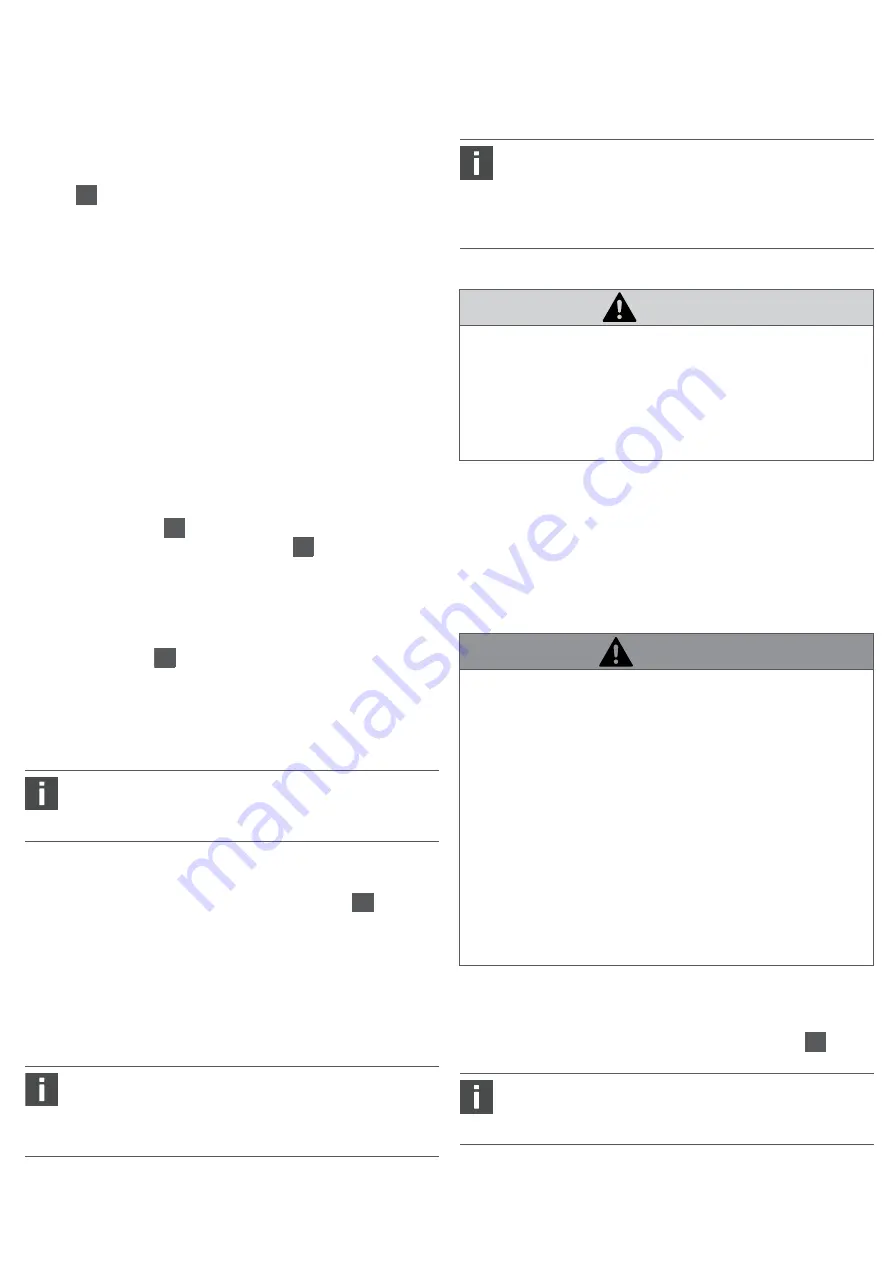
AVENTICS
| GSU | R402002667–BAL–001–AC | English
11
7
Commissioning
O
The blanking plugs must be left in the cylinder
connections until the compressed air lines are
connected.
O
Before commissioning, with the cylinder vented, check
that the slide is not stiff to move, does not move
unevenly or get stuck along the stroke of the cylinder
by manually pulling the slide.
Connecting the compressed air supply
The compressed air can be connected both axially and
radially to only one cover or to both covers. See
.
The connections for piston size 16 mm are size M5, while
those for piston size 25 mm have the size G 1/8.
1.
Remove any blanking plugs (
1
) from the connections.
Commissioning of the guided slide unit may only
be carried out by qualified electrical or pneumatic
personnel or an instructed person under the
direction and supervision of qualified personnel
(see also “Personnel qualifications”).
CAUTION
Improper installation of the guided slide unit poses a
risk of injury or damage!
An improperly installed guided slide unit can come
loose during operation and cause damage to other
system parts or injuries.
O
Carefully check that all components are securely fixed.
WARNING
Risk of crushing or impact!
If the compressed air is connected incorrectly, the slide
can move in the wrong direction or be operated at high
speeds, posing a high risk of injury or damage.
O
Check whether the compressed air supply is
connected to the correct connection.
O
Check whether all connections are connected and
sealed with plugs.
O
To prevent uncontrolled runaway of the slide during
the approach, increase the pressure slowly and use
the speed control.
O
Make sure that no one is in the risk area when the
compressed air supply is turned on.
The connections are labeled with direction arrows
so that the compressed air lines can be connected
in the correct direction in pairs.
8
Mounting the sensors
Magnetic sensors can be mounted with different spacing
in order to sense the position of the slide on the cylinder.
The cylinder body has slots to hold the sensors on the top
and side.
Figure
shows an example for positioning a sensor on
top of the cylinder body. Do not install more than two
sensors per slot to ensure the cables can be laid without
any obstruction.
1.
Place the sensor (
1
) at the desired position in the
sensor slot and align the sensor in the slot so that the
screw faces upwards.
2.
Guide the cable in the slot through the notch (
2
) in the
cover.
3.
Carefully tighten the screw in the sensor.
4.
Carefully tauten the cable and make sure that it does
not present an obstacle. If necessary, fix it with cable
ties or similar.
Adjusting the stroke
The stroke of the GSU guided slide unit is initially adjusted
coarsely by moving the bracket with the stop screw along
the base plate; see
. Next, fine adjustment can be
performed using the stop screw; see
.
1.
Carefully loosen the two screws (
1
) holding the bracket
(
2
) in place.
Do not remove the screws completely. Otherwise,
the sheet (
3
) connecting the cover to the base plate will
fall down. See
.
2.
Slide the bracket in the slot (
4
) of the base plate to the
correct position for the desired stroke.
3.
Tighten the screws to fix the bracket. Tightening
torque: GSU 16: 6.5 Nm, GSU 25: 11 Nm.
4.
Repeat steps 1 to 3 for the other end of the cylinder.
5.
Measure the stroke, then perform fine adjustment
using the stop screw (
5
) in the bracket; see
. Secure
the stop screw using the nut (
6
).
Attaching a load
Normally, loads are attached with the “Easy-2-Combine”
system, which can be attached directly to other AVENTICS
cylinders with high precision.
In delivery condition, the brackets are only
mounted tentatively. They must be tightened with
the correct torque!
Make sure that the load is properly attached for
the specific application and that the attachment
can handle the load for which the guided slide unit
is dimensioned.
5
6
7
6
7
Summary of Contents for GSU16
Page 45: ......