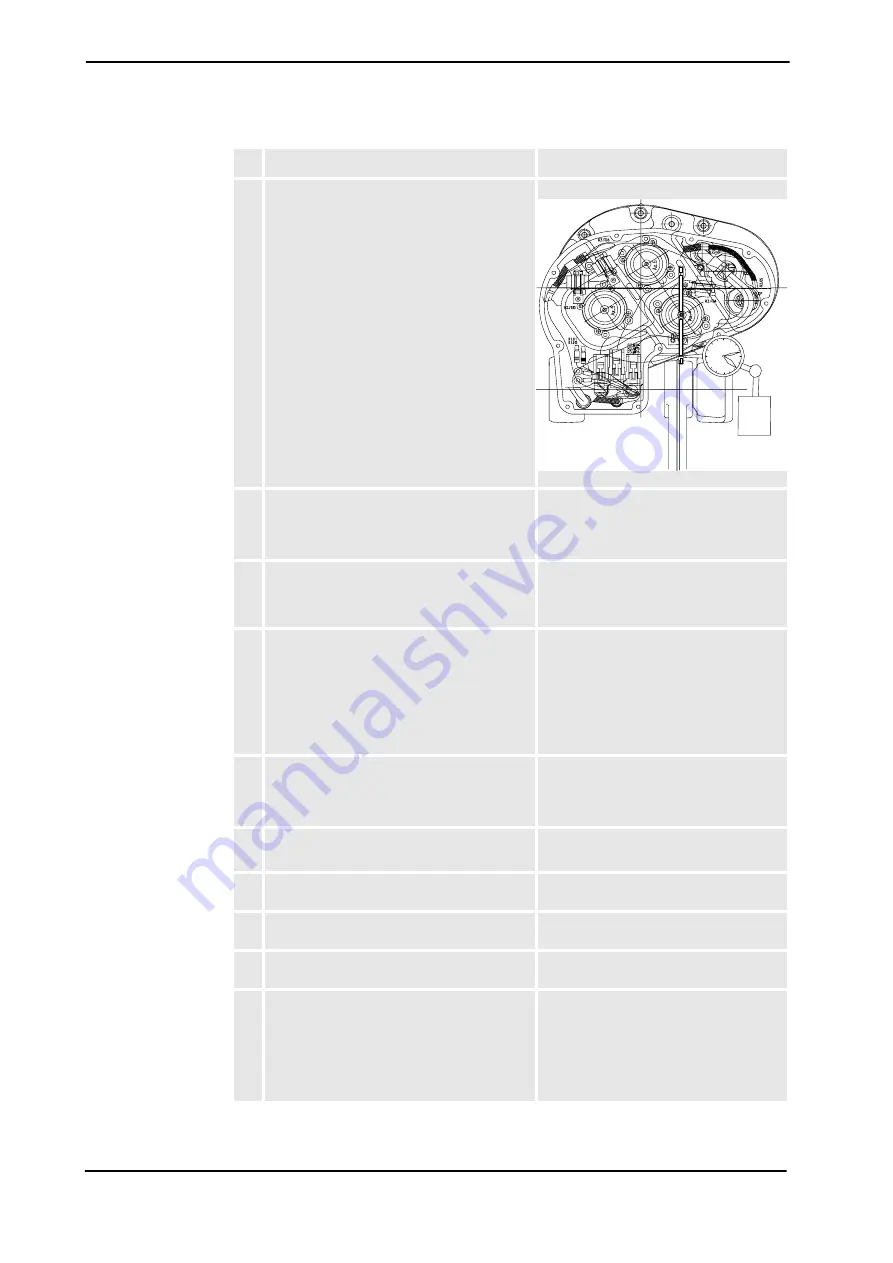
4 Repair
4.7.4. Replacement of motors, axes 4-6, IRB 2400L
3HAC022031-001 Revision: C
140
©
Co
py
rig
h
t 200
4-
200
8 ABB. All righ
ts reser
v
ed.
5. Fit the
measuring tool
at the rear of the
motor.
xx0300000005
6. The motor’s fixing screws shall be fastened,
but do not tighten them, to ensure that the
motor will be able to move parallel to the
gear when the adjustment is done
7. In order to release the brakes, connect the
24 VDC power supply to the motor.
Connect to connector R3.MP4:
•
+ : pin 7
•
- : pin 8
8. Start with a play in all positions and then
locate the smallest play by turning the motor
shaft six turns and thereby finding the area
with the smallest play within this range.
Use swift movements to avoid noticing the
magnetic field, which makes the gears stick
together.
9. Push or tap the motor in radial direction so
that the play becomes minimal within one
motor turn, without the gear “chewing”.
Do
not use force!
10. Tighten the motor attachment screws and
secure them with locking fluid.
4.1 Nm
Loctite 243
11. Perform a leak-down test.
Detailed in section
.
12. Refill the axis 4 gearbox with
lubricating oil
.
Art. no. and amount is specified in
Required equipment on page 137
.
13. Reconnect the cabling.
Detailed in section
14. Recalibrate the robot.
Calibration is detailed in a separate
calibration manual, enclosed with the
calibration tools.
General calibration information is
included in section
Action
Note/Illustration
Continued
Continues on next page
Summary of Contents for IRB 2400/L
Page 1: ...Product manual Articulated robot IRB 2400 L IRB 2400 10 IRB 2400 16 M2000 M2000A M2004 ...
Page 2: ......
Page 8: ...Table of Contents 6 3HAC022031 001 Revision C Copyright 2004 2008 ABB All rights reserved ...
Page 191: ......
Page 192: ......
Page 193: ......
Page 194: ......
Page 195: ......
Page 198: ......
Page 199: ......
Page 202: ......
Page 203: ......
Page 205: ......
Page 226: ......