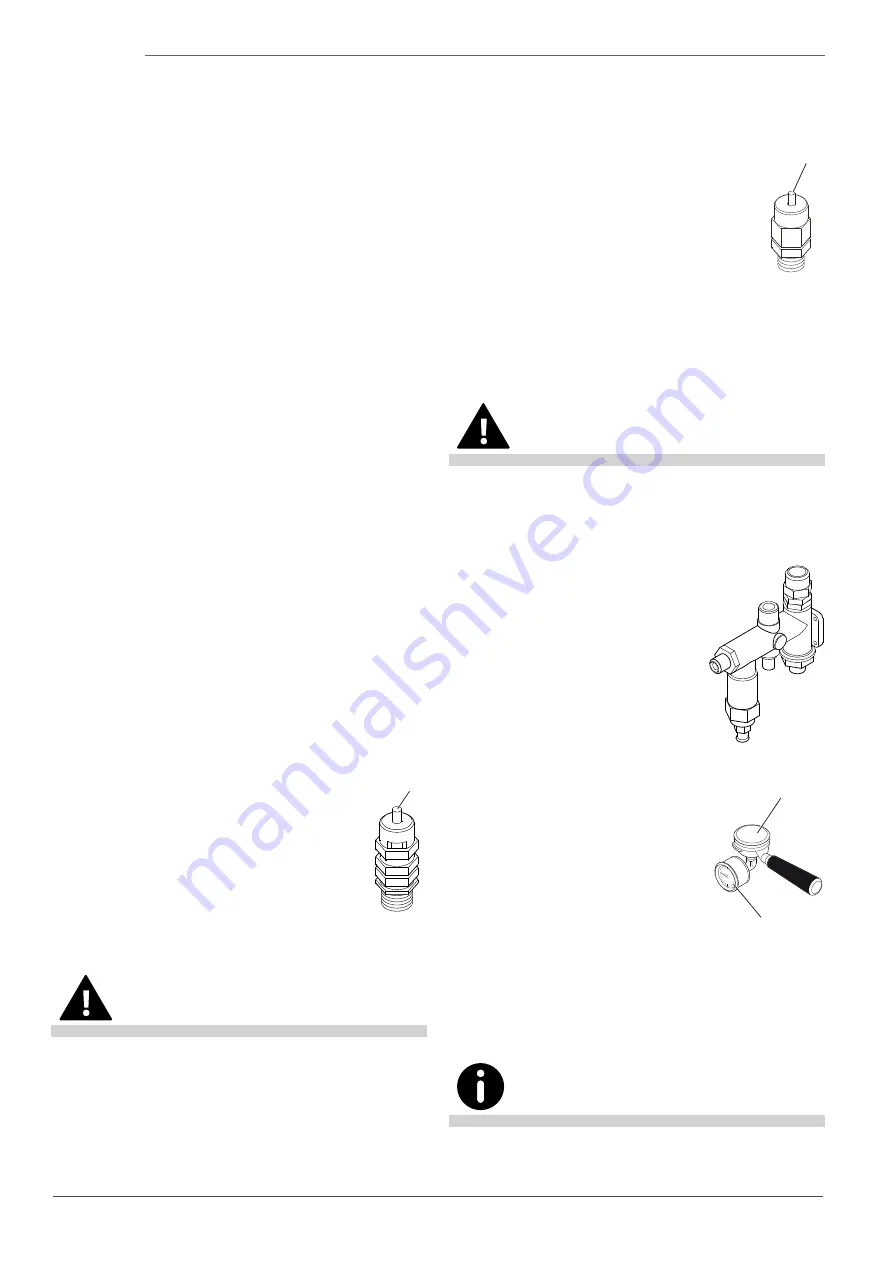
34
of
54
TECHNICIANS' manual
Core200
8.3.3 Maintenance after a short period of machine
inactivity
“Short machine downtime” refers to a period of time
exceeding one working week.
If the machine is switched back on after this period, all
of the water inside the hydraulic circuits must be replaced
as indicated in par. 6.10 .
All the scheduled maintenance operations must also
be performed - see the previous par. 8.3.1 .
8.3.4 Dispensing group maintenance
Replace the dispensing group's shower screen
(B)
and
group gasket
(D)
on a quarterly basis (it is recommended
to use original spare parts only), by proceeding as follows:
•
Unscrew the screw
(A)
;
•
Remove the shower screen containment ring
(C)
;
•
Replace the group shower screen
(B)
and the rubber
group gasket
(D)
;
•
Reassemble the components.
8.3.5 SAFETY VALVE check
The pressure relief valve is one of the main compo-
nents for machine safety. Therefore, it is important to
carry out the following checks:
First check :
•
Eemove the machine's upper grille;
•
Use pliers to pull the valve pin
(E)
upwards;
•
If the pin will not budge, it probably means that the
valve is encrusted with limestone and must
be replaced.
Second check :
•
Turn the machine off;
•
Close off the pressure switch contacts;
•
Turn the machine back on and wait for the
pressure in the heating unit to rise;
•
Check that the valve is working correctly at the ma-
ximum pressure of 0,19 MPa (1,9 bar).
If any malfunctions are detected, the valve must be replaced. Only
use the Manufacturer's original Safety Valves.
8.3.6 NEGATIVE PRESSURE VALVE check
First check:
•
Remove the machine's upper grille;
•
Use pliers to push the valve pin
(
F
)
downwards;
•
If the pin will not budge, it probably
means that the valve is encrusted with
limestone and must be replaced.
Second check:
•
Turn the machine off;
•
Open the steam valves and release all the pres-
sure from inside the heating unit;
•
Turn the machine back on and check that the valve
is closing normally.
If any malfunctions are detected, the valve must be replaced.
8.3.7 NON-RETURN DRAIN VALVE check
The non-return drain valve is an
important component for the correct
operation of the machine. Perform the
check as follows:
•
Activate the dispensing
groups for about 30 seconds;
•
Attach a filter holder
(
G
)
with
a pressure gauge (available
on request) to the dispensing
group;
•
Activate the dispensing group,
and use the pressure gauge
(
H
)
to monitor the pressure as
it increases up to 0,8-0,9 MPa
(8-9 bar);
•
Check that the pressure is
increasing due to the heated
water expanding until it
reaches approximately 1,2 MPa
(12 bar): when this value is reached, it confirms
that the valve is working correctly and the seals
and solenoid valves are tight;
•
Stop dispensing;
•
Repeat the check on the other dispensing groups.
If any malfunctions are detected, the valve must be replaced.
E
F
G
H
Summary of Contents for 10003318
Page 53: ......