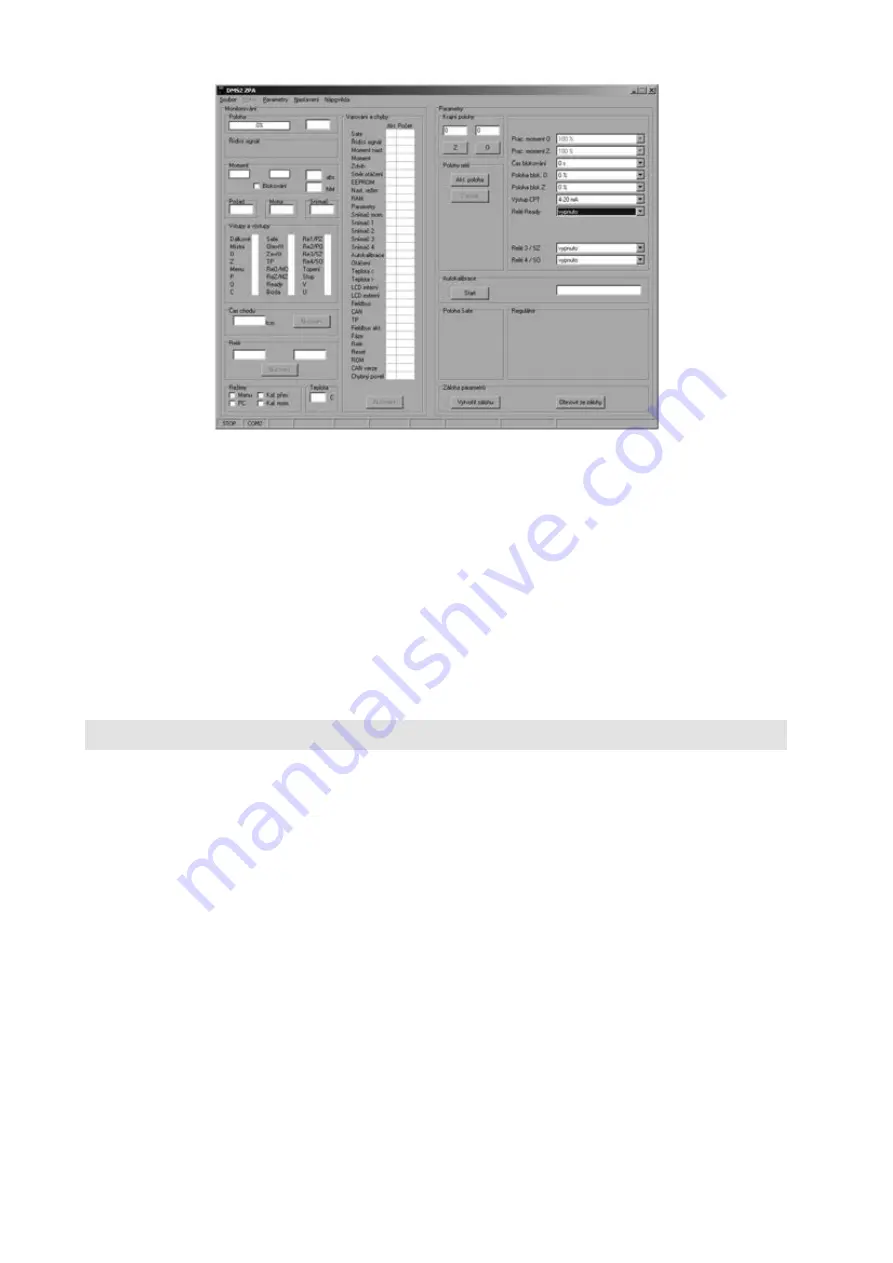
13
MENU 7 – Response in case of losing control signal in three-position regulation
– Shortly press P to select value OPEN
- 1x blinking of LED2,
or CLOSE
- 2x blinking of LED2,
or STOP
- 3x blinking of LED2,
and keep pressing push-button P to store the parameter to memory.
MENU 8 – Way of switching off in end-limit positions in 3P regulation
– Shortly press P to select value TORQUE
- 1x blinking of LED2,
or PO
- 2x blinking of LED2,
or PZ
- 3x blinking of LED2,
PO + PZ - 4x blinking of LED2,
And keep pressing push-button P to store the parameter to memory.
PROCEDURE OF SETTING PARAMETERS BY PROGRAM DMS2
– Before starting the actuator, it is necessary to set some parameters of the system by means of program
DMS2 on PC.
– For safety reasons, the system is delivered in the state of induced error of Calibration when the functions are
limited in order to reduce the risk of damaging the actuator by wrong wiring. In controlling the actuator from program
DMS2, its run is stopped when any torque is induced.
Working torque
– Check and, if necessary, set the value of working torque 50 – 100 % in program DMS2, which you change only
after consultation with the armature manufacturer.
Record of positions OPEN, CLOSED and AUTOCALIBRATION
The actuator should be adjusted so that the recorded position would stop the actuator before it is switched off
by torque. The actuator is shifted manually or electrically. The actuator in version CONTROL can be started from
menu MOTOR in program DMS2. In this case, the actuator does not respond to the set position and is switched
off by torque. In controlling from menu MOTOR, no torque may be induced. The torque should be left manually.
Record of position CLOSED:
– In the required position, press push-button Z in the program and confirm the approved record.
Record of position OPEN:
– In the required position, press push-button O in the program and confirm the approved record.
Main window of setting program