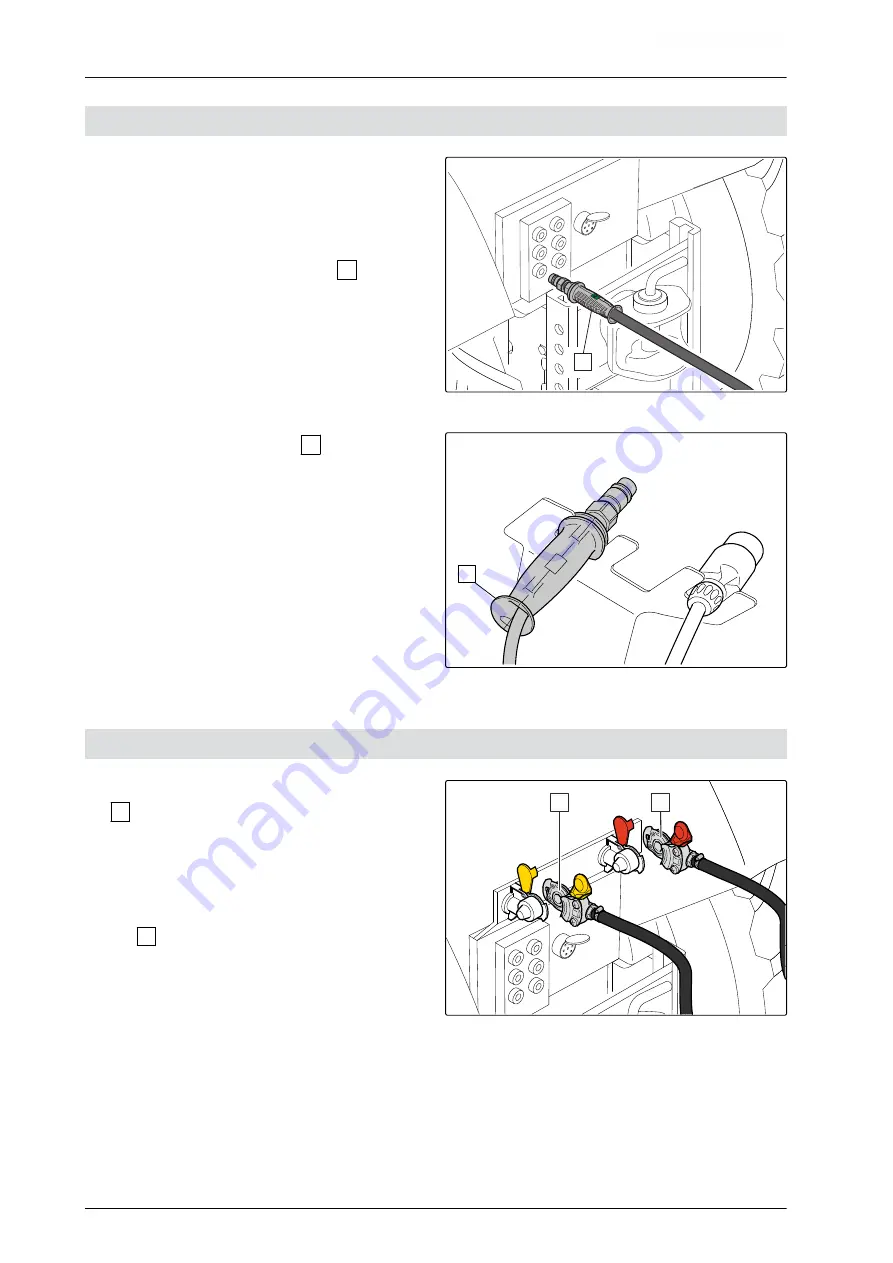
9.7 Disconnecting the hydraulic hose lines
1.
Secure the tractor and implement.
2.
Put the control lever on the tractor control unit in
float position.
3.
Disconnect the hydraulic hose lines
1
.
4.
Put the dust caps on the hydraulic sockets.
1
CMS-I-00001065
5.
Hang the hydraulic hose lines
1
in the hose
cabinet.
1
CMS-I-00001250
9.8 Uncoupling the pneumatic brake system
1.
Uncouple the red coupling head of the brake line
2
from the tractor.
2.
Couple the red coupling head with the empty
coupling on the implement.
3.
Uncouple the yellow coupling head of the brake
line
1
from the tractor.
4.
Couple the yellow coupling head with the empty
coupling on the implement.
5.
Close the tractor coupling head caps.
1
2
CMS-I-00003559
CMS-T-00000277-E.1
CMS-T-00004570-C.1
9 | Parking the machine
Disconnecting the hydraulic hose lines
MG7478-EN-GB | C.1 | 19.08.2022 | © AMAZONE
84