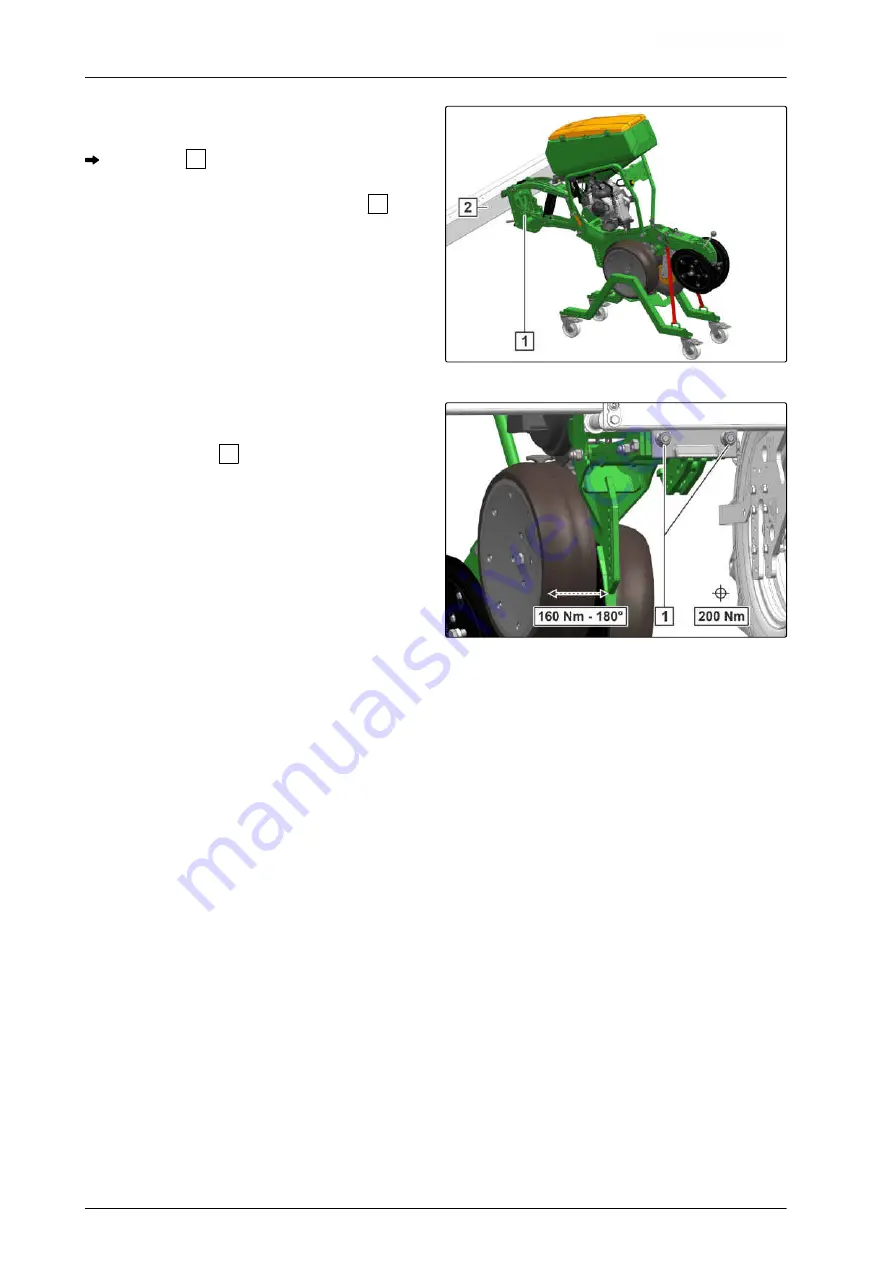
21. Continue lowering the implement.
The coulter
1
tips forward.
22. Release the tilted coulter from the frame
2
.
CMS-I-00005133
23.
To move the remaining coulters to the desired
position,
Loosen the bolts
1
.
24. Push the coulters into the desired position.
25.
For telescopic coulters
Tighten the bolts to 160 Nm -180°,
or
For non-telescopic coulters
Tighten the bolts to 200 Nm.
26. Connect the ISOBUS to the tractor.
27. Restart the implement.
28.
To enter the changed working width on the
control terminal,
see "ISOBUS software operating manual" >
"Defining the geometry".
CMS-I-00002039
6 | Preparing the machine
Preparing the implement for operation
MG6967-EN-II | C.1 | 27.09.2021
156