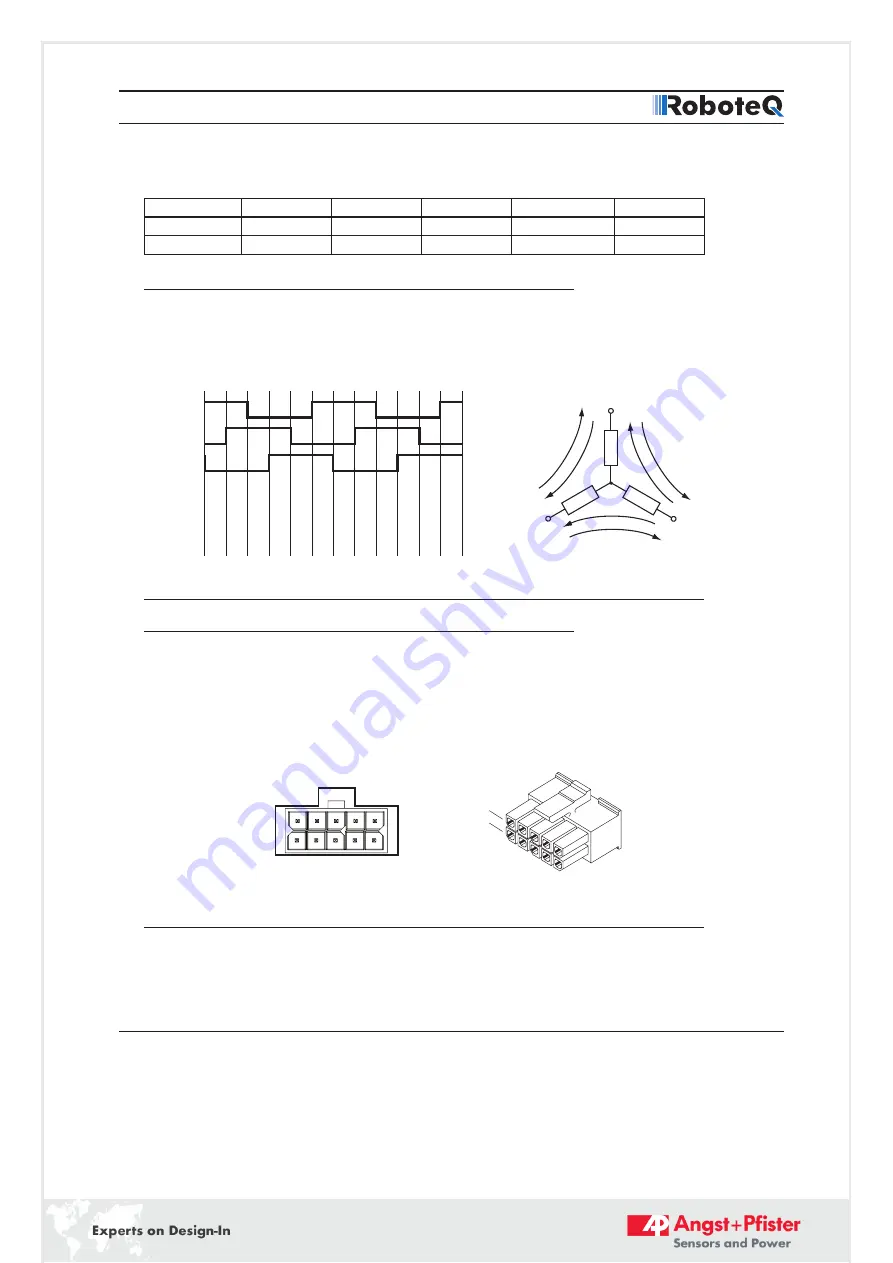
FBL2360 Brushless DC Motor Controller Datasheet
7
Connection to SPI Absolute Encoder
TABLE 1.
Pin Number
1
2
3
4
5
Row Ch1
5V
Hall1 C
Hall1 B
Hall1 A
Ground
Row Ch2
5V
Hall2 C
Hall2 B
Hall2 A
Ground
Hall Sensor vs Motor Output sequencing
The controller requires the Hall sensors inside the motor to be 120 degrees apart.
The controller’s 3-phase bridge will activate each of the motor winding according to the
sequence shown in the figure below.
FIGURE 7. Hall Sensors sequence
Connection to SPI Absolute Encoder
In Sinusoidal Mode, the FBL2360 and FBL2360S models can use motors equipped with
absolute angle sensors with SPI interface, such as found on the BL167 or BL90 motors
from Micromotor. When enabled, the SPI signals are found on the 10-pin Molex connector
that is otherwise used for the Hall Sensors. The controller issues a clock and select signal.
When two motors are used, these signals must be connected to both sensors. Serial data
from each sensor is captured on separate input pins. The SPI Encoder is not available on
‘A’, ‘T’ and ‘E’ versions of Roboteq products.
FIGURE 8. Hall Sensor connector used for SPI encoders
U
V
W
1 2 3 4 5 6 1
4
2
5
3
6
4
1
5
2
6
3
Hall A
Hall B
Hall C
U
V
W
+
-
-
-
-
-
-
-
-
-
-
-
-
+ +
+ +
+ +
+ +
+ +
+
1
Row 2
Row 2
Row 1
Row 1
1
5
5
7
FBL2360_1691-21588-0001-D-0720