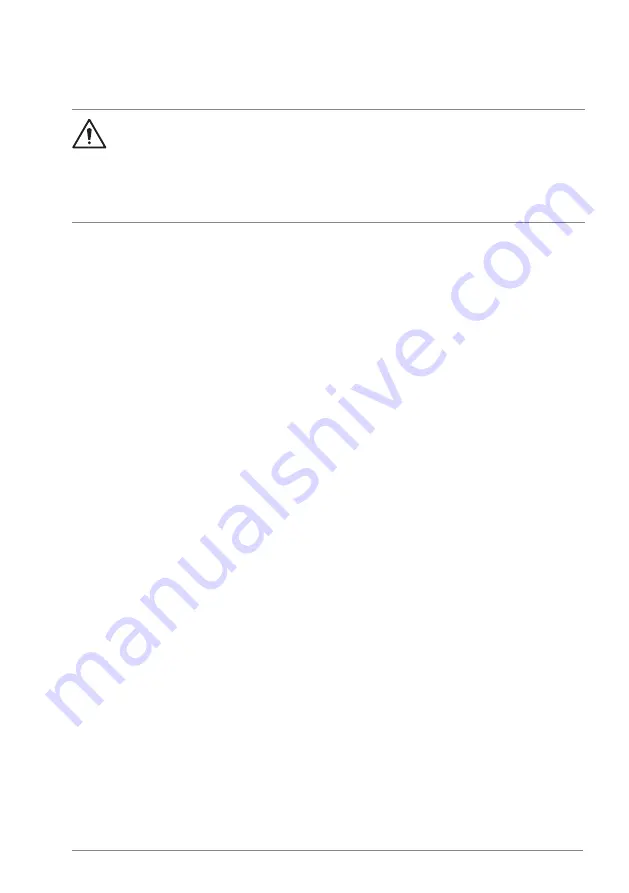
•
the temperature of the space that the resistor is in does not go above the
allowed maximum value.
WARNING!
The materials near the brake resistor must be non-flammable. The surface
temperature of the resistor is high. Air flowing from the resistor is of
hundreds of degrees Celsius. If the exhaust vents are connected to a
ventilation system, make sure that the material withstands high
temperatures. Protect the resistor against contact.
Protecting the system in brake circuit fault situations
■
Protecting the system in cable and brake resistor short-circuit
situations
The drive input fuses will also protect the resistor cable when it is identical with
the input power cable.
■
Protecting the system against thermal overload
The drive has a brake thermal model which protects the brake resistor against
overload. ABB recommends to enable the thermal model at start up.
ABB recommends to equip the drive with a main contactor for safety reasons even
when you have enabled the resistor thermal model. Wire the contactor so that it
opens in case the resistor overheats. This is essential for safety since the drive
will not otherwise be able to interrupt the main supply if the chopper remains
conductive in a fault situation. An example wiring diagram is shown below. ABB
recommends that you use resistors equipped with a thermal switch (1) inside the
resistor assembly. The switch indicates overtemperature.
Resistor braking 157
Summary of Contents for ACS180-04S-03A7-1
Page 1: ...ABB MACHINERY DRIVES ACS180 drives Hardware manual...
Page 2: ......
Page 4: ......
Page 12: ...12...
Page 24: ...24...
Page 84: ...84...
Page 96: ...96...
Page 146: ...146...
Page 148: ...Frame R0 148 Dimension drawings...
Page 149: ...Frame R1 Dimension drawings 149...
Page 151: ...Frame R3 Dimension drawings 151...
Page 152: ...Frame R4 152 Dimension drawings...
Page 160: ...160...
Page 180: ...Declarations of conformity 180 The Safe torque off function...
Page 181: ...The Safe torque off function 181...
Page 182: ...182 The Safe torque off function...
Page 183: ...The Safe torque off function 183...
Page 184: ...184...
Page 187: ...Installation 1 2 N m M4x16 2x 3 3 3 2 2 2 2 Accessories 187...
Page 189: ...Installation 3 3 2 2 2 3 2 2 N m M4x16 4x 1 Accessories 189...