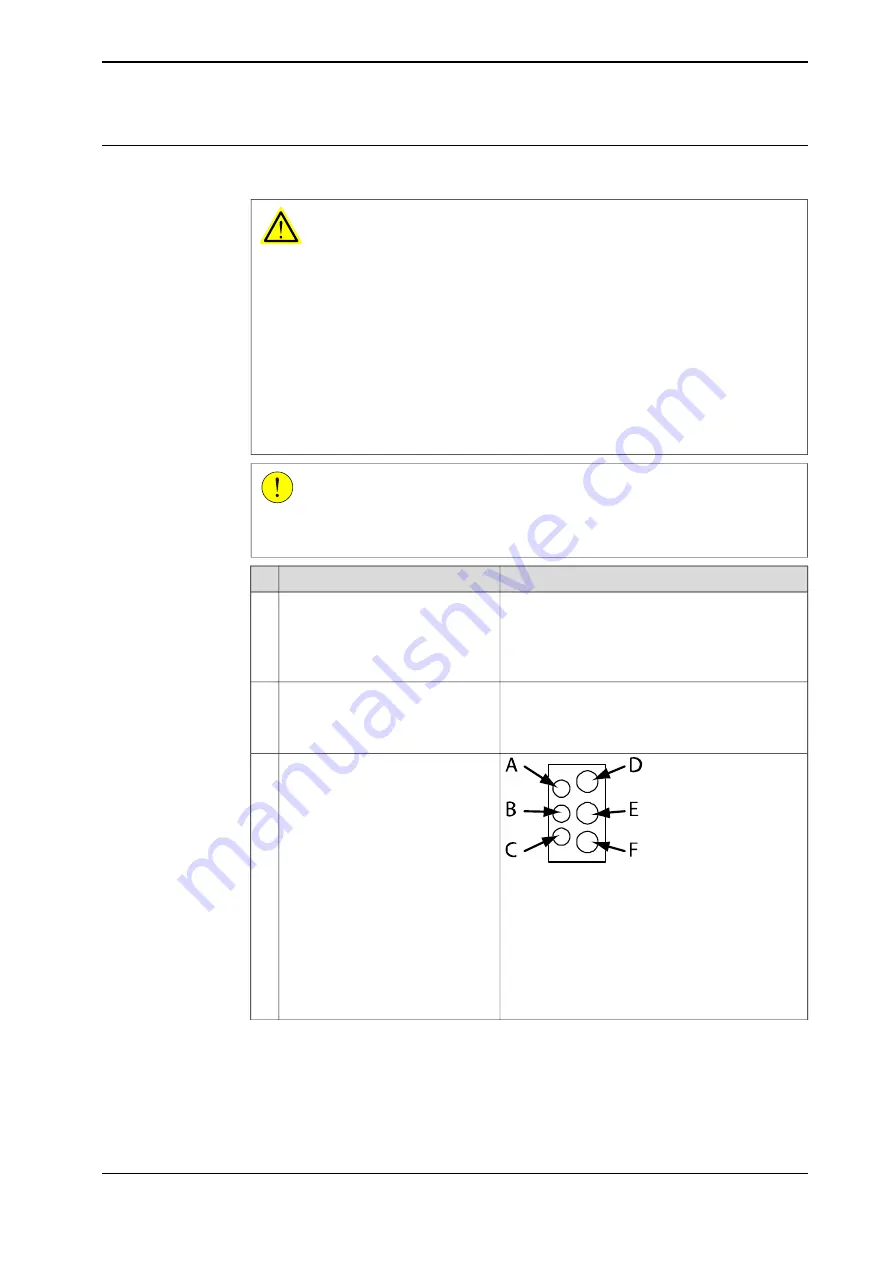
Refitting, cable harness
The procedure below details how to refit the cable harness.
WARNING
Please observe the following before commencing any repair work on the
manipulator:
•
- Motors and gears are
HOT
after running the robot! Burns may result from
touching the motors or gears!
•
- Turn off all electric power, hydraulic and pneumatic pressure supplies to
the robot!
•
- Take any necessary measures to ensure that the manipulator does not
collapse as parts are removed, e.g. to secure the lower arm with fixtures if
removing motor, axis 2.
CAUTION
The cable packs are sensitive to mechanical damage! They must be handled
with care, especially the connectors, in order to avoid damaging them!
Note/Illustration
Action
Refit in reverse order to what is de-
tailed above.
1
Detailed below are some recom-
mendations on how to route the
cables.
Clean the joints that have been
opened. See
face on the robot before replacing
parts on page 118
2
xx0300000093
Cable distribution in the cable
holder in the manipulator base.
3
Cables:
•
A: Signal
•
B: Signal
•
C: Customer signal
•
D: Power cable, axes 4-6
•
E: Pressurized air supply
•
F: Power cable, axes 1-3
Continues on next page
Product manual - IRB 140
125
3HAC027400-001 Revision: V
© Copyright 2004-2018 ABB. All rights reserved.
4 Repair
4.3.1 Replacement of cable harness
Continued
Summary of Contents for IRB 140
Page 1: ...ROBOTICS Product manual IRB 140 ...
Page 8: ...This page is intentionally left blank ...
Page 46: ...This page is intentionally left blank ...
Page 214: ...This page is intentionally left blank ...
Page 228: ...This page is intentionally left blank ...
Page 230: ...This page is intentionally left blank ...
Page 244: ...This page is intentionally left blank ...
Page 250: ......
Page 251: ......