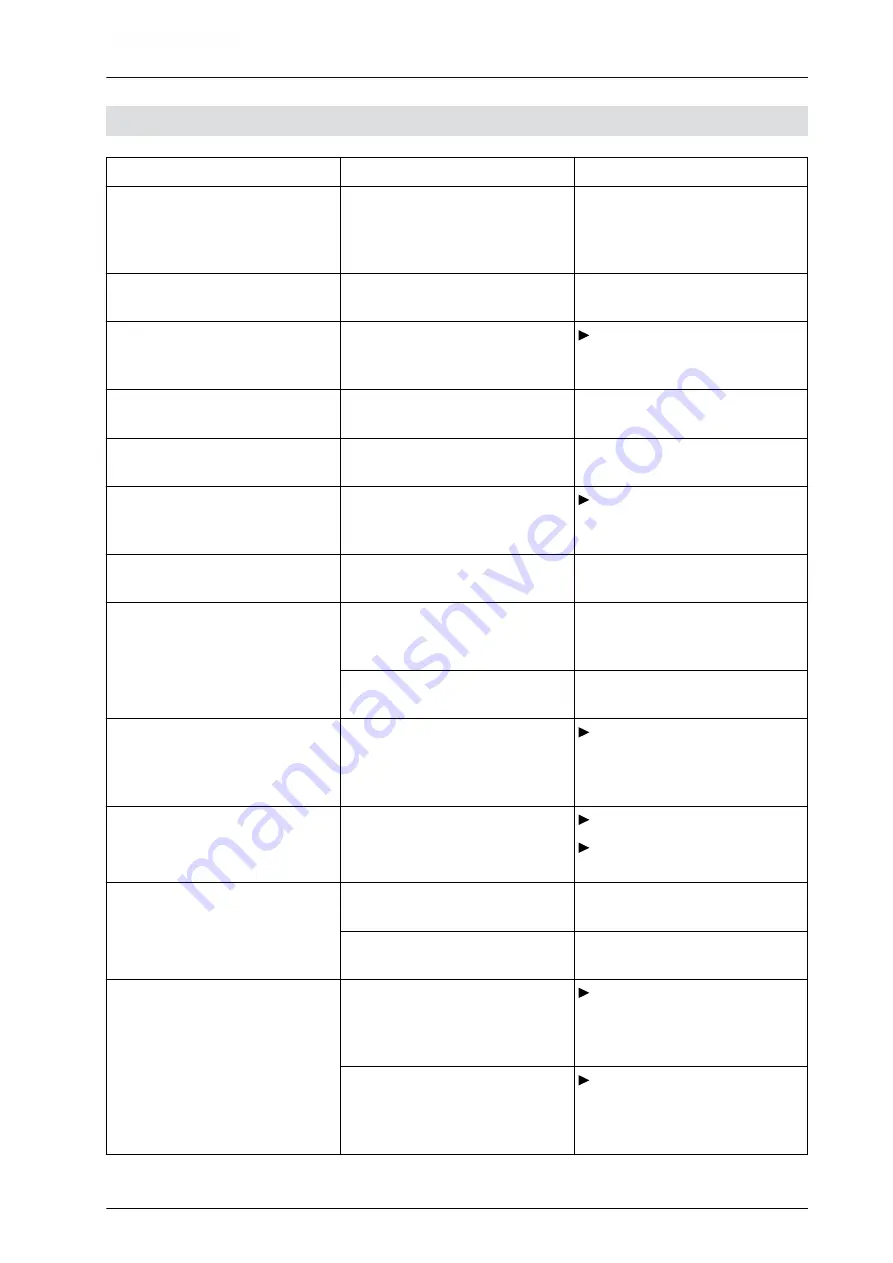
9.4 Eliminating faults
Errors
Cause
Solution
Track marker collision protection
has been triggered.
The track marker has encountered
a solid obstacle. The shear bolt is
torn and the track marker folded to
the rear.
Gaps can be caused by insufficient
seed in the grain singling unit.
Bridge formation disturbs the seed
flow in the grain singling unit.
An increased cleaning effort of the
opto-sensor is observed.
Talc in the seed shortens the
cleaning interval of the opto-
sensor.
Clean the opto-sensor.
The seed is not caught and jumps
out of the furrow.
The seed collides against the catch
roller or against the seed furrow.
The control terminal shows a
spread rate error.
The shot channel is blocked.
The control terminal shows a
speed error.
Check the gap on the inductive
sensor. Defect on the mechanical
drive.
Adjust the distance between
the inductive sensor and pulse
wheel to 1-2 mm.
Press rollers get blocked.
Clods or stones get jammed
between the press rollers.
Blocking the depth control wheels.
Soil gets stuck between the cutting
discs and the depth control wheels
with closed rim.
Organic residues get stuck on the
open rims.
The electric drives do not run or
start running at the wrong time.
The switch points of the working
position sensor are wrong.
To configure the working
position sensor,
see "Configuring the working
position sensor".
The lighting for road travel has a
malfunction.
Lamp or lighting supply line is
damaged.
Replace the lamp.
Replace the lighting supply
line.
Stopping of one or several singling
discs.
The fuse for the electric drive is
defective.
Fuse for the mechanical drive is
defective.
The grain spacings are larger than
the setpoint.
Too much slip on the drive wheels.
To configure the working
position sensor,
see "Configuring the working
position sensor".
Too much slip on the drive wheels.
To configure the working
position sensor,
see "Configuring the working
position sensor".
CMS-T-00005550-B.1
9 | Repairing the machine
Eliminating faults
MG6967-EN-II | C.1 | 27.09.2021
225