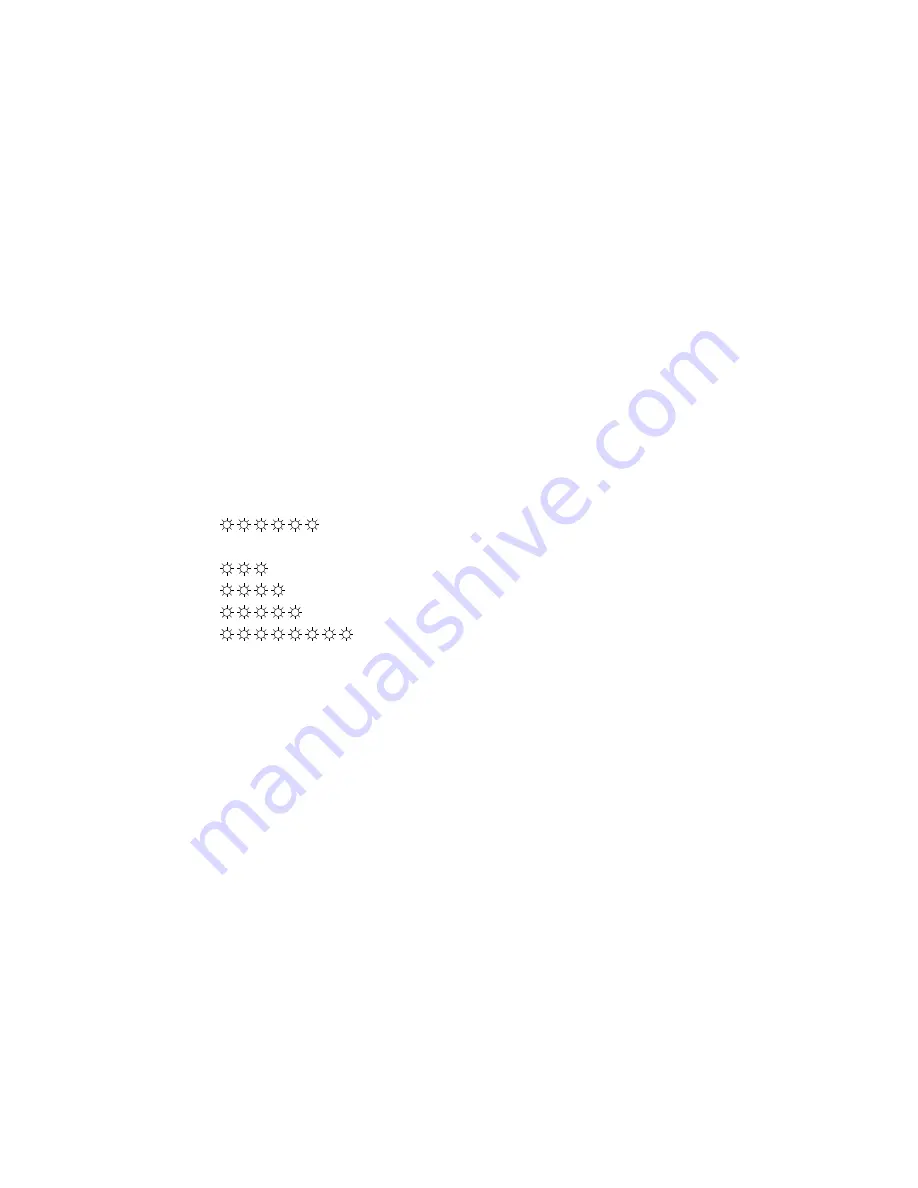
17
By the regulation “to position” the actuator shaft is set to the position in which the input and feedback signals are equal.
The regulation “to moment” means that, in setting the input signal close to limiting positions - for the signal 4 – 20 mA this
is up to the value of about 4.2 mA and above 19.8 mA
(these values are fix set and cannot be changed),
the actuator shaft is
not stopped when the input and feedback signals are equal but it goes on moving until it is stopped by action of the particular
limit switch. Such setting is used in case that tight closing of the valve inthe limit position is safely ensured.
“Narrow” regulation means that, during the regulation, the actuator shaft is set so that the signal from the position
transmitter corresponds exactly to the input signal. In case, after the actuator is stopped, the feedback signal does not
correspond to the input signal the actuator is switched over to the so-called step regime; it reaches an exact position by
repeated switching on and off of the electric motor.
“Broad” regulation means that the actuator shaft is set so that, after the actuator stops, the difference
between the input and feedback signal is smaller or equal to the set range of insensitivity.
If the regulator need not be set otherwise it is recommended to set the way of regulation as “broad to position”.
After setting, checking and possible correcting the parameters, the push-button SW1 should be kept
pressed
(this can be done in any menu)
until the diode D3 is lit on. In this way, setting of parameters is
completed and it is acknowledged that the set parameters are valid and can be stored in the regulator memory.
After releasing the push-button SW1, the auto-calibration is automatically started.
Auto-calibration is an automatic process in which the regulator performs checking of the position transmitter,
sense of rotation of the actuator output shaft, changes over the actuator into the position “Open” and “Closed”,
measures feedback signals in these positions, measures inertia in the direction “Opens” and “Closes”, and
stores the set and measured parameters into the regulator memory.
The auto-calibration should always be started in case of a change of conditions which can influence
the regulator performance, e.g. in case of a change in setting the limit switches of the actuator or a change in
mechanical properties of the valve, e.g. if the gland is tightened.
Menu 6: Auto-calibration (error messages)
D 3
(yellow)
D 4
(red)
no flickering
auto-calibration in progress
auto-calibration starts at the limit switch, failure of limit switch
error in connecting limit switches
position transmitter connected in wrong way or defective
wrong sense of the shaft rotation
In case of wrong connection of the regulator
(limit switches or position transmitter wrongly connected)
the auto-
calibration will be interrupted and the regulator will announce an error by means of the diodes
D3 and D4. If everything
is OK then, after the auto-calibration is completed, the regulator is switched over to the regulation regime.
IMPORTANT!
In case the setting of parameters and auto-calibration have not been accomplished without an error
the set parameters are not stored in the memory of the regulator. After the error is repaired, the setting of
parameters and the auto-calibration can be repeated.
If the regulator parameters are set before the valve with the actuator have been installed on the piping, then, after
their installation and filling the piping with the working medium, properties of the complete can be changed in such
a way that the setting of the regulator and starting of auto-calibration should be repeated.
Program RESET of regulator
If the regulator is brought to a state which is to be cancelled
(RESET),
e.g. for returning from the setting menu without
auto-calibration, this can be accomplished by pressing the push-button
SW1 and keeping it pressed down for at least 6 s.
Note:
If an error occurs in the auto-calibration this procedure does not function: the error conditions should be cancelled
by switching off and on the feeding voltage of the regulator. If the new regulator or the regulator into which wrong
parameters have erroneously been set cannot be started, they can be put into the initial state by switching off
the feeding voltage for about 0.5 min
(to provide for discharging the filtering capacitors in the power supply source);
then, keep pressed both push-buttons on the regulator, with the push-buttons pressed down switch on feeding voltage
to the regulator and keep the push-button pressed down for 6 s. In this way, data which allow putting the regulator into
operation and carrying-out new setting of parameters are counted into the regulator memory.
Содержание MODACT MOK 1000
Страница 2: ...ZPA Pe ky a s is certified company in accordance with ISO 90001 as amended...
Страница 37: ...NOTE...
Страница 38: ...NOTE...