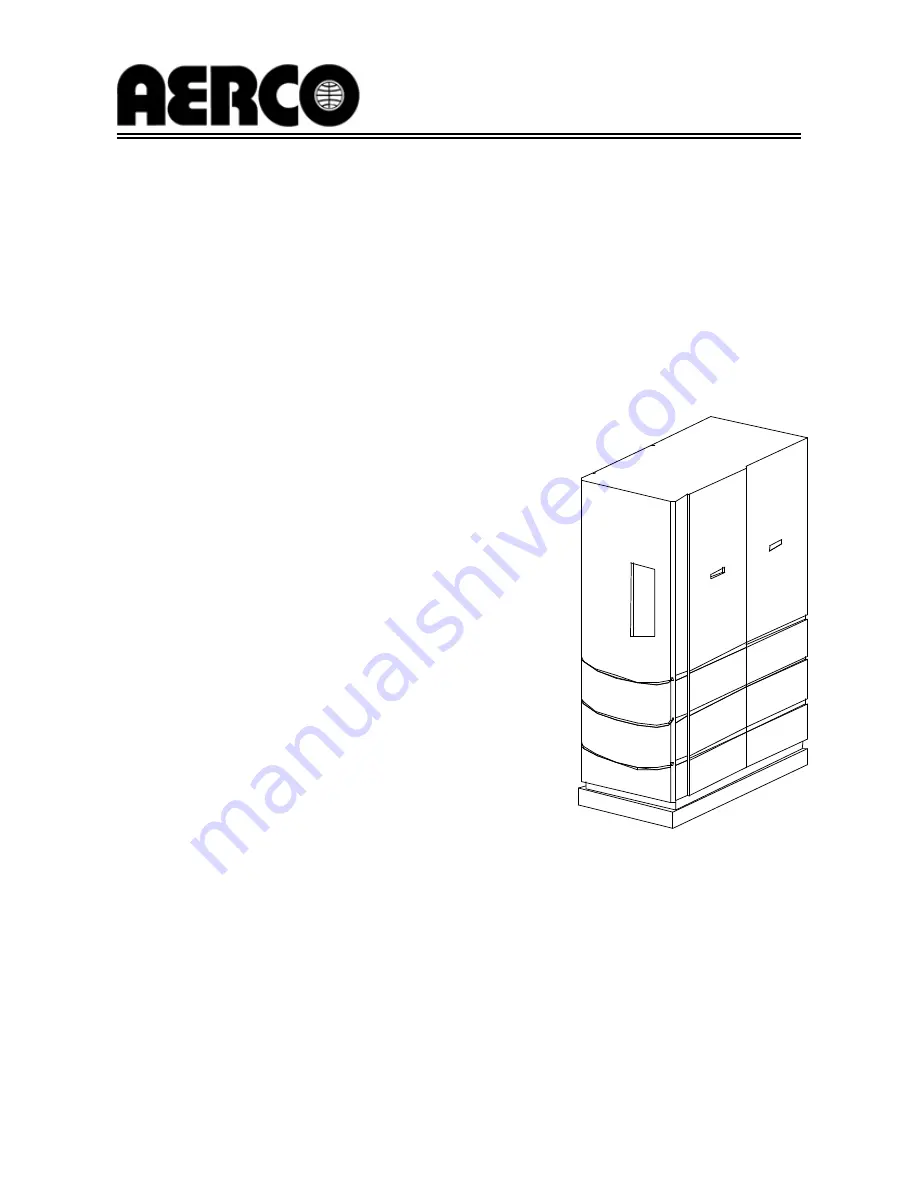
Printed in U.S.A.
REVISED JANUARY, 2009
GF-110
Instruction
No.
AERCO INTERNATIONAL, Inc., Northvale, New Jersey, 07647 USA
Installation, Operation
& Maintenance Instructions
Benchmark
™
Series
Gas Fired
Boiler System
Condensing, Modulating
Forced Draft, Hot Water Boiler
2,000,000 BTU/H Input
Applicable for Serial Numbers G-02-533 and above
Patent # : 2.155.12
Summary of Contents for GF-110 Benchmark Series
Page 6: ......
Page 8: ......
Page 12: ......
Page 32: ......
Page 40: ......
Page 46: ......
Page 52: ......
Page 58: ......
Page 68: ......
Page 76: ......
Page 77: ...APPENDIX C C 1 Temperature Sensor Resistance Chart Balco ...
Page 78: ......
Page 84: ......
Page 85: ......
Page 86: ......
Page 87: ......
Page 88: ...APPENDIX F F 4 ...
Page 89: ...APPENDIX F F 5 ...
Page 90: ......
Page 91: ......
Page 92: ......
Page 93: ...APPENDIX F F 9 ...
Page 94: ...APPENDIX F F 10 ...
Page 95: ......
Page 96: ......
Page 97: ......
Page 98: ......
Page 99: ...APPENDIX G G 5 ...
Page 100: ......
Page 101: ...APPENDIX H H 1 ...
Page 102: ...APPENDIX H H 2 ...
Page 104: ...APPENDIX H H 4 ...
Page 105: ...APPENDIX H H 5 ...
Page 106: ...APPENDIX H H 6 ...
Page 108: ......
Page 110: ...APPENDIX J J 2 P1 P2 P3 P4 P5 P6 BENCHMARK CONTROL PANEL REAR VIEW ...
Page 112: ...APPENDIX K K 2 FIGURE 1 DUAL FUEL DIVERTER VALVE FIGURE 2 DUAL FUEL AIR INJECTION VALVE ...
Page 115: ......
Page 116: ......