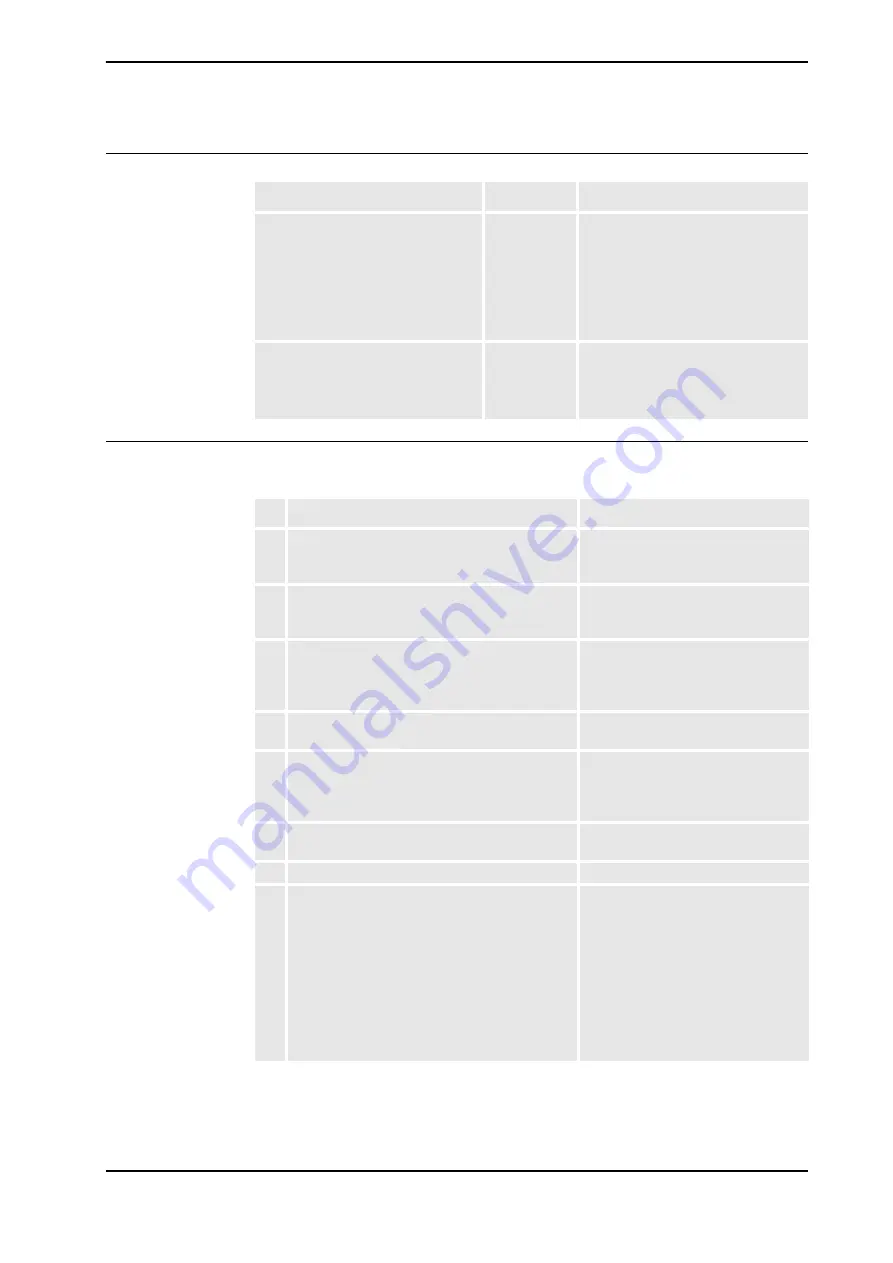
2 Installation and commissioning
2.4.2. Mechanically restricting the working range of axis 1
53
3HAC022031-001 Revision: C
©
Co
py
rig
h
t 200
4-
200
8 ABB. All righ
ts reser
v
ed.
Required equipment
Fitting, mechanical stop axis 1
The procedure below details how to fit a mechanical stop to the robot base.
Equipment
Art. no.
Note
Stop, axis 1
3HAB 7298-1
Includes:
•
removable stop (2 pcs)
•
plain washers (4 pcs)
•
hex socket head cap screw (4
pcs, M12x30)
•
drill template (1 pc)
User’s guide - S4Cplus (RobotWare
4.0)
Technical reference manual - System
parameters (RobotWare 5.0)
-
Art. no. is specified in section
Action
Note
1. Decide where to fit the extra mechanical stops,
according to the figure
holes for extra stops on page 54
2. Make a copy of the drill template, enclosed with
the mechanical stop.
The template is also shown in the
figure
in
scale 1:1.
3. Use the template to mark the center of the two
holes on each stop.
Place the template edge edge with
the robot base, as shown in the figure
Location of where to drill holes for
extra stops on page 54
4. Drill the holes through, Ø 10.2. Cut threads,
M12.
5. Fit the stops to the robot base, but without
tightening the screws.
Note!
The stops must be mounted in
correct direction, as shown in the
figure
Location of where to drill holes
.
6. Turn axis 1 manually and check the working
range between the stops.
If necessary; correct the angle of
impact.
7. Tighten the screws.
8. The software working range limitations must be
re-defined to correspond to the changes in the
mechanical limitations of the working range.
How to define the range of movement
in RobotWare 4.0 is detailed in
User’s
guide - S4Cplus, chapter System
Parameters - topic Manipulator
.
The system parameters that must be
changed in RobotWare 5.0 (Upper
joint bound and Lower joint bound)
are further detailed in
Technical
reference manual - System
parameters
.
Continued
Continues on next page
Summary of Contents for IRB 2400/L
Page 1: ...Product manual Articulated robot IRB 2400 L IRB 2400 10 IRB 2400 16 M2000 M2000A M2004 ...
Page 2: ......
Page 8: ...Table of Contents 6 3HAC022031 001 Revision C Copyright 2004 2008 ABB All rights reserved ...
Page 191: ......
Page 192: ......
Page 193: ......
Page 194: ......
Page 195: ......
Page 198: ......
Page 199: ......
Page 202: ......
Page 203: ......
Page 205: ......
Page 226: ......