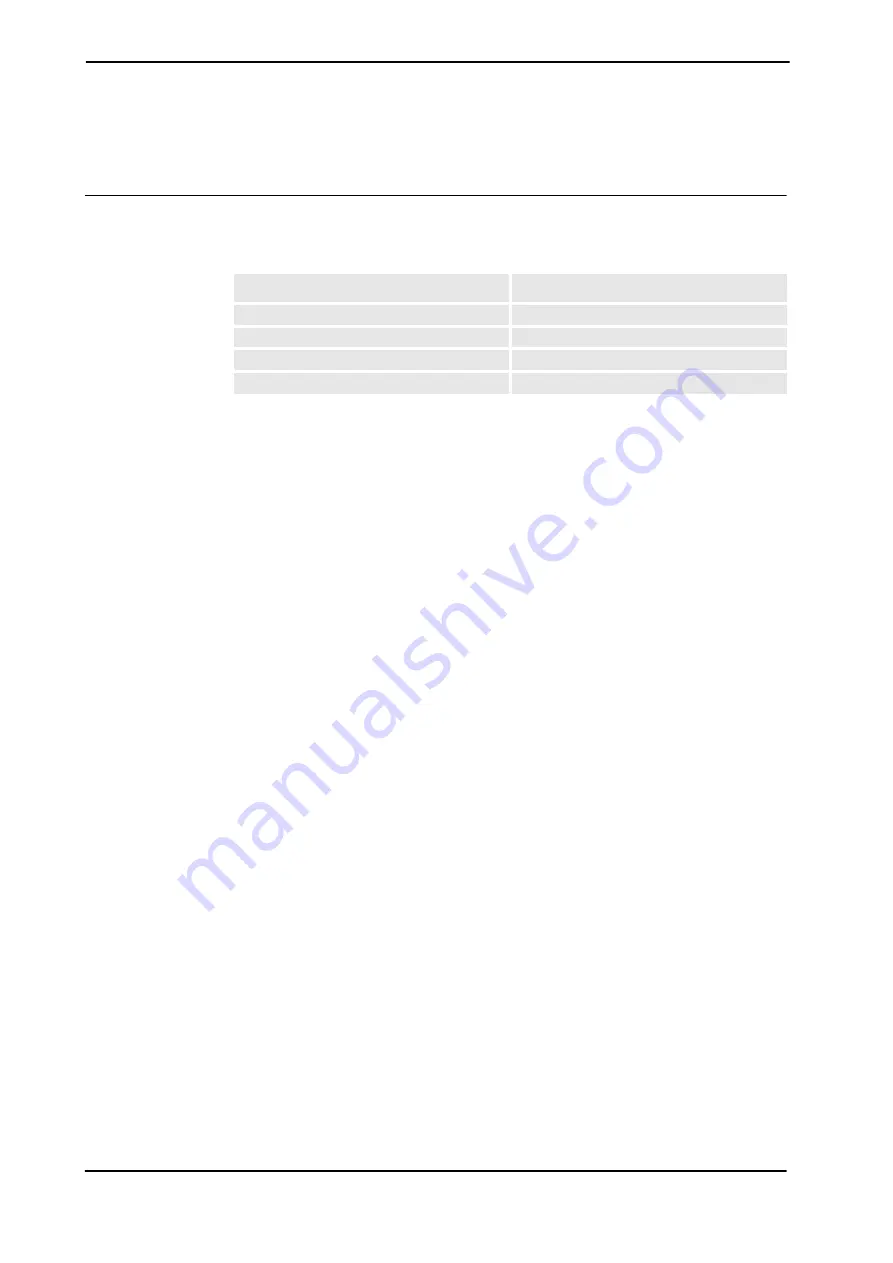
5 Maintenance
5.2. Expected components lifetime
3HAW050027150 Revision: C
66
©
Co
py
rig
h
t 201
3-
101
6 ABB. All righ
ts reser
v
ed.
5.2. Expected components lifetime
General
The expected lifetime of the components can vary greatly depending on how intensively the
feather duster is run.
Item
Maintenance
Cables
1,000,000 cycles
Belt
Over 16,000h
Roller
Over 6 month
Motor
Over 10 years
Summary of Contents for Feather Duster
Page 1: ...Product manual Feather Duster ...
Page 2: ......
Page 12: ...3HAW050027150 Revision C 10 Copyright 2013 1016 ABB All rights reserved ...
Page 92: ... Copyright 2013 1016 ABB All rights reserved ...
Page 100: ... Copyright 2013 1016 ABB All rights reserved ...
Page 110: ......
Page 148: ... Copyright 2013 1016 ABB All rights reserved ...
Page 149: ......