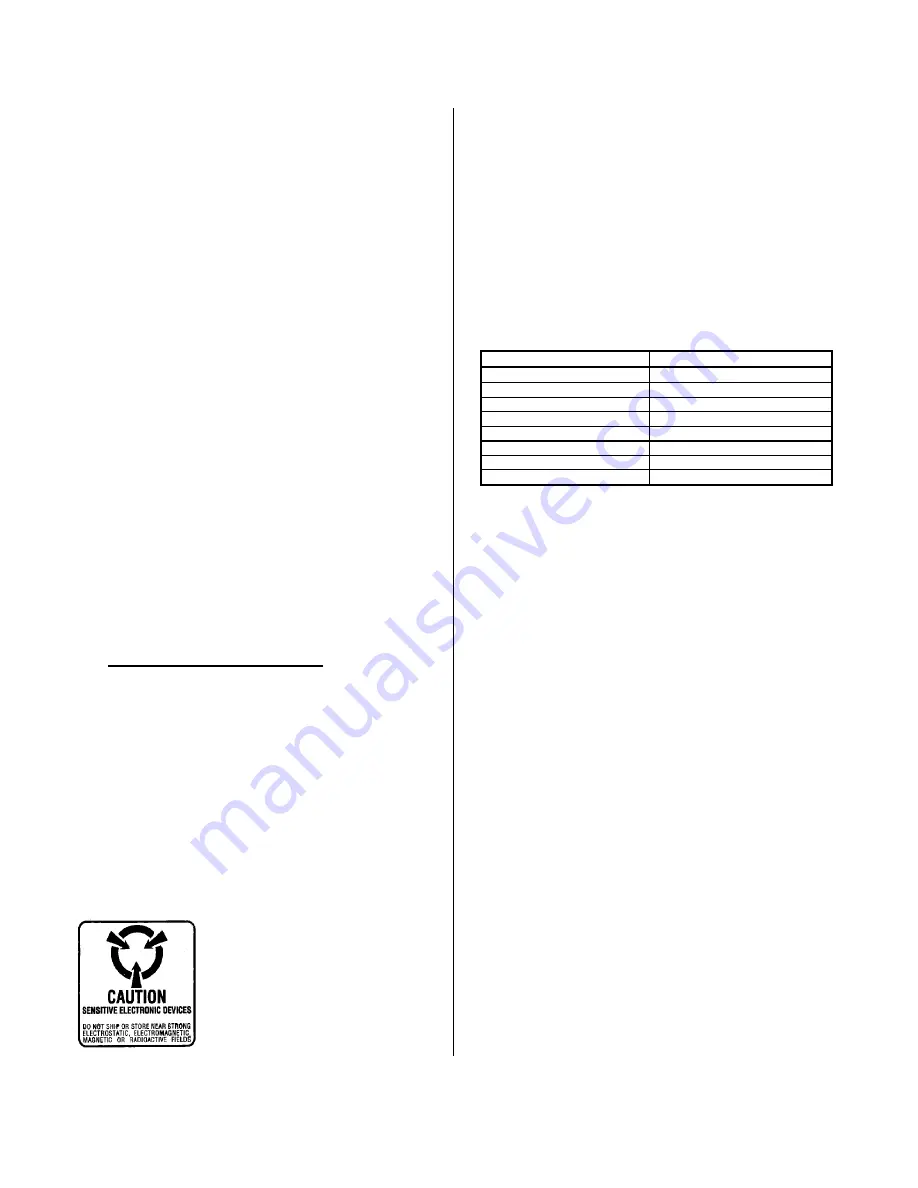
BusWorks
Model 903MB/902MB/901MB Network I/O Module User’s Manual Digital I/O
___________________________________________________________________________________________
- 4 -
RS-232 to RS-485 Serial Adapter (Model 5034-214)
This device is a non-isolated, port-powered, signal converter
for communication between the RS-232 serial port of a personal
computer and the RS-485 network interface of Series 900MB I/O
Modules. It is used in conjunction with the Acromag
Configuration Software for simple reconfiguration, testing, and
troubleshooting of Series 900MB I/O modules. As a port-
powered device, it is not intended for driving fully loaded RS-485
networks over long distances, and does not have sufficient power
to drive terminated networks. The adapter has DB-9F connectors
at both ends and plugs directly into the common DB-9M serial
port connector of most personal computers. The module is
connected to the RS-485 side of this adapter via a separate
interconnecting cable (see Cable 5034-202 described below).
Interface Cable (Model 5034-202)
This 3-wire cable is used to connect the RS-485 side of
Signal Converter 5034-214 to the RS-485 network terminals of
Series 900MB modules. This cable is 8 feet long and has a
DE-9M connector on one end, and three stripped and tinned
wires on the other end. The wires are labeled A, B, and C for
connection to the module D, Dbar, and COM terminals,
respectively.
Series 900MB Software Interface Package (Model 900C-SIP)
The 900C-SIP Software Interface Package combines the
900MB Configuration Software (5034-186), RS-232 to RS-485
Serial Converter (5034-214), Interface Cable (5034-202), and
Instructions (8500-649), into a complete kit for interfacing with
Series 900MB I/O Modules.
2.0 PREPARATION FOR USE
UNPACKING AND INSPECTION
Upon receipt of this product, inspect the shipping carton for
evidence of mishandling during transit. If the shipping carton is
badly damaged or water stained, request that the carrier's agent
be present when the carton is opened. If the carrier's agent is
absent when the carton is opened and the contents of the carton
are damaged, keep the carton and packing material for the
agent's inspection. For repairs to a product damaged in
shipment, refer to the Acromag Service Policy to obtain return
instructions. It is suggested that salvageable shipping cartons
and packing material be saved for future use in the event the
product must be shipped.
This module is physically protected
with packing material and electrically
protected with an anti-static bag during
shipment. However, it is
recommended that the module be
visually inspected for evidence of
mishandling prior to applying power.
This circuit utilizes static sensitive
components and should only be
handled at a static-safe workstation.
MODULE INSTALLATION
This transmitter module is packaged in a general purpose
plastic enclosure. Use an auxiliary enclosure to protect the unit in
unfavorable environments or vulnerable locations, or to maintain
conformance to applicable safety standards. Stay within the
specified operating temperature range. As shipped from the
factory, the unit is calibrated for all valid input ranges and has the
default configuration shown in Table 2 below:
WARNING:
Applicable IEC Safety Standards may require that
this device be mounted within an approved metal enclosure or
sub-system, particularly for applications with exposure to voltages
greater than or equal to 75VDC or 50VAC.
Table 2: 903MB Default Factory Configuration
PARAMETER
CONFIGURATION
Module Address
247
Baud Rate
9600bps
Parity
None
Stop Bits
1 or 2 (When Parity = None)
Response Delay
0 (No Additional Delay)
Watchdog Time (Each Port)
0 (Disabled)
Timeout State (Each Port)
65535 (FFFFH) = No Change
Pullup Resistor To EXC+
5.6K Installed (In Sockets)
Note:
Do not confuse the Default Factory Configuration noted
above with the Default Communication Mode, which refers to the
fixed baud rate, module address, parity, and stop bit settings
achieved by pushing the Default Mode button until the status LED
flashes ON/OFF. The Default Communication Mode will
temporarily over-ride any factory configuration of baud rate,
module address, parity, and stop bits with settings of 9600bps,
247, None, and 1 or 2, respectively. It is provided as a
convenient means of achieving communication with a module
when these parameters are unknown.
Your application will typically differ from the default factory
configuration and will require that the transmitter be reconfigured
to suit your needs. This can be easily accomplished with
Acromag’s user-friendly Windows 95/98
or NT
900MB
Configuration Program. Configuration is normally done prior to
field installation. Refer to MODULE SOFTWARE
CONFIGURATION of Section 3.0 for detailed instructions.
Default Mode Switch
A push-button default mode switch (DFT) and status LED are
provided at the front of the module as a convenient way of
communicating with the module when its baud rate and address
settings are unknown. Push & hold this button until the Status
LED flashes ON/OFF to indicate the module is in the Default
Communication Mode with a fixed module address of 247, baud
rate of 9600bps, no parity, and 1 or 2 stop bits. It is most
convenient to configure a module in this mode, then leave the
default mode by pressing this button again until the Status LED
stops flashing (constant ON or OFF), or by resetting the module.
Note that a rapidly flashing Status LED indicates a watchdog
timer timeout has occurred and this may temporarily mask default
mode indication. The Default Mode is disabled following a
software or power-on reset. New communication parameters (for
baud rate, address, and parity) will take effect following a reset of
the module and the module will leave the Default Mode.