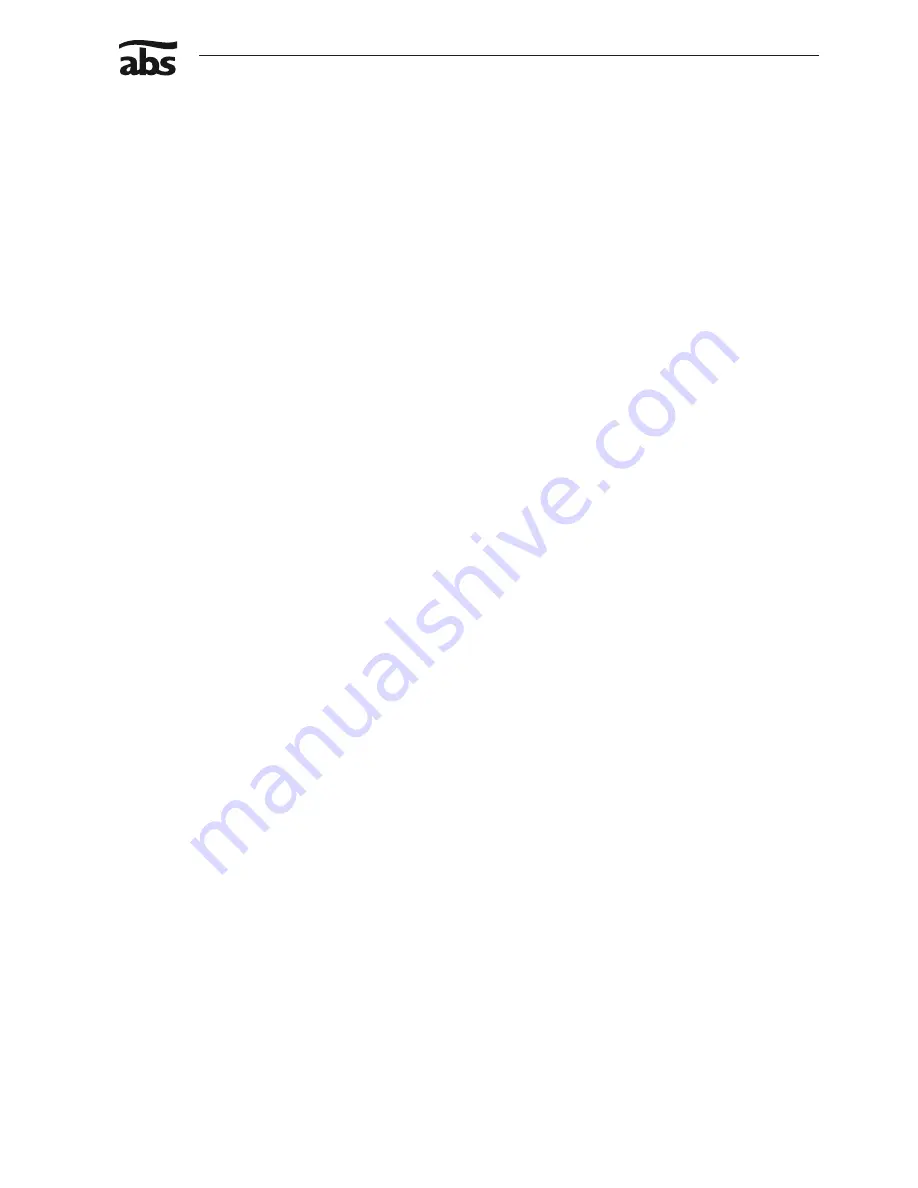
������������ ���� ���������� ������������
5
ABS lifting station Sanimat
1.5
D����������
The flood-proof sewage lifting station Sanimat 1501S to 3702S are made up of a gas and odour-tight synthetic
collection tank complying with DIN 19760 and 12050-1 with either 1 or 2 submersible sewage pumps, together
with a control unit and level control system. The collection tank is fitted with a number of inflow ports. The unit
is supplied from the factory with all inlet ports closed off. The inlet ports of dimensions DN 100/150 and 200 are
located at various heights and can be opened up as required.
Depending on the size of the sewage lifting station, submersible pumps of the types AS S17/2 and S26/2 as
well as pumps from the AFP series M15/4 to M60/4 can be supplied. All motors comply with Insulation Class F
(155 °C) and Protection Type IP 68. The motor shaft is supported in lubricated-for-life ball bearings. The shaft
sealing on the motor side is carried out by a lip seal, while sealing at the liquid side is carried out by means of a
high quality silicon carbide mechanical seal. The submersible pumps M15/4 to M60/4 have been supplied with
thermal sensors in the stator which switch off the motors in the event of overheating, together with a Dl-system
of moisture protection for the monitoring of the mechanical seal.
The hydraulic section is supplied with ContraBlock system, and spiral bottom plate with waved shearing inlet,
open ABS channel type impeller and volute. All hydraulic parts have been manufactured from Cast Iron (GG
25).
The sewage entering by the inlet port is collected in the odour-tight collection tank.
When a predetermined liquid level is reached, then the automatic level control system switches on the
submersible pump and switches it off again when the tank is empty.
In the case of twin pumping stations the starting sequence of pumps is reversed at each starting operation. If
level 2 is reached, then both submersible pumps work in parallel.
The automatic level control system functions as an electro-pneumatic control system based on the forced air
bubbling principle, by which compressed air is continually pumped via the submerged tube into the liquid in the
collection tank. The counter pressure caused by this is dependent on the liquid level present and operates a
membrane switch in the control system by means of the control line (plastic hose).
Units supplied with one pump can be retrofitted with a second pump.
S�f��y
The general and specific health and safety hints are described in detail in the separate booklet Safety Hints. If
anything is not clear or you have any questions as to safety make certain to contact the manufacturer ABS.
3
T��������
m
During transport the unit should not be dropped or thrown.
c
The unit should never be raised or lowered by the Power cable.
m
Any hoist used must be adequately dimensioned for the weight of the unit.
All relevant safety regulators as well as general good technical practice must be complied with.