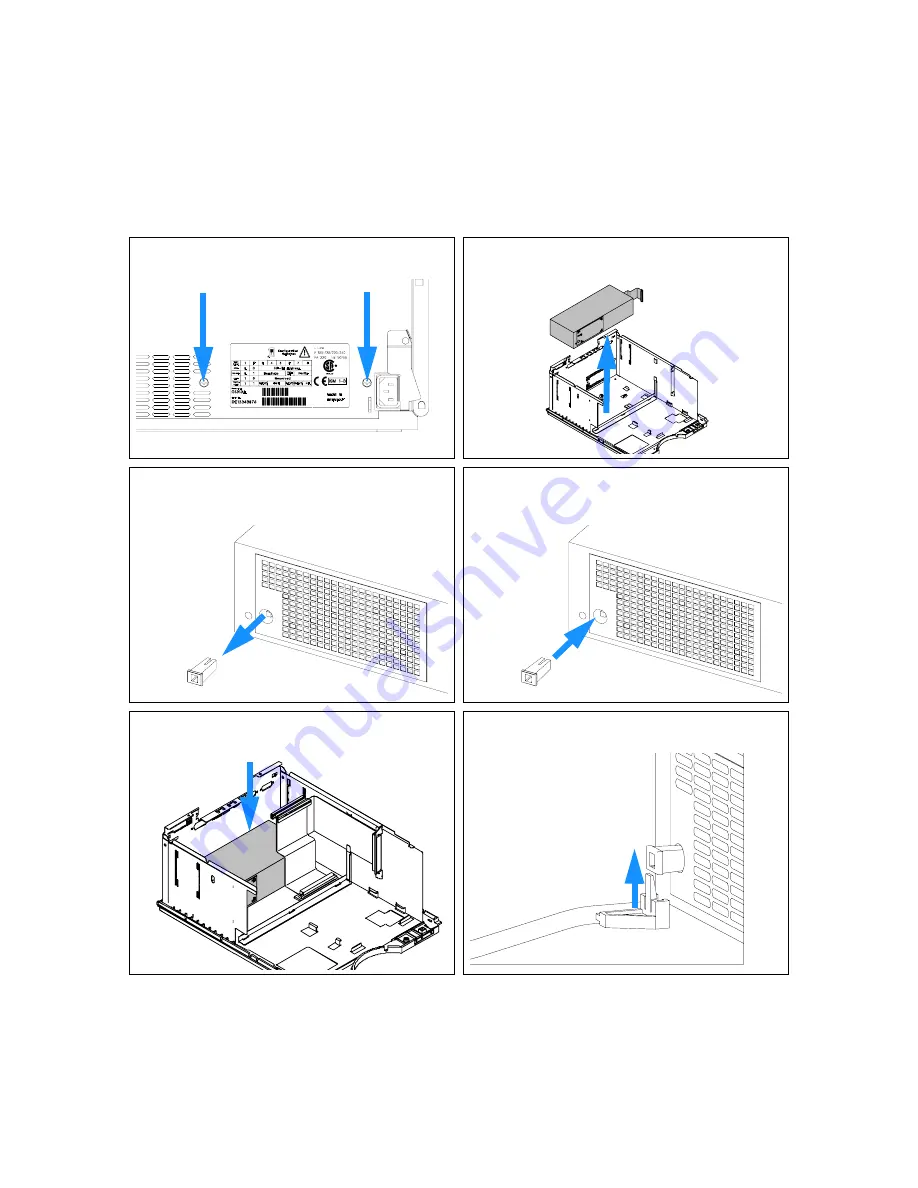
170
Agilent 1200 Series Autosampler Reference Manual
4
Repairing the Autosampler
3 Remove the two screws from the rear panel.
4 Lift the power supply out of the module.
5 Remove the coupler from the of the power supply.
6 Insert the coupler onto the switch of the new power
supply.
7 Install the power supply in the module.
8 Connect the light pipe to the coupler.
CellFrame
CellFrame
CellFrame
CellFrame
CellFrame
CellFrame
Summary of Contents for 1200 series
Page 1: ...A Agilent 1200 Series Standard and Preparative Autosamplers Reference Manual ...
Page 12: ...12 Agilent 1200 Series Autosampler Reference Manual Contents ...
Page 42: ...42 Agilent 1200 Series Autosampler Reference Manual 1 Installing the Autosampler ...
Page 104: ...104 Agilent 1200 Series Autosampler Reference Manual 3 Troubleshooting and Test Functions ...
Page 174: ...174 Agilent 1200 Series Autosampler Reference Manual 4 Repairing the Autosampler ...
Page 198: ...198 Agilent 1200 Series Autosampler Reference Manual 5 Parts and Materials ...
Page 232: ...232 Agilent 1200 Series Autosampler Reference Manual 7 Introduction to the Autosampler ...
Page 277: ......