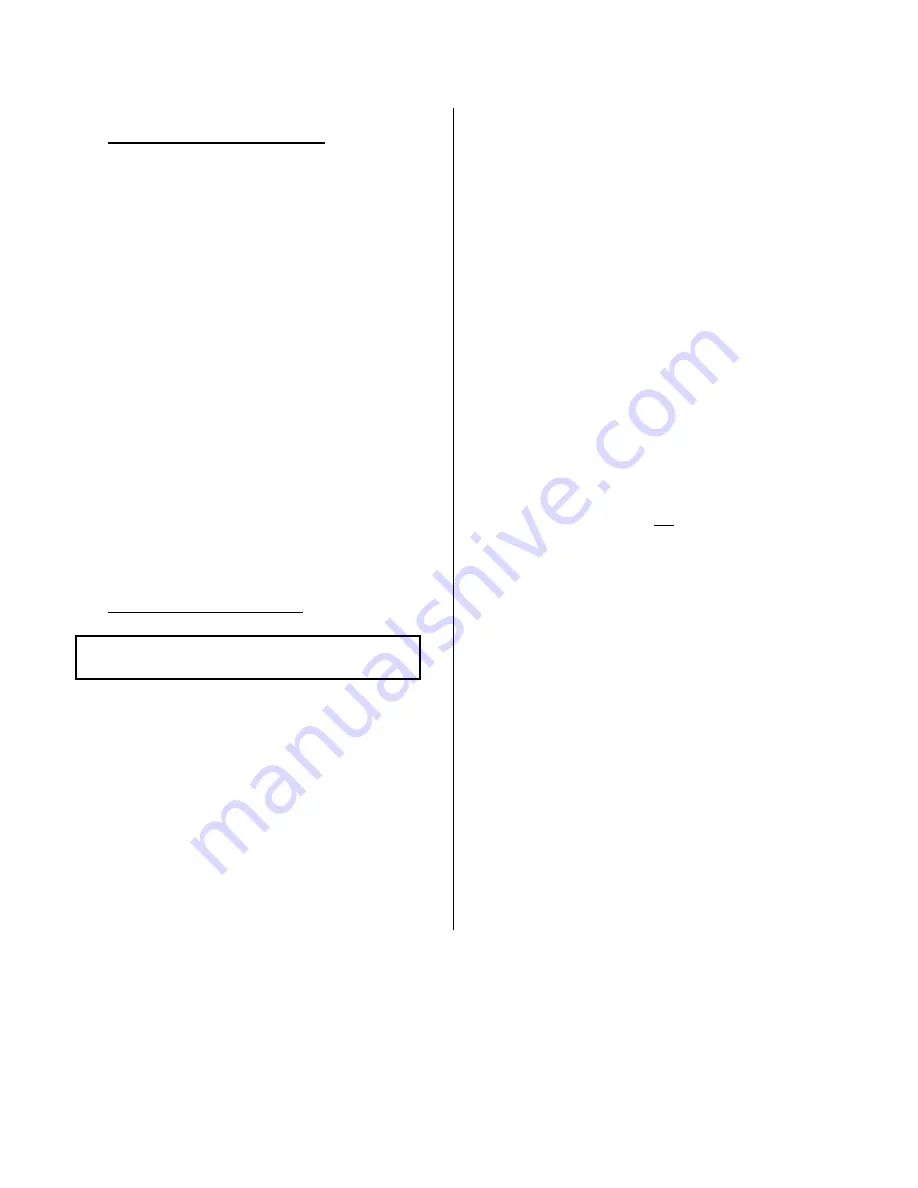
BusWorks
Model 903MB/902MB/901MB Network I/O Module User’s Manual Digital I/O
___________________________________________________________________________________________
- 19 -
4.0 THEORY OF OPERATION
Refer to Simplified Schematic 4501-809 and Functional Block
Diagram 4501-810 to gain a better understanding of the circuit.
Note that these modules will interface with any mix of up to
twelve digital input or output signals according to the model, and
provide network commands to configure the module, monitor the
inputs, and control the outputs. The outputs are the open-drains
of n-channel mosfets. Input buffers are connected in tandem with
the drain circuits via series 100K
Ω
resistors. Over-voltage
clamps to +5V are connected to the buffer inputs. I/O terminals
also include transient suppression. Sockets are installed for
installation of optional input or output drain pullup resistors.
These resistors are pulled up to an external supply connected to
the EXC+ and RTN terminals. The microcontroller completes the
information transfer according to the I/O type and its embedded
program. I/O lines of the microcontroller switch the outputs
ON/OFF, and sample the digital inputs, as required. The UART
of the microcontroller sends/receives its I/O signals to the
network via an optically isolated RS485 transceiver. Embedded
configuration parameters are stored in non-volatile memory
integrated within the micro-controller. Only the functions required
by an application are actually stored in memory—new
functionality can be downloaded via the host running the Modbus
Configuration Software, or other compatible Modbus software
along the network. A wide input switching regulator (isolated
flyback) provides isolated power to the I/O circuit and RS485 port.
Refer to Functional Block Diagram 4501-810 for an overview of
how the software configuration variables are arranged.
5.0 SERVICE AND REPAIR
CAUTION:
Risk of Electric Shock - More than one
disconnect switch may be required to de-energize the
equipment before servicing.
SERVICE AND REPAIR ASSISTANCE
This module contains solid-state components and requires no
maintenance, except for periodic cleaning and transmitter
configuration parameter verification. Since Surface Mounted
Technology (SMT) boards are generally difficult to repair, it is
highly recommended that a non-functioning module be returned
to Acromag for repair. The board can be damaged unless special
SMT repair and service tools are used. Further, Acromag has
automated test equipment that thoroughly checks and calibrates
the performance of each module. Please refer to Acromag’s
Service Policy Bulletin or contact Acromag for complete details
on how to obtain service parts and repair.
PRELIMINARY SERVICE PROCEDURE
Before beginning repair, be sure that all installation and
configuration procedures have been followed. Make sure that the
correct baud rate is selected for the RS232-to-RS485 converter
employed The unit routinely performs internal diagnostics
following power-up or reset. During this period the green “Run”
LED flashes. If the diagnostics complete successfully, the “Run”
LED will stop flashing after two seconds and remain ON. This
indicates that the unit is operating normally. If the “Run” LED
continues to flash, then this is indicative of a problem. In this
case, use the Acromag Modbus Configuration Software to
reconfigure the module and this will usually cure the problem. If
the diagnostics continue to indicate a problem (a continuously
flashing green LED), or if other evidence points to a problem with
the unit, an effective and convenient fault diagnosis method is to
exchange the questionable module with a known good unit.
Acromag’s Application Engineers can provide further
technical assistance if required. When needed, complete repair
services are available from Acromag.
TROUBLESHOOTING
If you fail to communicate with the Model 903MB…
1.
Is power ON at the module and the RS485 signal converter
(Green power LED continuously ON)?
2.
Have you set the correct baud rate at the RS485 converter
(and/or repeater if used)? Is your host set to the proper
baud rate and parity? Are you using the correct address?
3.
Have you tried communicating using the Default
Communication Mode? Press the “DFT” push-button of the
903MB module until the yellow status LED is flashing. This
sets the module’s communication parameters to 9600 baud,
a slave address of 247, no parity, and two stop bits. Be sure
to also set the baud rate of your RS485 converter and/or
repeater to 9600 baud.
4.
Has the module been reset? The module will automatically
leave the Default Communication Mode following a software
or power-on reset and new settings for address, baud rate,
and parity will take effect following reset. If the yellow status
LED is not blinking or OFF, the module is no longer in the
Default Mode. Be sure to make host/software adjustments
to the baud, parity, and address parameters following a
reset of the module, as required to maintain communication.
5.
If you fail to communicate with the module or have a high
degree of communication errors, try increasing the response
delay time (See Response Delay Register 40010). Some
network converters or host/software systems cannot accept
an immediate response from a slave device without
additional delay inserted between message receipt and
module response.