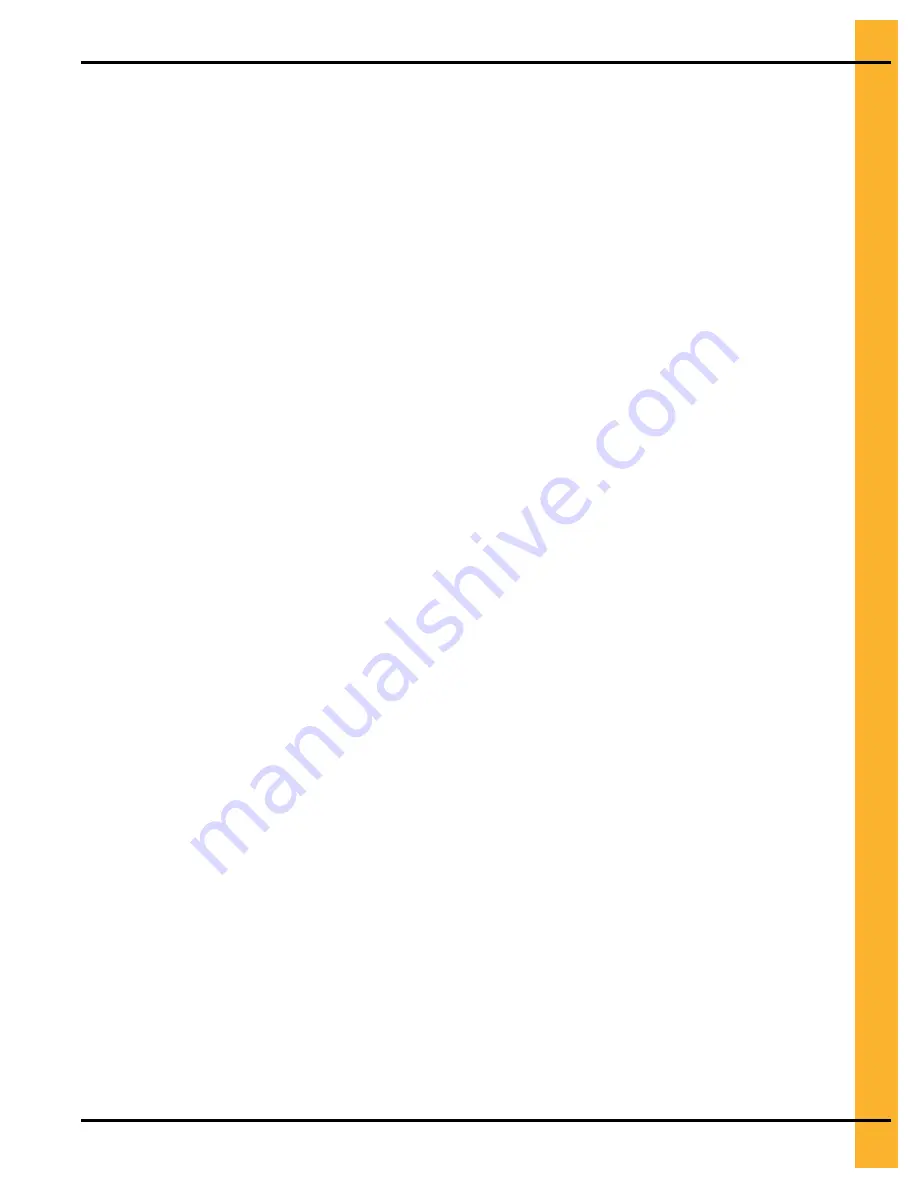
15.Install the outer door assembly to the outer door hinge weldments with bolts (S-1443) and nuts.
Adjust the hinges until the outer door opens and closes smoothly. Apply 1/2 x 1 in. foam seal strip to
the outer frame weldment to seal the outer door. Fill all unused bolt holes with 3/8 x 1 in. bin bolts
(S-7487).
16.After all parts are installed, tighten all hardware to the recommended torque specifications. See
Torque Specifications, page 22
.
17.Make sure the decals are installed on the inside and outside of the outer door. Please contact GSI
immediately if decals are missing or damaged.
18.Caulk as necessary at the top and bottom juncture of the door frame and the sidewall and
foundation.
Pneg-4460A
60 Ft Diameter 40-Series Bins
79