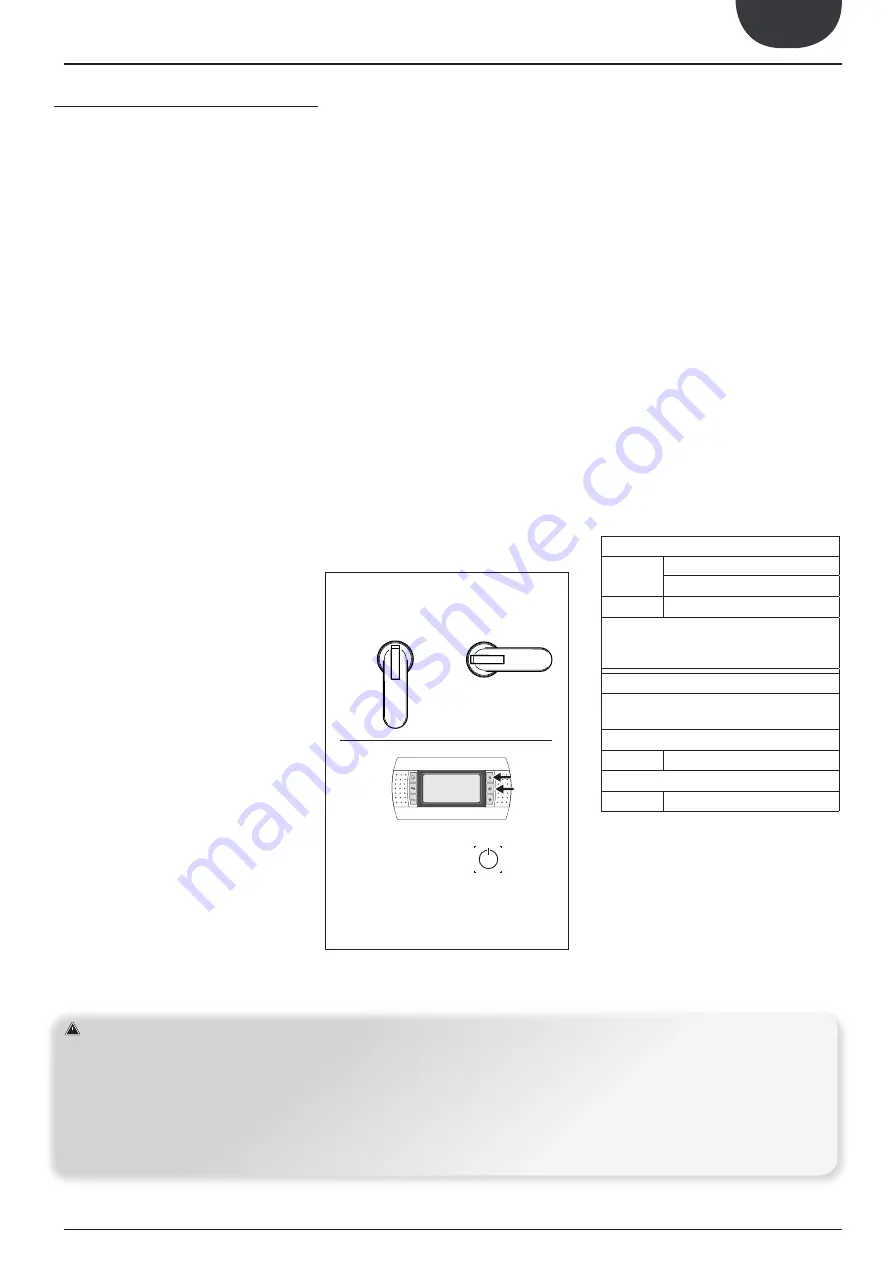
23
21.05 - 6068956_00
NXP 0500 - 1650 2-PIPE SYSTEM / 4-PIPE SYSTEM
EN
CONTROL AND COMMISSIONING
PREPARATION FOR COMMISSIONING
Please note that, on request by the Aermec customer or
the legiti mate owner of the machine, the units in this se-
ries can be started up by the AERMEC A� er-Sales Service
in your area (valid only on Italian territory).
The start of operati on must be scheduled in advance
based on the frame regarding the realisati on of the sys-
tem. Prior to the interventi on, all other works (electrical
and hydraulic connecti ons, priming and bleeding of air
from the system) must have been completed.
START - UP
PRELIMINARY OPERATIONS TO BE PERFOR-
MED WITH NO VOLTAGE PRESENT
Control:
1.
All safety conditi ons have been respected.
2.
The unit is correctly fi xed to the support
surface.
3.
The minimum technical spaces have been
respected.
4.
That the main power supply cables have
appropriate cross-secti on, which can support
the total absorpti on of the unit
(see electric
data secti ons)
and that the unit has been duly
connected to earth.
5.
That all the electrical connecti ons have been
made correctly and all the clamps adequately
ti ghtened.
THE FOLLOWING OPERATIONS ARE TO BE CAR-
RIED OUT WHEN THE UNIT IS LIVE.
1.
Supply power to the unit by turning the master
switch to the ON position; see (fig1.) The display
will switch on a few seconds after voltage has
been supplied; check that the operating status
is on OFF (OFF BY KEY B on lower side of the
display).
2.
Check with a tester that the value of the supply
voltage to the phases: single-phase – three-phase
is within the present limits: ±10% (230V ±10% -
400V ±10%), and that the unbalance between the
phases is not more than 3% (only for three-phase
models)
3.
Check that the connections made by the installer
are in compliance with the documentation.
4.
Verify that the compressor sump resistance/s
is/are operating by measuring the increase in
temperature of the oil pan. The resistance/s must
function for at least 12 hours before start-up of
the compressor and in any event, the tempera-
ture of the oil pan must be 10-15°C higher than
room temperature.
HYDRAULIC CIRCUIT
1.
Check that all hydraulic connections are made
correctly, that the plate indications are complied
with and that a mechanical filter has been
installed at the evaporator inlet
(mandatory
component for warranty to be valid).
2.
Make sure that the circulation pump/s is/are
operating and that the water flow rate is
sufficient to close the flow switch contact.
3.
Check the water flow rate, measuring the
pressure difference between evaporator inlet
and outlet and calculate the flow rate using the
evaporator pressure drop diagram present in
the technical manual
(available on the software
selection and on the website www.aermec.com
4.
Check correct operation of the flow meters, if
installed (or supplied with the unit or by the
installer – see the chapter of hydraulic circuit to
know the components supplied with the unit):
•
Flow switch/Pressure switch:
on closing the
cut-off valve at the heat exchanger outlet, the unit
must display the block. Finally, open the valve and
rearm the block.
MACHINE COMMISSIONING
The unit can be used a� er all of the above-menti oned
controls have been performed.
- Close the electric control board hatch.
- Positi on the appliance master switch at ON
- Starting the unit
WITH THE MACHINE ON, CHECK
COOLING CIRCUIT
CHECK:
- That the compressor input current is lower than the
maximum indicated in the technical data table.
- That in models with three-phase power supply, the
compressor noise level is not abnormal. If this is the
case, invert a phase.
- That the voltage value lies within the pre-fixed limits
and that unbalance between the three phases (three-
phase power supply) is not above 3%.
- The presence of any refrigerant GAS leaks, parti cu-
larly in correspondence with the manometers pres-
sure transducers and pressure switches pressure
points (vibrati ons during transportati on may have
loosened the fi � ngs).
- Overheating
Comparing the temperature read using a contact
thermostat positioned on the compressor intake with
the temperature shown on the low pressure manom-
eter (saturation temperature
corresponding to
the evaporation pressure). The difference between
these two temperatures gives the
over-
heating value. Optimal values are between 4 and 8°C.
- Pressing line temperature. If the subcooling and
overheating values are regular, the temperature
measured in the pressing line pipe at the outlet of
the compressor must be 30/40°C above the conden-
sation temperature.
Operati ng features (Factory set)
7°C / ∆t=5°C
Cooling Only
Heat Pump in Cooling Mode
45°C / ∆t=5°C Heat Pump in Heati ng Mode
If the unit power supply is restored a� er a tempo-
rary interrupti on, the mode set will be kept in the
memory.
Compressor Start-Up Delay
Two functi ons have been set-up to prevent com-
pressor start-ups that are too close.
Minimum time from last switch-off
60 seconds
in Cooling Mode
Minimum time from last switch-on
300 seconds
in Heati ng mode
ATTENTION
1)
Commissioning must be performed with standard settings.
Only when the inspection has been completed can the functio-
ning Set Point values by changed.
Before start-up, power the unit for at least 12-24 hours, posi-
tioning the protection magnet circuit breaker switch and the
door lock isolating switch at ON.
Make sure that the control panel is off in order to allow the
compressor oil sump to heat.
2)
We recommend to envision a machine book (not
supplied, but the user’s responsibility), which allows to keep
track of the interventions performed on the unit.
In this way it will be easy to suitably organise the interventions
making research and the prevention of any
machine breakdowns easier. Use the date to record date, type
of intervention made (routine maintenance, inspection or re-
pairs), description of the intervention,
measures actuated.
3)
It is forbidden to LOAD the cooling circuit with a refrigerant
different to that indicated. Using a different refrigerant gas can
cause serious damage to the unit.
ON
ON
OFF
OFF
SELECT MENÙ
ON/OFF
16. CONTROL AND COMMISSIONING