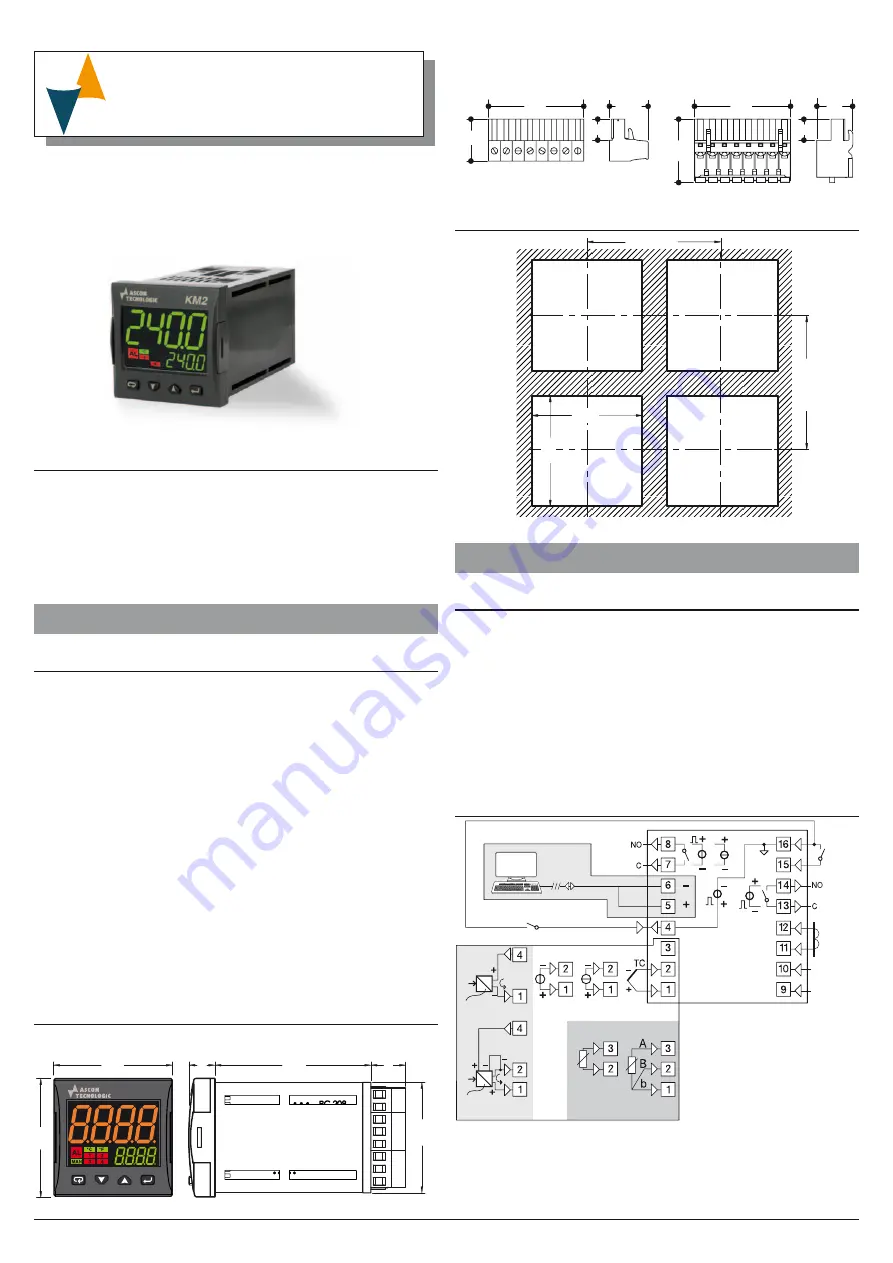
Ascon Tecnologic - KM2 Line - ENGINEERING MANUAL - PAG. 1
KM2
CONTROLLER AND
MINI-PROGRAMMER WITH
HEATER BREAK DOWN ALARM
Engineering Manual
Code : ISTR-MKM2ENG01 - Vr. 1.0 (ENG)
Ascon Tecnologic S.r.l.
Viale Indipendenza 56, 27029 Vigevano (PV) - ITALY
Tel.:
+39 0381 69871/
FAX:
+39 0381 698730
www.ascontecnologic.com
e-mail:
1. OUTLINE DIMENSIONS (mm)
1.1 Mounting requirements
This instrument is intended for permanent installation, for
indoor use only, in an electrical panel which encloses the
rear housing, exposed terminals and wiring on the back.
Select a mounting location having the following characteristics:
1.
It should be easily accessible;
2.
There is minimum vibrations and no impact;
3.
There are no corrosive gases;
4.
There are no water or other fluids (i.e. condensation);
5.
The ambient temperature is in accordance with the
operative temperature (0... 50°C);
6.
The relative humidity is in accordance with the instrument
specifications (20... 85%);
The instrument can be mounted on panel with a maximum
thickness of 15 mm.
When the maximum front protection (IP65) is desired, the
optional gasket must be mounted.
1.2 Dimensions
1.2.1 Controller with non removable terminals
63.3
14
11
44.5
PV
AT
48
48
1.2.2 Removable terminals
40
15.5
18.85
26
15
8.3
40
8.3
Screw removable terminals
Spring removable terminals
1.3 Panel cutout
45
+0.6
65 mm min.
65 mm min.
45
+0.6
2. ELECTRICAL CONNECTIONS
2.1 General notes about wiring
1.
Do not run input wires together with power cables.
2.
External components (like zener barriers, etc.) connected
between sensor and input terminals may cause errors in
measurement due to excessive and/or not balanced line
resistance or possible leakage currents.
3.
When a shielded cable is used, it should be connected at
one point only.
4.
Pay attention to the line resistance; a high line resistance
may cause measurement errors.
2.2 Wiring diagram
C.T. input
50 mA AC
Relay Out 1:
4 (4) A/250 VAC
Relay Out 2:
2 (1) A/250 VAC
SSR Out 1, 2:
10 Vdc/15 mA
Out1:
0/4... 20 mA, 0/2... 10V
SSR Out 3:
12 Vdc/20 mA
Note: Terminal 4 can be porogrammed
as Digital Input, Logic output or
Transmitter PWS
Thermocouple
DI1
Out2
Out3
DI2 (note)
Analogue input
mV, V
mA
12 VDC
(note)
PV
Passive 4... 20 mA
2 wires
Transmitter
3 wires
12 VDC
(note)
PV
Transmitter
Pt100
Pt1000/NTC/PTC
Out1
RS485
Power
supply
AC/DC