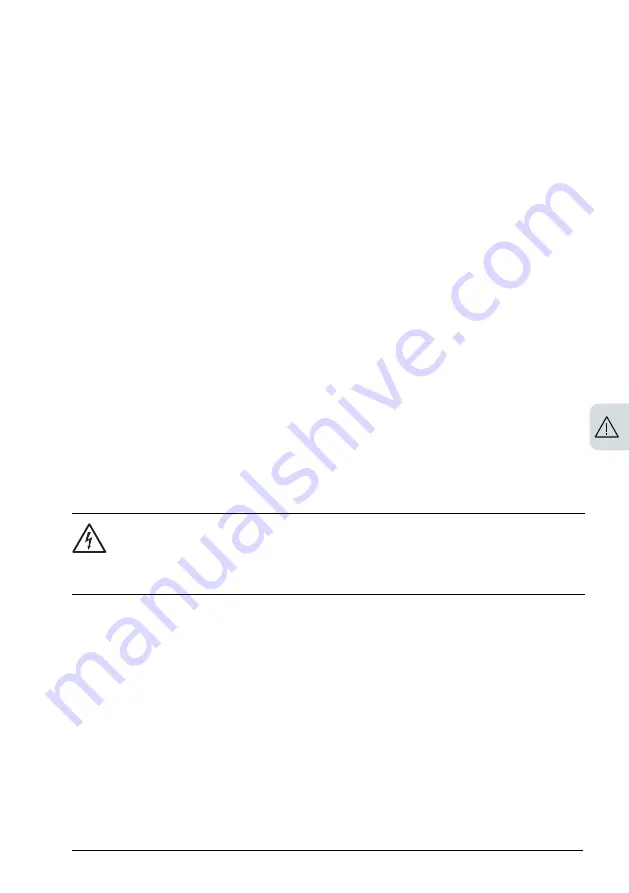
Before installation, start-up and maintenance work on the drive:
•
Stop the drive.
•
Disconnect the motor from the drive with a safety switch or by other means.
•
If you cannot disconnect the motor, make sure that the motor cannot rotate during
work. Make sure that no other system, like hydraulic crawling drives, can rotate the
motor directly or through any mechanical connection like felt, nip, rope, etc.
•
Do the steps in section
Electrical safety precautions (page 17)
.
•
Measure that the installation is de-energized.
•
Use a multimeter with an impedance greater than 1 Mohm.
•
Make sure that the voltage between the drive input power terminals (L1, L2, L3)
and the grounding (PE) busbar is close to 0 V.
•
Make sure that the voltage between the drive output terminals (T1/U, T2/V,
T3/W) and the grounding (PE) busbar is close to 0 V.
•
Make sure that the voltage between the drive DC terminals (R+/UDC+ and
UDC-) and the grounding terminal (PE) is close to 0 V.
•
Install temporary grounding to the drive output terminals (T1/U, T2/V, T3/W). Connect
the output terminals together as well as to the PE.
During the start up:
•
Make sure that the motor cannot run overspeed, for example, driven by the load.
Motor overspeed causes overvoltage that can damage or destroy the capacitors in
the intermediate circuit of the drive.
■
Safety in operation
WARNING!
Make sure that the motor cannot run overspeed, for example, driven by the load.
Motor overspeed causes overvoltage that can damage or destroy the capacitors
in the intermediate circuit of the drive.
Safety instructions 21
Summary of Contents for ACH480
Page 1: ... ABB DRIVES FOR HVAC ACH480 drives Hardware manual ...
Page 2: ......
Page 4: ......
Page 14: ...14 ...
Page 22: ...22 ...
Page 28: ...28 ...
Page 38: ...38 ...
Page 44: ...44 ...
Page 60: ...60 ...
Page 86: ...86 ...
Page 110: ...110 ...
Page 114: ...114 ...
Page 122: ...122 ...
Page 156: ...Frame R1 Frame R1 front side IP20 UL open type 156 Dimension drawings ...
Page 157: ... Frame R1 bottom rear IP20 UL open type Dimension drawings 157 ...
Page 158: ... Frame R1 front side UL Type 1 kit installed 158 Dimension drawings ...
Page 159: ... Frame R1 bottom rear UL Type 1 kit installed Dimension drawings 159 ...
Page 160: ...Frame R2 Frame R2 front side IP20 UL open type 160 Dimension drawings ...
Page 161: ... Frame R2 bottom rear IP20 UL open type Dimension drawings 161 ...
Page 162: ... Frame R2 front side UL Type 1 kit installed 162 Dimension drawings ...
Page 163: ... Frame R2 bottom rear UL Type 1 kit installed Dimension drawings 163 ...
Page 164: ...Frame R3 Frame R3 front side IP20 UL open type 164 Dimension drawings ...
Page 165: ... Frame R3 bottom rear IP20 UL open type Dimension drawings 165 ...
Page 166: ... Frame R3 front side UL Type 1 kit installed 166 Dimension drawings ...
Page 167: ... Frame R3 bottom rear UL Type 1 kit installed Dimension drawings 167 ...
Page 168: ...Frame R4 Frame R4 front side IP20 UL open type 168 Dimension drawings ...
Page 169: ... Frame R4 bottom rear IP20 UL open type Dimension drawings 169 ...
Page 170: ... Frame R4 front side UL Type 1 kit installed 170 Dimension drawings ...
Page 171: ... Frame R4 bottom rear UL Type 1 kit installed Dimension drawings 171 ...
Page 172: ...172 ...
Page 180: ...180 ...
Page 198: ... Declaration of conformity 198 The Safe torque off function ...
Page 206: ...Dimensions 206 BIO 01 I O extension module ...
Page 212: ...Dimensions 3AXD50000031148 rev A 212 BREL 01 relay output extension module ...