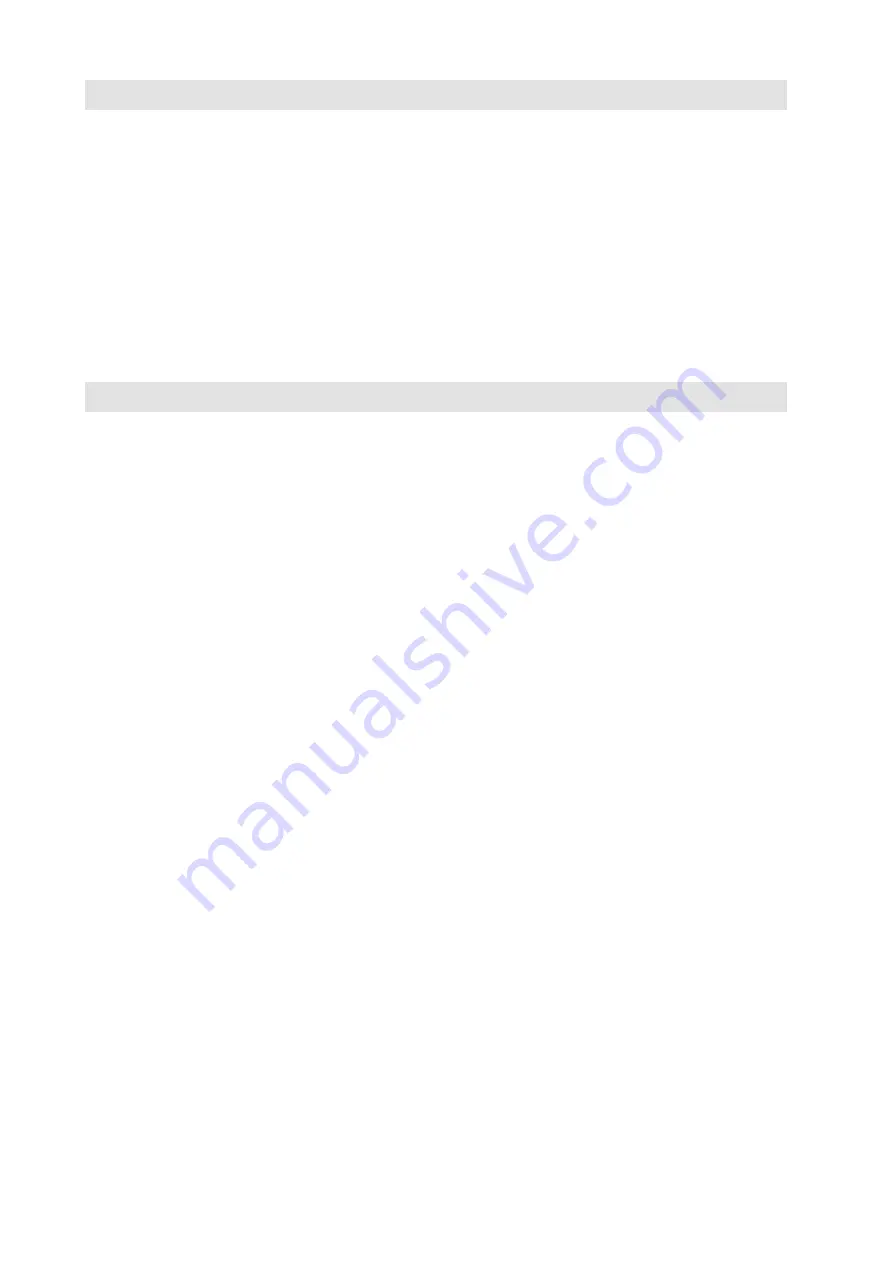
9
8. ELECTRONIC OUTFIT
Electro-mechanical control board is replaced with the electronic system
DMS2 or DMS2 ED. Both systems scan
position of the output shaft and torque of the electric actuator by contact-free magnetic sensors. Long service life is
guaranteed for the contact-free sensors that do not get mechanically worn.
The sensor of the output shaft position is absolute and does not require any backup power supply in case supply
voltage is disconnected during operation of the electric actuator. Both systems can be set and monitored by a computer
with controlling program
(set parameter can be backed up on a computer)
or manually without a computer
(for the
electronics DMS2, parameters can be manually set and it can be checked without computer only if the system is equipped
with a display and local control).
They contain diagnostic functions - error messages on the display, memory of recent
failures and number of occurrences of respective failures.
The more simple system
DMS2 ED substitutes the electro-mechanical board and/or provides for controlling
the electric actuator by input analog signal as in the version Control.
The system
DMS2 enables the electric actuator to be used for two-position and three-position regulation or to be
connected to the industrial bus bar Profibus.
DMS2 ED
Basic outfit:
Control unit
main part of the system DMS2.ED - includes microcomputer, position sensor, 3 signal
lamps LED, 4 push-buttons for simple setting and checking the actuator, connectors for
connecting the torque sensor, source board, and interface RS 232
(connection of
computer for setting and diagnostics).
Torque unit
Source unit
electronic power supply, user's terminal board
(connection of power supply and control signals)
,
2 torque relays, 2 position relays, 2 signalling relays, 1 relay for signalling errors
(READY),
switch of resistance anti-condensation heater, connectors for connecting electronic brake,
resistance heater of analog module, and connector for interconnection with the control unit.
Optional outfit:
Analog module
output of feed-back signal 4 – 20 mA, in version CONTROL input of control signal 0/4 – 20 mA
Position indicator
LED display
Local control
Reversing relays
Parameters:
Scanning of position
contact-less, magnetic
Scanning of torque
contact-less, magnetic
Working stroke
see Tables 1, 2
Torque blocking
0 – 20 s at reversing in limit positions
Input signal
0
(4)
– 20 mA with switched on regulator function
Local/Remote control, Local open/close
Output signal
7 x relay 250 V AC, 3 A
(MO, MZ, PO, PZ, SO, SZ, READY)
Position signal 4 – 20 mA max. 500
Ω
, active/passive, galvanic-isolated,
LED display
Power supply of electronic
230 V AC, 50 Hz, 4 W, over-voltage category II
Realization:
Replacement of electric-
the provided relay contacts substitute position, torque and signalling micro-switches;
mechanical board
current feed-back signal 4 – 20 mA can also be brought out; the actuator is controlled by
the superior control system with signals
“open”
and
“close”.
CONTROL
The electronics covers also function of the regulator; the output shaft position is controlled
by analog input signal.
Function and setting of output relays
The output relays replace end-limit micro-switches; to some extent, function of the output relays differs according to
chosen mode of electronics or it can be selected, preferably by the setting program.