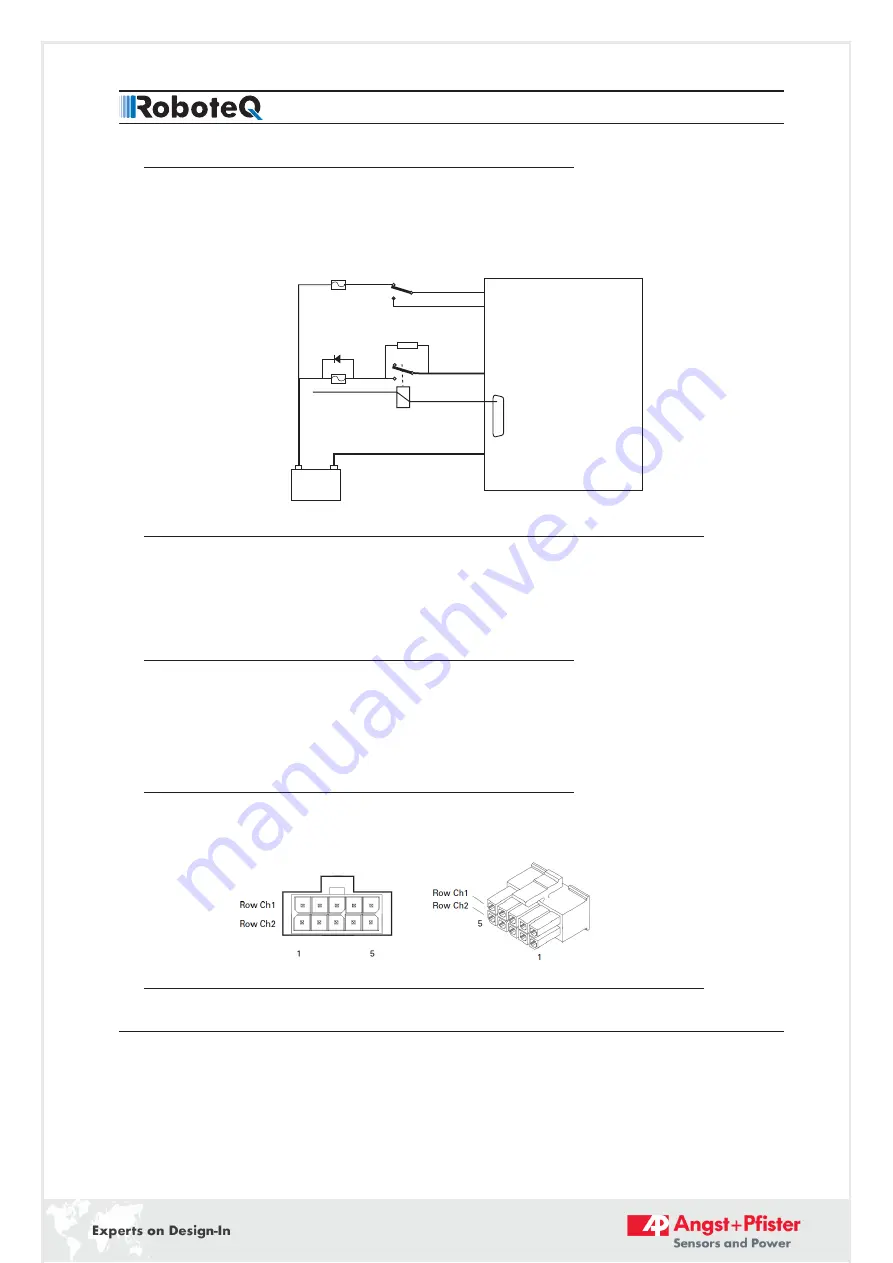
6
FBL2360 Brushless DC Motor Controller Datasheet
Version 1.3 August 29, 2019
Use of Safety Contactor for Critical Applications
An external safety contactor must be used in any application where damage to property or
injury to person can occur because of uncontrolled motor operation resulting from failure
in the controller’s power output stage.
PwrCtrl
SW1 Main
On/Off Switch 1A
F2
1A
Diode
>20A
Resistor
1K, 0.5W
+
-
F1
I/O Connector
VMot
to +40V Max
Digital Out
Ground
Ground
Main
Battery
FIGURE 1.Contactor wiring diagram
FIGURE 5. Contactor wiring diagram
The contactor coil must be connected to a digital output configured to activate when
“No MOSFET Failure”. The controller will automatically deactivate the coil if the output
is expected to be off and battery current of 1A or more is measured for more than 0.5s.
This circuit will not protect against other sources of failure such as those described in the
“Important Safety Disclaimer” on page 3.
Controller Mounting
During motor operation, the controller will generate heat that must be evacuated. The
published amps rating can only be fully achieved if adequate cooling is provided. Good
conduction cooling can be achieved by having the bottom surface of the case making
direct contact with a metallic surface (chassis, cabinet). The mounting has to be like that,
so that the thermal-safety limits are not exceeded.
Hall Sensors Connection
Connection to the Hall Sensors is done using a special connector on the front side of the
controller. The Hall sensor connector is a 10-pin Molex Microfit 3.0, ref. 43025-1000. Pin
assignment is in the table below.
FIGURE 6. Hall Sensors connector
6
FBL2360_1691-21588-0001-D-0720