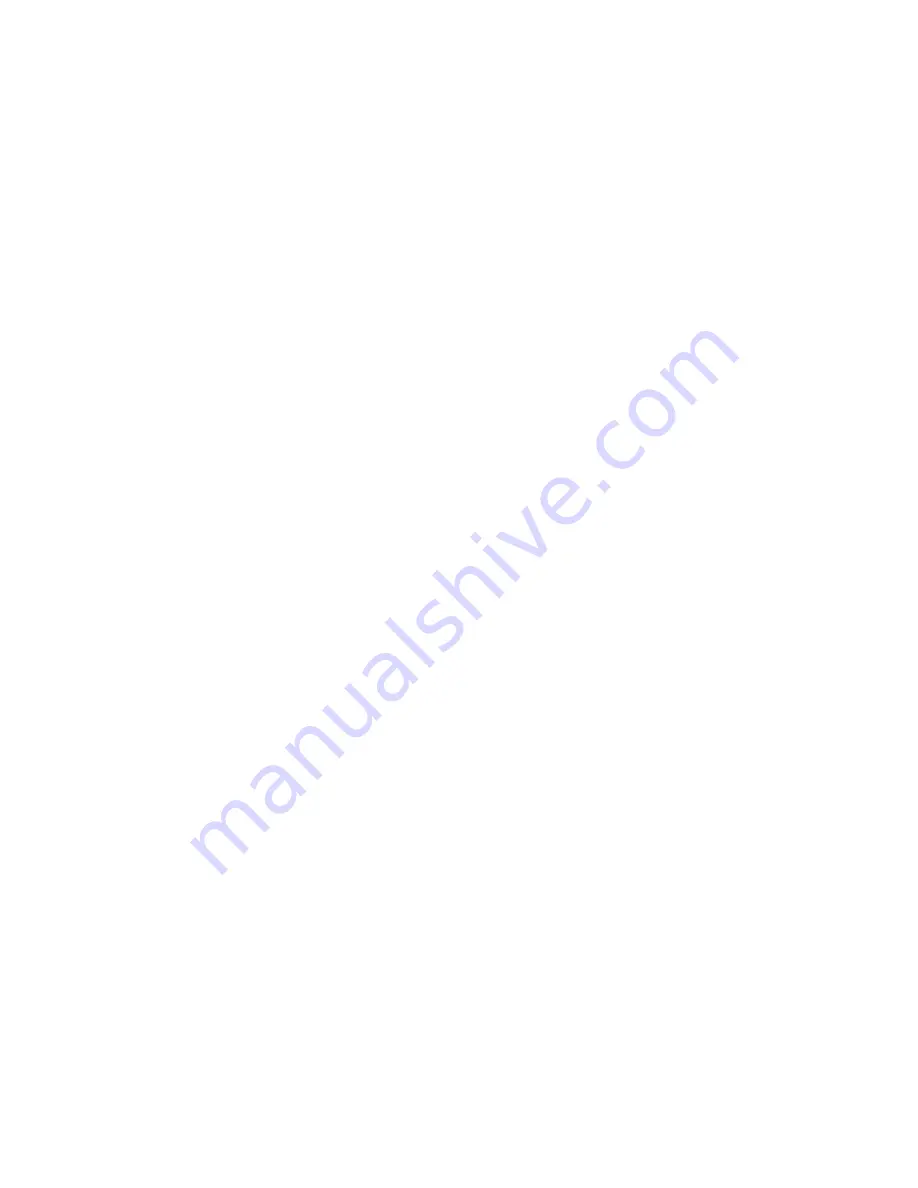
V6.230 20131017
105
interface capable of supporting multi-drop topologies. RS-485 interfaces differ
from RS-232 in that RS-485 uses a differential receiver and transmitter pair. This
permits RS-485 links to send and receive data over much greater distances as
long as some simple rules are followed. See Sections 3.7.3, 3.7.4, and 3.10 for
connections, jumper settings, and shield grounding.
After making the proper connections to the TTC-1000, there are only two settings
that need to be made: Node Address and Baud Rate. Node Addresses for
DNP3.0 can be any number from 0 to 65535. For MODBUS the addresses are
1-247, 0 is for broadcast and remaining 248-255 are reserved. Please consult
the DNP3.0 or MODBUS reference materials as some higher order addresses
are reserved for broadcast messages.
Baud Rates can be set to either 1200, 2400, 9600 or 19200. It is recommended
that both Node Address and Baud Rate settings be made before attempting to
communicate, however these settings can be changed “on-the-fly” without
powering down the TTC-1000. In the TTC-1000, the MODBUS RTU interface is
configured using 8 data bits, 2 stop bits, and no parity. The DNP3.0 interface is
configured using 8 data bits, 1 stop bit, and no parity.
The TTC-1000 implements DNP3.0 Level 1 communications. This includes Class
0 polls (Object 60 Variation 1) of analog and binary output points. The TTC-1000
supports Object 1 Variation 2 binary outputs. Binary outputs include all
temperature and load set points along with the state of each output relay.
Because Variation 2 is supported, the TTC-1000 communicates whether or not
an output relay is under manual control by exerting the “forced” status bit for
these points only. The “forced” status bit is located in bit 4 of each binary output
octet transmitted to the Master. For Analog Outputs, the TTC-1000 supports
Object 30 Variation 4. These are 16 bit signed analog quantities without status.
Included in the Analog Output points are all temperatures equipped plus load
data if available. Also, the TTC-1000 uses two points to identify whether or not
the probe is measuring Top Oil, Heated Well, LTC Differential or Ambient
temperature. This is particularly useful for dual probe units. It is noted that Object
1 Variation 2 and Object 30 Variation 4 points cannot be read individually and
can only be read by a Class 0 poll.
In addition, the TTC-1000 supports the remote control of the four output relays.
The TTC-1000 supports both direct control (Object 10 Variation 0) and Select
Before Operate control (Object 12 Variation 1). The TTC-1000 permits the user
to command an output relay to pickup. It cannot be used to dropout an output
relay. If the Binary Input point is turned off, it merely returns the device to local
automatic control. Once the unit accepts the remote control command, the
“remote forced” bit will become a logic “1”. The “remote forced” bit will remain a
logic “1” until that point is dropped out by the DNP Master.
Remote control can be blocked through the use of the REMOTE BLK setting.
Enabling this setting will prevent all output points from picking up through remote
control. Also, enabling the REMOTE BLK setting after an output has been
commanded to remotely pickup but before remote control is returned to local
Summary of Contents for TTC-1000
Page 11: ...Warranty V6 230 20131017 x PAGE INTENTIONALLY BLANK ...
Page 41: ...V6 230 20131017 30 THIS PAGE INTENTIONALLY LEFT BLANK ...
Page 121: ...V6 230 20131017 110 PAGE INTENTIONALLY BLANK ...
Page 133: ...V6 230 20131017 122 PAGE INTENTIONALLY BLANK ...
Page 153: ...V6 230 20131017 142 PAGE INTENTIONALLY BLANK ...
Page 157: ...V6 230 20131017 146 PAGE INTENTIONALLY BLANK ...
Page 199: ...V6 230 20131017 188 PAGE INTENTIONALLY BLANK ...
Page 247: ...V6 230 20131017 236 PAGE INTENTIONALLY LEFT BLANK ...