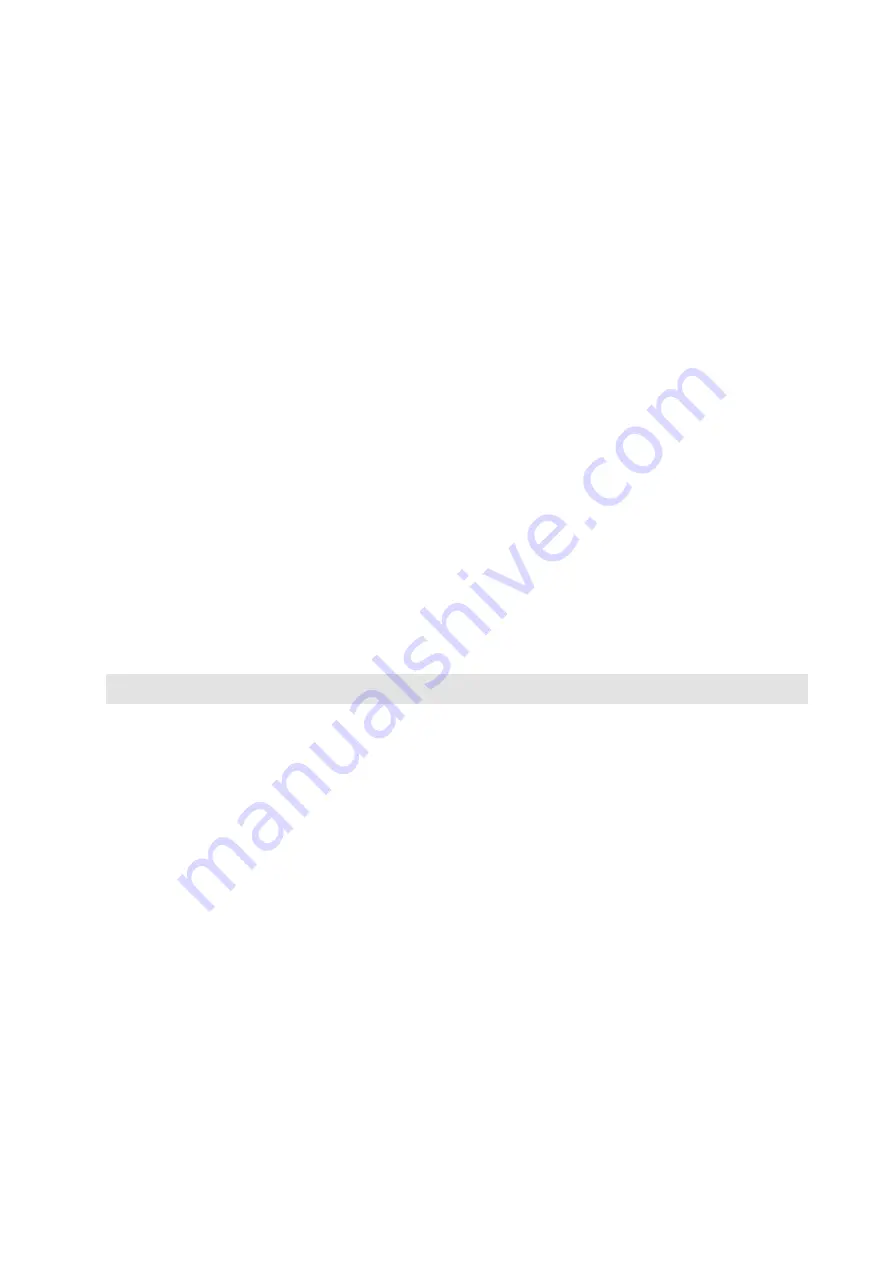
6
Self-locking
The actuator is self-locking provided that the load only acts in the direction against motion of the actuator output shaft.
Self-locking is ensured by a roller arrest immobilizing the electric motor rotor even in the case of manual control.
In order to observe safety regulations, the actuators cannot be used for driving transportation lifting devices with
possible transport of persons or for installations where persons can stand under the lifted load.
Sense of rotation
When looking at the output shaft in the direction towards the control box, the CLOSE direction of rotation is identical
with the clockwise sense.
Working stroke
The ranges of working stroke are given in Table No. 1 or No. 2.
Rising spindle
In the design variants with connecting dimensions, Shapes A and C, the actuators can be adapted for mounting
to the valve with a rising spindle that projects over the upper end of the actuator output shaft in the end position
of the valve. The space reserved for the rising spindle is clearly shown in the dimensional sketches. The user should
mount a cylindrical guard of the rising spindle instead of the port cover at the control box top, if required. This guard
has not been included in the delivery of the actuator.
Manual control
Manual control is performed directly by a handwheel
(without clutch).
It can be used even when the electric
motor is running
(the resulting motion of the output shaft is determined by the function of the differential gear).
When the handwheel is rotated clockwise the output shaft of the actuator also rotates clockwise
(when looking at
the shaft towards the control box).
On condition that the valve nut is provided with left-hand thread, the actuator
closes the valve.
Torque-limit switches in the actuator are set and work when the actuator is under voltage.
When using the manual control, ie. actuator is controlled mechanically, the torque-limit switches
doesn´t work and the valve can be damaged.
5. ACTUATOR OUTFIT
Position indicator
The actuator can be fitted with a display as an option for electronic system DMS2 ED. Actuator with electronic
system DMS2 is equipped with two-line display.
Anti-condensation heater
Anti-condensation heater is connected to DMS and DMS ED electronic circuit. Switching of the anti-condensation
heater is controlled by a thermostat. From the factory is the switching temperature set to 10°C. The temperature is
adjustable by adjusting software DMS2. Input power of the anti-condensation heater is 10W / 230V.
Local control
Local control serves for controlling the actuator from the site of its installation. It includes two change-over switches:
one with positions “Remote control - Off - Local control”, the other “Open - Stop - Close”.
The former change-over switch can be built-in as two-pole or four-pole. The change-over switches are installed
in a terminal-board box and the control elements on the lid of this terminal-board box.
Dynamic brake
The brake is an optional accessory to the actuators fitted with electronics
DMS2 and DMS2 ED Control. As
switching elements are used contactors
(mechanical contacts)
or SSR
(modern contactless switching elements).
After opening the switching element
(contactor or SSR),
it induces dynamic braking moment in the motor for several
tenths of second. During the rest period of the actuator no braking torque is developed. The brake reduces dramatically
time of the actuator run-down and regulation is thus more precise. The used brakes BR2 are controlled, impulse for
action comes form the control unit. Corresponding variant of the brake is chosen according to the electric motor output
and the type of switching elements.