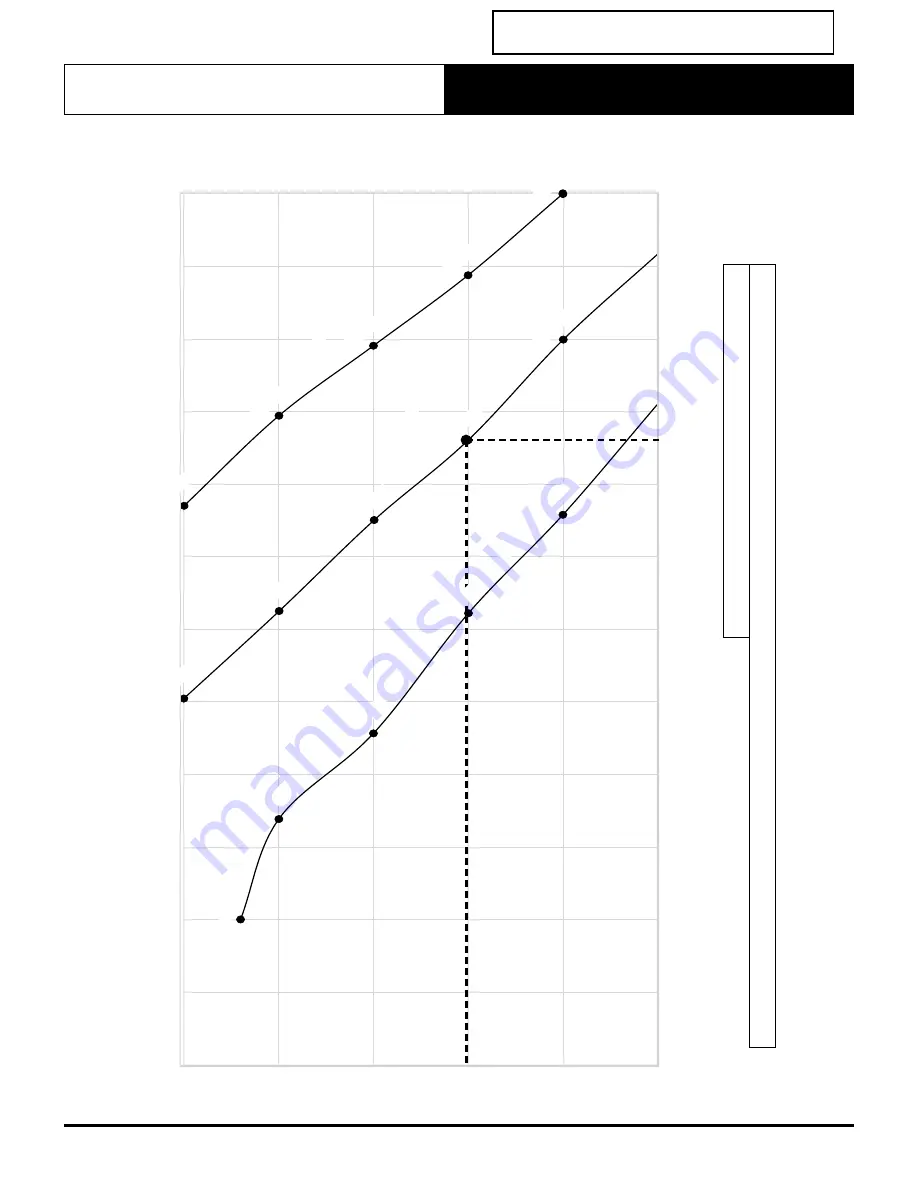
Installation and Commissioning Guide
Advance Outdoor Units
Installation and Commissioning Guide - Advance Split Ducted Outdoor Unit
Doc. No.0525-085 Ver. 2 22xxxx
43
PRELIMINARY DATA ONLY
Ver. 2.04 220704
THIS LABEL TO BE REMOVED ON SIGN-OFF
EVV140S / EFV140S : Three Speed Application Fan Curve
EXTERNAL STA
TIC PRESSURE (P
a)
F
an
F
an
F
an
Low
Med
High
0
0.86
1.27
1.68
50
1.02
1.45
1.89
100
1.17
1.62
2.09
150
1.31
1.79
2.28
200
1.44
1.96
2.49
220
1.26
250
2.11
2.68
0
50
100
150
200
250
200
25
0
30
0
350
40
0
45
0
500
550
60
0
650
700
75
0
80
0
Lo
w
Sp
eed
M
edi
um
Spee
d
Hi
gh
Spe
ed
1.
02 A
1.44 A
1.31 A
1.
26 A
2.28 A
1.45 A
2.09 A
Nominal Air
flow = 6
30 I/
s
4
7% PW
M
AIRFL
O
W (l
/s)
1.79 A
1.9
6 A
2.11 A
2.49
A
2.68 A
1.1
7 A
1.89 A
1.6
2 A
0
50
100
150
200
250
220
60% PW
M
35
% PW
M
250
300
350
400
450
500
550
600
650
70
0
75
0
800
Hi-
Mid-L
ow Sp
ee
d Air
flow Range
V
ariable F
an T
echnolo
gy Air
flow Range
200