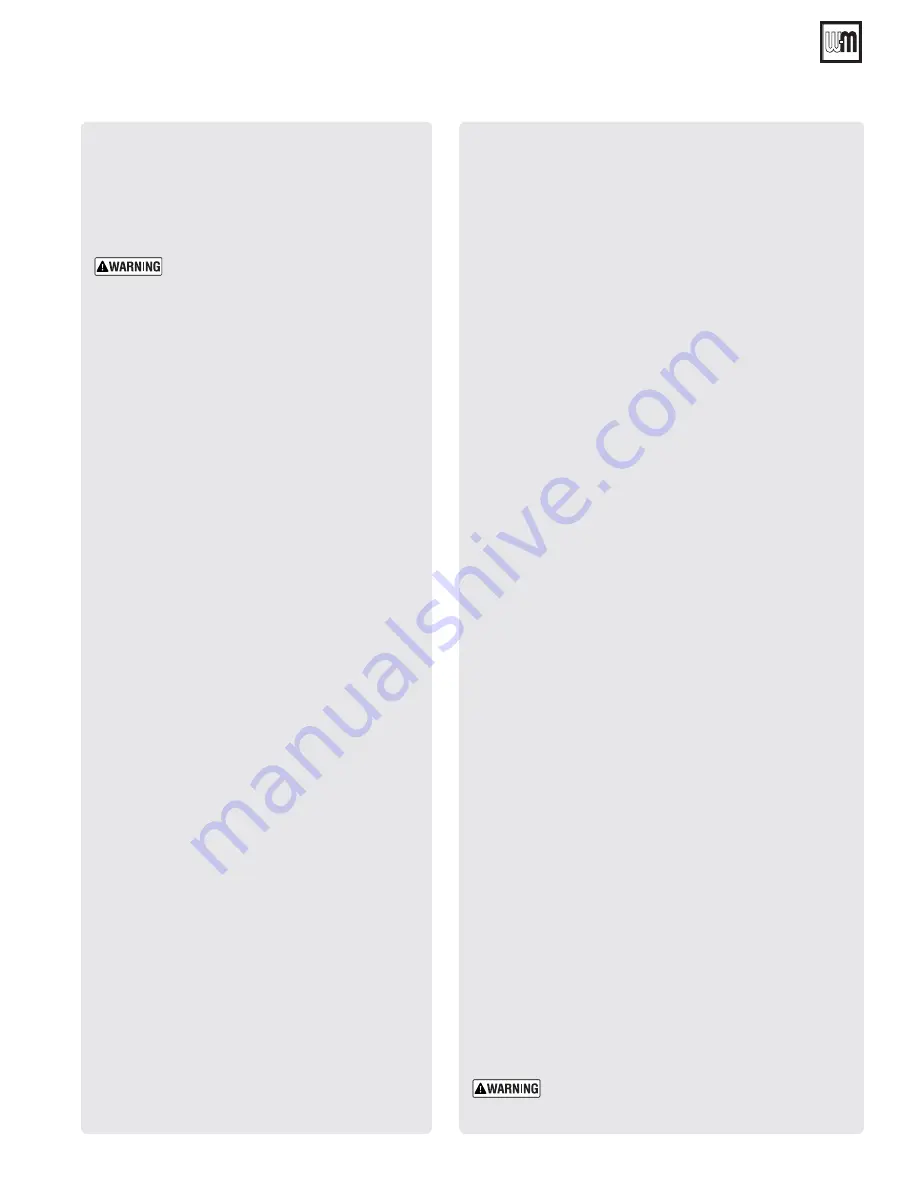
Part number 550-100-305/0916
67
AquaBalance
TM
W
ALL
M
OUNT
GAS
-
FIRED
WATER
BOILER
— C
OMBI
Boiler Manual
31
Annual startup
HANDLING CERAMIC FIBER
MATERIALS
2%-/6).'"52.%2'!3+%4OR
#/6%20,!4%).35,!4)/.
The heat exchanger refractory contain
ceramic fiber materials that have been
identified as carcinogenic, or possibly
carcinogenic, to humans). Ceramic fibers
can be converted to cristobalite in very
high temperature applications.
The International Agency for Research on
Cancer (IARC) has concluded, “Crystal-
line silica inhaled in the form of quartz or
cristobalite from occupational sources is
carcinogenic to humans (Group 1).”:
■
Avoid breathing dust and contact with skin and eyes.
s
Use NIOSH certified dust respirator (N95).
This type of respirator is based on the OSHA
requirements for cristobalite at the time this
document was written. Other types of respira-
tors may be needed depending on the job site
conditions. Current NIOSH recommendations
can be found on the NIOSH web site at http://
www.cdc.gov/niosh/homepage.html. NIOSH
approved respirators, manufacturers, and phone
numbers are also listed on this web site.
s
Wear long-sleeved, loose fitting clothing,
gloves, and eye protection.
■
Handle carefully to minimize dust that could be
caused by abrasion.
■
If replacement is necessary, remove the refractory
from the boiler and place it in a plastic bag for
disposal.
■
Wash potentially contaminated clothes separately
from other clothing. Rinse clothes washer thor-
oughly.
.)/3(STATED&IRST!ID
■
Eye: Irrigate immediately
■
Breathing: Fresh air.
FIRST-YEAR SPECIAL INSPECTION
1.
.OLATERTHANMONTHS
after the boiler is installed, per-
form a first-year inspection of the boiler. This should include
the following
IN ADDITION TO ROUTINE ANNUAL STARTUP
PROCEDURES
.
a. The integrity of the flue system and the flue seals;
b. The integrity of the boiler combustion circuit and the
relevant seals;
c. The operational (working) gas inlet pressure at
maximum rate, as described on pages 45 and 64;
d. The gas rate, as described on page 45;
e. The combustion performance, as described on pages 62,
63 and 64 for combustion check.
f. Competence to carry out the check of combustion per-
formance.
g. The person carrying out a combustion measurement
should have been assessed as competent in the use of a
flue gas analyzer and the interpretation of the results;
Periodical check
h. To keep the unit working properly over time, it is necessary to
have qualified personnel make an annual check that includes
the following tests:
i.
The control and safety devices (gas valve, flow meter,
thermostats, etc.) must function correctly.
j.
The flue pipes must be fully intact, secure and clear.
k. The airtight chamber must be sealed.
l. The air-flue terminal and ducts must be free of obstructions
and leaks.
m. The condensate evacuation system must be efficient with no
leakage or obstructions and drain condensate without back-
ing up.
n. The burner and heat exchanger must be clean and free of scale.
When cleaning, do not use chemical products or wire brushes.
o. The electrode must be free of scale and properly positioned.
p. The gas and water systems must be leak free.
q. The water pressure in the heating system must be minimum of
12 PSI, do not exceed 25 PSI. Fill the boiler to that pressure or
the system design pressure.
r. The circulation pump must not be blocked.
s. The expansion tank must be filled.
t.
The gas flow and pressure must correspond to that given in the
respective tables.
2. Determine any follow-up maintenance and service needs based on
the condition of the heat exchanger and condensate lines.
a. If the heat exchanger shows substantial fouling, or if condensate
lines show accumulation of sediment, schedule a follow-up
service call to perform the first-year inspection again, sooner
than the normal twelve months between.
b. Heavy fouling of the heat exchanger or condensate lines indi-
cates possible combustion air contamination. Inspect the air
intake area carefully, and remove possible contaminants. See
page 8, for products to avoid.
You must eliminate causes of corrosion and con-
tamination to ensure reliable operation of the boiler
and system.