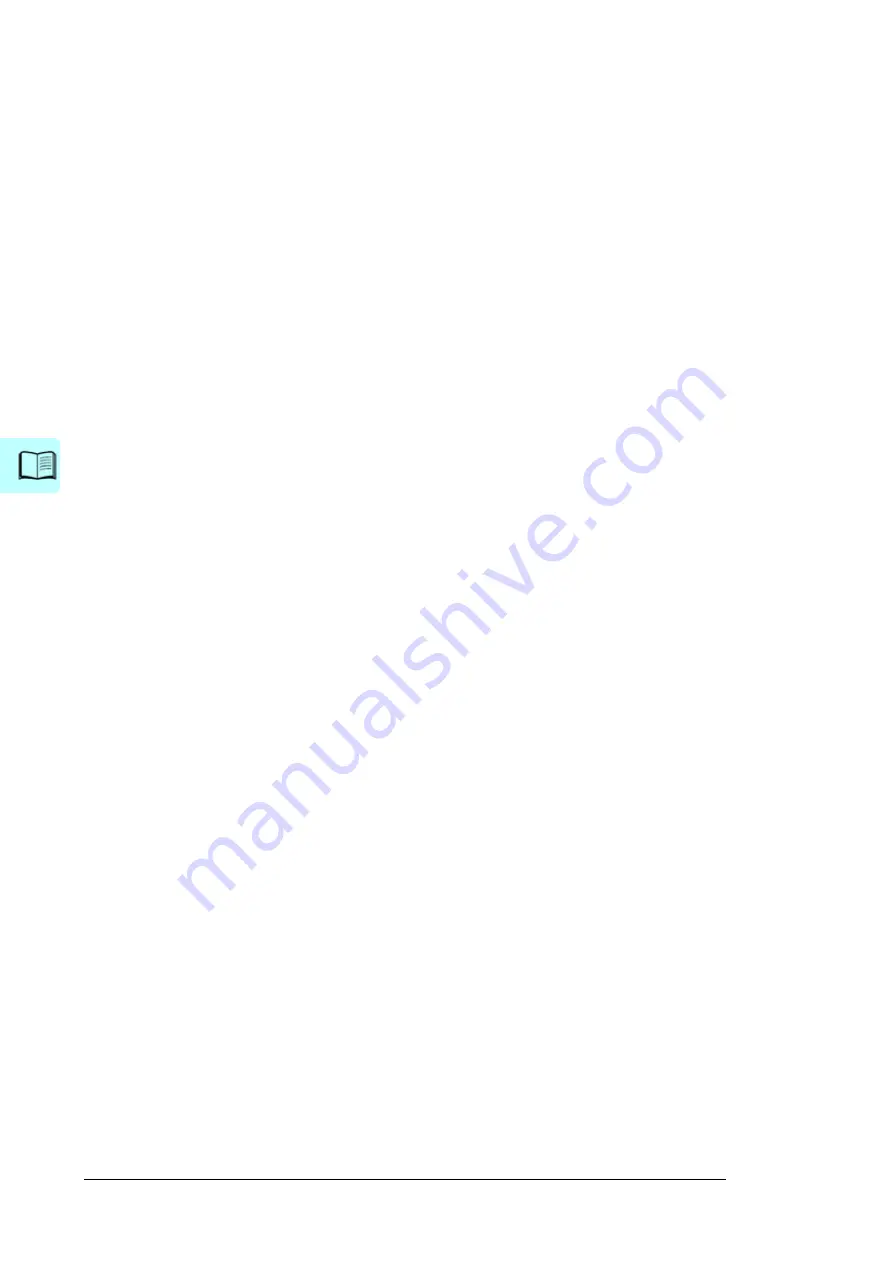
6
Contents of this chapter . . . . . . . . . . . . . . . . . . . . . . . . . . . . . . . . . . . . . . . . . . . . . . . . . 39
Examining the installation site . . . . . . . . . . . . . . . . . . . . . . . . . . . . . . . . . . . . . . . . . . . . 39
Necessary tools . . . . . . . . . . . . . . . . . . . . . . . . . . . . . . . . . . . . . . . . . . . . . . . . . . . . . . . 40
Moving and unpacking the drive . . . . . . . . . . . . . . . . . . . . . . . . . . . . . . . . . . . . . . . . . . 41
Unpacking the transport package . . . . . . . . . . . . . . . . . . . . . . . . . . . . . . . . . . . . . . . 42
Checking the delivery . . . . . . . . . . . . . . . . . . . . . . . . . . . . . . . . . . . . . . . . . . . . . . . . 42
Lifting the cabinet . . . . . . . . . . . . . . . . . . . . . . . . . . . . . . . . . . . . . . . . . . . . . . . . . . . 43
Moving the cabinet after unpacking . . . . . . . . . . . . . . . . . . . . . . . . . . . . . . . . . . . . . 43
Laying the cabinet on its back . . . . . . . . . . . . . . . . . . . . . . . . . . . . . . . . . . . . . . . 43
Moving on rollers . . . . . . . . . . . . . . . . . . . . . . . . . . . . . . . . . . . . . . . . . . . . . . . . . 44
Final placement . . . . . . . . . . . . . . . . . . . . . . . . . . . . . . . . . . . . . . . . . . . . . . . . . . 44
Installing the IP54 roof . . . . . . . . . . . . . . . . . . . . . . . . . . . . . . . . . . . . . . . . . . . . . . . . . . 45
Attaching the cabinet to the floor and wall or roof . . . . . . . . . . . . . . . . . . . . . . . . . . . . . 46
General rules . . . . . . . . . . . . . . . . . . . . . . . . . . . . . . . . . . . . . . . . . . . . . . . . . . . . . . . 46
Attaching methods . . . . . . . . . . . . . . . . . . . . . . . . . . . . . . . . . . . . . . . . . . . . . . . . . . 47
5. Guidelines for planning the electrical installation
Contents of this chapter . . . . . . . . . . . . . . . . . . . . . . . . . . . . . . . . . . . . . . . . . . . . . . . . . 49
Limitation of liability . . . . . . . . . . . . . . . . . . . . . . . . . . . . . . . . . . . . . . . . . . . . . . . . . . . . 49
Selecting the supply disconnecting device . . . . . . . . . . . . . . . . . . . . . . . . . . . . . . . . . . 49
Selecting the main contactor . . . . . . . . . . . . . . . . . . . . . . . . . . . . . . . . . . . . . . . . . . . . . 49
Protecting the motor insulation and bearings . . . . . . . . . . . . . . . . . . . . . . . . . . . . . . . . 50
Examining the compatibility of the motor and drive . . . . . . . . . . . . . . . . . . . . . . . . . . . . 50
Additional requirements for ABB motors of types other than M2_, M3_, M4_, HX_ and
AM_ . . . . . . . . . . . . . . . . . . . . . . . . . . . . . . . . . . . . . . . . . . . . . . . . . . . . . . . . . . . 52
Additional requirements for ABB high-output and IP23 motors . . . . . . . . . . . . . . 52
Additional requirements for non-ABB high-output and IP23 motors . . . . . . . . . . . 52
Additional data for calculating the rise time and the peak line-to-line voltage . . . 53
Additional note for common mode filters . . . . . . . . . . . . . . . . . . . . . . . . . . . . . . . 53
General rules . . . . . . . . . . . . . . . . . . . . . . . . . . . . . . . . . . . . . . . . . . . . . . . . . . . . . . . 53
Typical power cable sizes . . . . . . . . . . . . . . . . . . . . . . . . . . . . . . . . . . . . . . . . . . . . . 54
Alternative power cable types . . . . . . . . . . . . . . . . . . . . . . . . . . . . . . . . . . . . . . . . . . 54
Summary of Contents for ACS580-07-0495A-4
Page 1: ...ABB general purpose drives Hardware manual ACS580 07 drives 250 to 500 kW ...
Page 4: ......
Page 8: ...4 Update notice ...
Page 16: ...12 ...
Page 24: ...20 Safety instructions ...
Page 42: ...38 Operation principle and hardware description ...
Page 74: ...70 Electrical installation PE PE 8 PE 13 11 7 8 12 13 ...
Page 82: ...78 Electrical installation ...
Page 102: ...98 Fault tracing ...
Page 114: ...110 Maintenance R10 and R11 4 5 2 7 6 3 8 ...
Page 115: ...Maintenance 111 R10 and R11 9 10 ...
Page 116: ...112 Maintenance R10 and R11 11 ...
Page 117: ...Maintenance 113 R10 and R11 12b 12a ...
Page 118: ...114 Maintenance R10 and R11 R10 and R11 17 14 13 R11 15 16 ...
Page 134: ...130 Technical data ...
Page 137: ...Dimension drawings 133 13 Dimension drawings Example dimension drawings are shown below ...
Page 138: ...134 Dimension drawings Frames R10 and R11 IP42 ...
Page 139: ...Dimension drawings 135 Frames R10 and R11 IP54 option B055 ...
Page 140: ...136 Dimension drawings ...
Page 152: ...148 Safe torque off function ...
Page 174: ...Contact us www abb com drives www abb com drivespartners 3AXD50000032622 Rev A EN 2016 03 16 ...