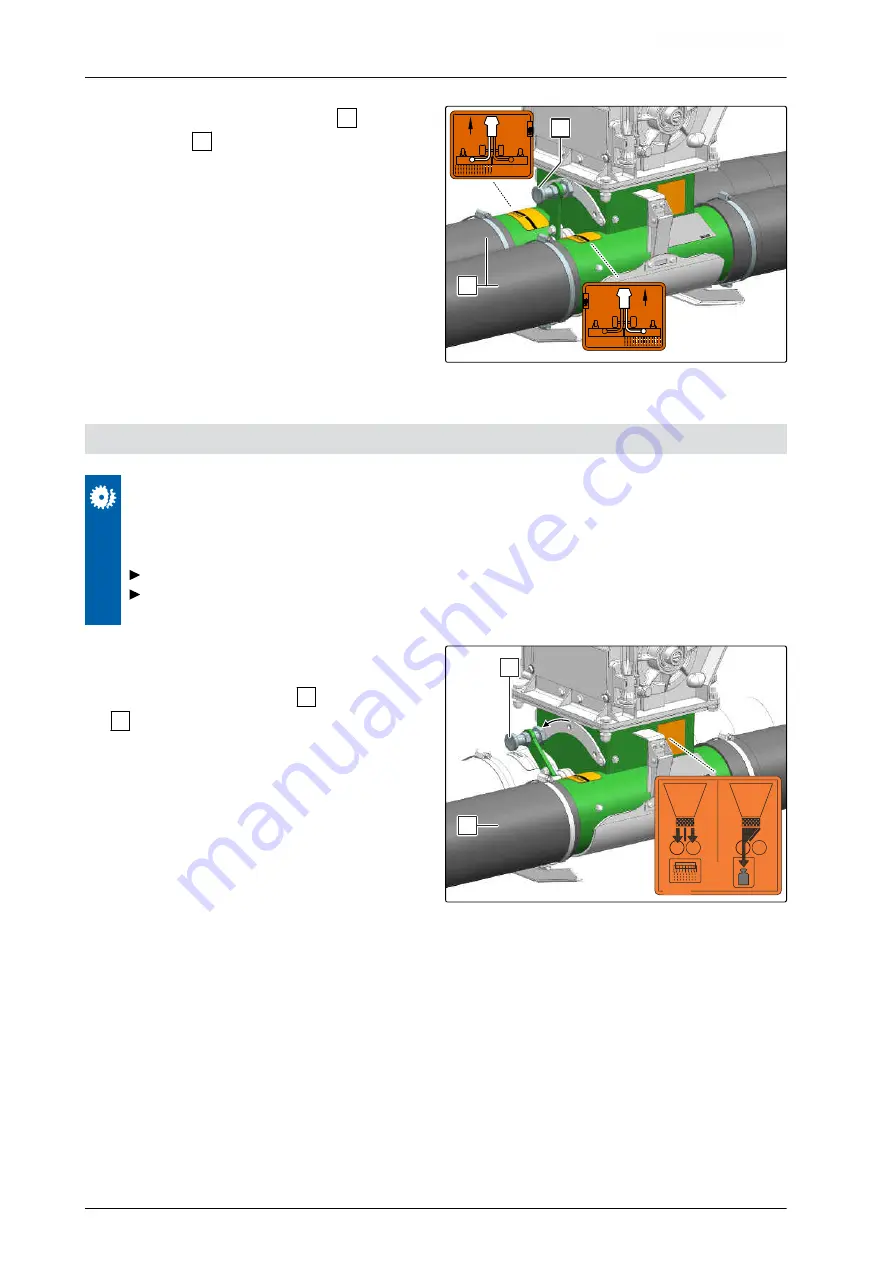
30.
To activate both conveyor sections
2
,
put the lever
1
back in the centre position.
R
L
1
2
CMS-I-00002543
8.2 Emptying the metering unit
IMPORTANT
Risk of damage to the metering drive due
to swelling fertiliser or germinating seed.
Empty the metering unit after operation.
Clean the metering unit after operation.
1.
If the implement is equipped with a double
sluice,
activate the conveyor section
2
with the lever
1
.
2
1
Cal
ME1080
CMS-I-00002542
CMS-T-00003326-B.1
8 | Parking the machine
Emptying the metering unit
MG6492-EN-II | G.1 | 26.04.2021
94