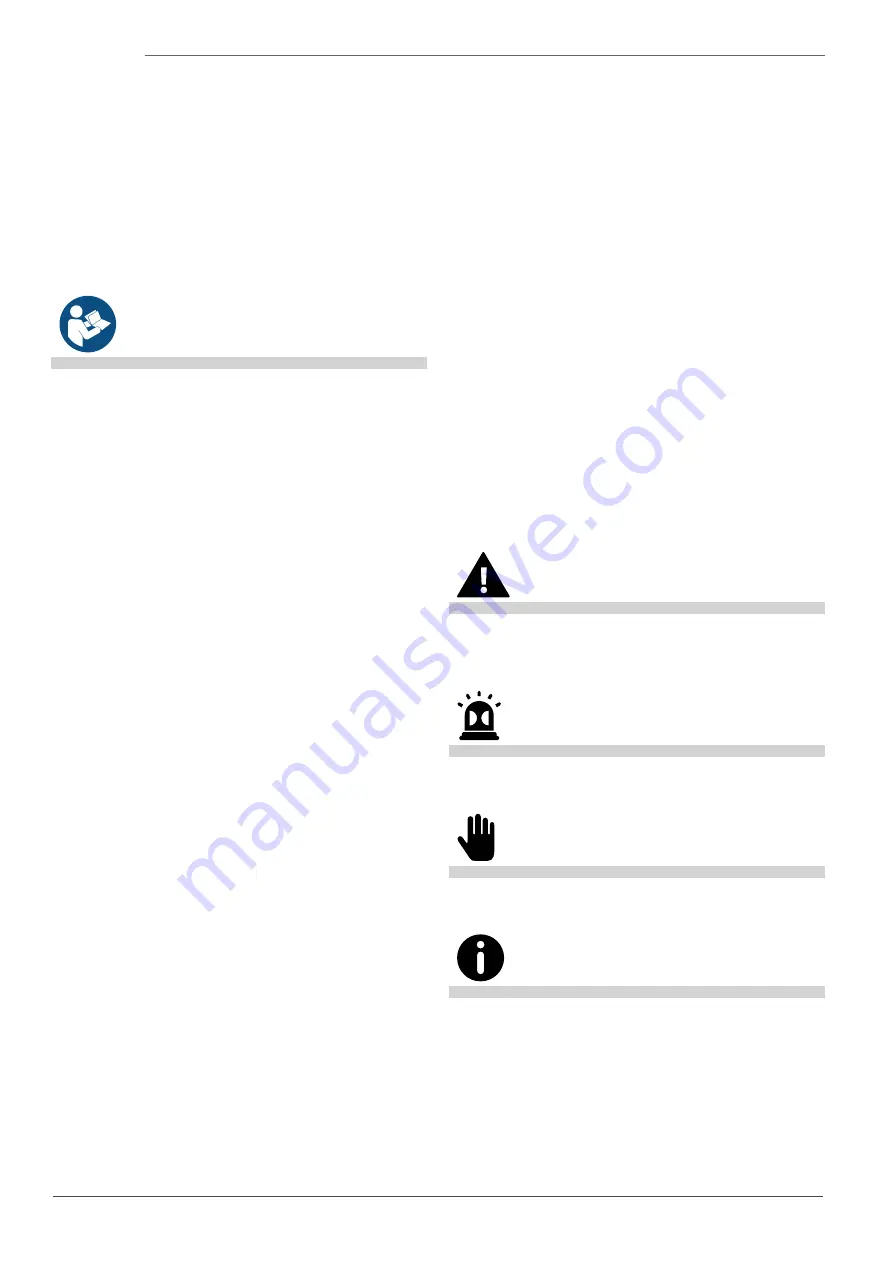
8
of
54
TECHNICIANS' manual
Core200
1.
INTRODUCTION
Read this manual carefully. It provides important
safety information to the Maintenance Technician regard-
ing the operations indicated in this document.
Keep this Manual in a safe place. If you lose it, you can
ask the Manufacturer for another copy.
The Manufacturer of the appliance cannot be held
responsible for any damage caused due to the non-
observance of the requirements listed in this manual.
Before operating on the machine, read the instructions contained
in this publication and follow the guidelines carefully. Keep this
manual and all attached publications in an accessible and secure
place.
This document assumes that the machine is installed
in a location where the current work safety and hygiene
standards are observed.
The instructions, drawings and documentation con-
tained in this Manual are technical and confidential. They
are the sole property of the Manufacturer, and may not
be fully or partially reproduced in any way.
The Manufacturer reserves the right to make any
improvements and/or modifications to the product. We
guarantee that this Manual reflects the technical state of
the appliance at the time it was released to the market.
We encourage the Maintenance Technicians to make
any proposals in regards to improving the product or its
Manual.
1.1
Guidelines for reading the Manual
This Manual is divided into separate chapters. The
chapter order is linked to the temporal logic of the life
of the machine.
Terms, abbreviations and pictograms are used to
facilitate the immediate understanding of the text.
This Manual consists of cover, index and a series of
chapters. Each chapter is sequentially numbered. The
page number is shown in the footer.
The machine identification data is displayed on the
machine’s nameplate and the CE declaration of Con-
formity, whilst the date and revision of the Instruction
Manual is provided on the last page.
ABBREVIATIONS
Sec.
= Section
Chap.
= Chapter
Para.
= Paragraph
P.
= Page
Fig.
= Figure
Tab.
= Table
UNITS OF MEASUREMENT
The units of measurement are those provided by the
International System (SI).
PICTOGRAMS
Descriptions preceded by these symbols contain very
important information/requirements, particularly in re-
gards to safety. Failure to comply with these may result in:
•
A safety risk for those operating the machine;
•
Injury, including serious injury (in some cases even
death);
•
Loss of the guarantee;
•
The Manufacturer waiving liability.
DANGER symbol used when there is a risk of permanent serious
injury that would require hospitalisation, or in extreme cases,
even cause death.
CAUTION symbol used when there is a risk of minor injury that
could require medical attention.
WARNING symbol used when there is a risk of minor injury that
could be treated with first-aid or similar measures.
NOTE symbol used to provide important information about the
topic.
Summary of Contents for 10003318
Page 53: ......